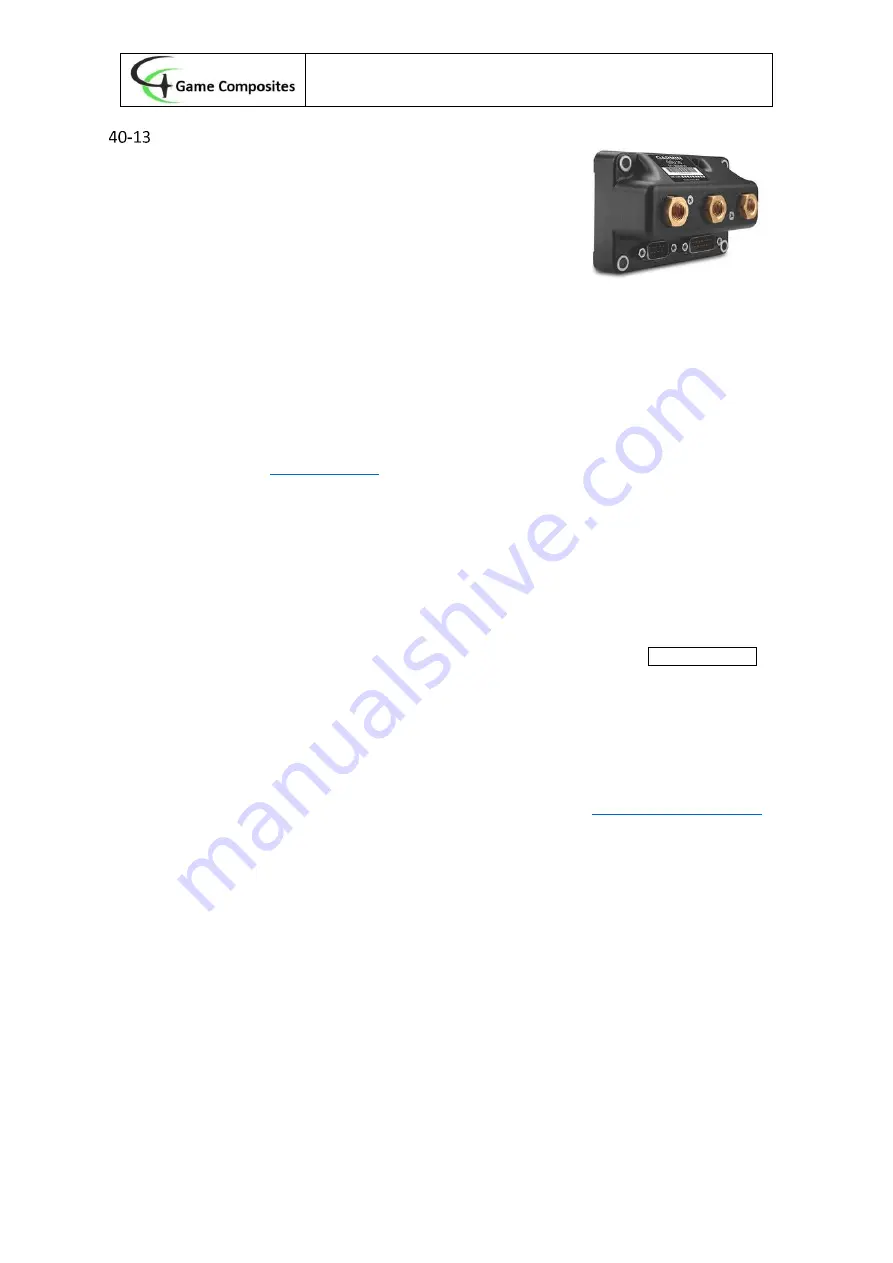
Maintenance Manual GB1 GameBird
Page date: April 24, 2020
40-10
ADAHRS
The GSU 25 is an LRU that provides AHRS and Air Data information in a
single mechanical package. The GSU 25 interfaces to a remote mounted
GMU magnetometer for heading information and also computes OAT and
TAS from inputs provided by the GTP 59.
