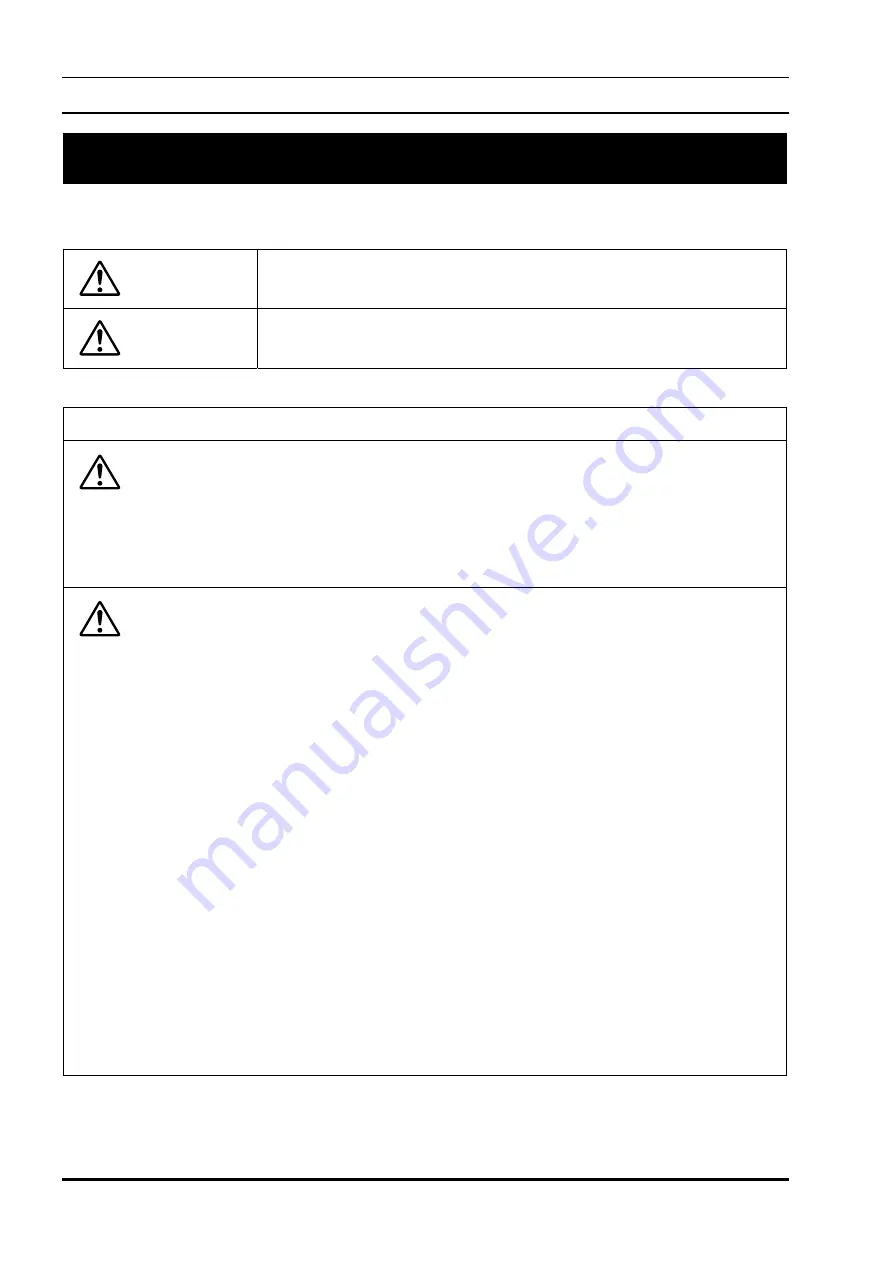
- iv -
INZ-TN7ZSS-E
CAUTION ON SAFETY
First of all, read this “Caution on safety” carefully, and then use the particle counter
in the correct way.
The following items are important for safe operation and must be fully observed. These safety precautions
are ranked in 2 levels; “DANGER” and “CAUTION.”
If operation is incorrect, a dangerous situation may occur, resulting in death
or serious injury.
If operation is incorrect, a dangerous situation may occur, resulting in minor
to medium injuries or only physical damage to equipment.
Caution on installation and transportation
(1)
When the analyzer (receiver unit and transmitter unit) is installed on in-
cineration facility, make sure the facility has stopped completely.
Installing in an operating facility may cause high temperature gas injec-
tion resulting in burn.
(2)
This analyzer is not explosion-proof. Do not use it in an atmosphere of
explosive gas. This may result in serious accidents such as explosion,
fire, etc.
(1)
The analyzer should be installed in a place conforming with the installa-
tion requirements noted in this instruction manual, and where the weight
of the analyzer can be endured. Otherwise, it may cause a tip-over, drop,
electric shocks, fire or malfunction of the unit.
(2)
Ask professional services or your dealer for installation, transportation,
reinstallation, and associated piping and wiring work. Improper installa-
tion may result in a falling accident, electric shock, or injury.
(3)
Check the installation site once every 6 months to make sure that the in-
stallation surface is free of rattling. If the instrument is used under inse-
cure installation conditions, a falling accident may occur.
(4)
During installation, make sure that the inside of the unit is free from ca-
ble chips and other foreign objects. Otherwise, it may cause fire, failure
or malfunction.
(5)
For lifting the gas analyzer, be sure to wear protective gloves. Bare hands
may leave you prone to injury. If the temperature in the installation site is
high, it is imperative to wear leather gloves to prevent burn.
(6)
The analyzer is heavy. It should be transported carefully by two or more
persons if manually required. Otherwise, bodily harm may ensue.
(7)
Do not look into the transmitter unit or direct the laser beam to the eyes
of people while the power is turned ON. Otherwise, the laser beam may
damage cornea of the eye.
(8)
The laser beam is the invisible infrared light. Do not watch the laser
beam directly or scattering light.
(9)
Do not watch the laser beam directly with the optical measuring device.
Otherwise, it may cause serious damage to your eyes.
DANGER
CAUTION
DANGER
CAUTION
Summary of Contents for ZSS-7
Page 1: ......
Page 109: ...102 INZ TN7ZSS E APPENDIX 2 CODE SYMBOLS...
Page 114: ...INZ TN7ZSS E 107 13 BNC cable for optical axis adjustment...
Page 116: ......