Electrical power for ADHRS operation is provided via the 35A Avionic CB
Switch, supplied through the Battery Master (essential bus) and 2A AHRS
circuit breaker on the circuit breaker panel, located in the RH side console
in the rear cockpit.
Location:
On vertical Acrotank compartment bulkhead under front instrument panel
Type:
GSU 25C
PN 011-02929-50
Accessories:
GMU 11 install Kit
PN 011-04349-90
Manufacturer:
Garmin International, Inc.
1200 East 151st Street, Olathe, Kansas 66062, USA
Tel: 913.397.8200
Fax: +1 913.397.8282
Aircraft on Ground (AOG) Hotline: +1 913.397.0836
To service the ADAHRS:
1
Remove front instrument panel, refer to section
2
Disconnect pitot- and static lines
3
Disconnect electrical connection: unscrew connector fasteners, pull connector off plug
4
Remove fasteners
5
Remove unit from airplane
6
Service or replace as required
7
To reinstall, reverse steps 1
–
5
8
Conduct pitot-static test, refer to section
Signature
9
Check for correct installation
NOTE:
After installation of a new unit, conduct calibration in accordance with
the Garmin G3X Touch Installation Manual.
No regular maintenance is required for the unit. If defective, the unit must be replaced.
For wiring and connection details, refer to section
Troubleshooting or additional information:
Refer to Garmin G3X Touch Installation Manual, 190-01115-01_AE, available at
Summary of Contents for GB1 GameBird
Page 9: ...Maintenance Manual GB1 GameBird Page date April 24 2020 1 3 OverviewDrawing...
Page 58: ...Maintenance Manual GB1 GameBird Page date April 24 2020 20 8...
Page 70: ...Maintenance Manual GB1 GameBird Page date April 24 2020 24 5 Wiringloom...
Page 71: ...Maintenance Manual GB1 GameBird Page date April 24 2020 24 6...
Page 72: ...Maintenance Manual GB1 GameBird Page date April 24 2020 24 7...
Page 73: ...Maintenance Manual GB1 GameBird Page date April 24 2020 24 8...
Page 74: ...Maintenance Manual GB1 GameBird Page date April 24 2020 24 9...
Page 75: ...Maintenance Manual GB1 GameBird Page date April 24 2020 24 10...
Page 76: ...Maintenance Manual GB1 GameBird Page date April 24 2020 24 11...
Page 77: ...Maintenance Manual GB1 GameBird Page date April 24 2020 24 12...
Page 78: ...Maintenance Manual GB1 GameBird Page date April 24 2020 24 13...
Page 79: ...Maintenance Manual GB1 GameBird Page date April 24 2020 24 14...
Page 80: ...Maintenance Manual GB1 GameBird Page date April 24 2020 24 15...
Page 81: ...Maintenance Manual GB1 GameBird Page date April 24 2020 24 16...
Page 82: ...Maintenance Manual GB1 GameBird Page date April 24 2020 24 17...
Page 83: ...Maintenance Manual GB1 GameBird Page date April 24 2020 24 18...
Page 84: ...Maintenance Manual GB1 GameBird Page date April 24 2020 24 19...
Page 91: ...Maintenance Manual GB1 GameBird Page date April 24 2020 24 26...
Page 139: ...Maintenance Manual GB1 GameBird Page date April 24 2020 28 4...
Page 141: ...Maintenance Manual GB1 GameBird Page date April 24 2020 28 6 Acrotank GB1 2810 00 00 Overview...
Page 188: ...Maintenance Manual GB1 GameBird Page date April 24 2020 40 3 System Schematic...
Page 261: ...Maintenance Manual GB1 GameBird Page date April 24 2020 79 3 OilLines...