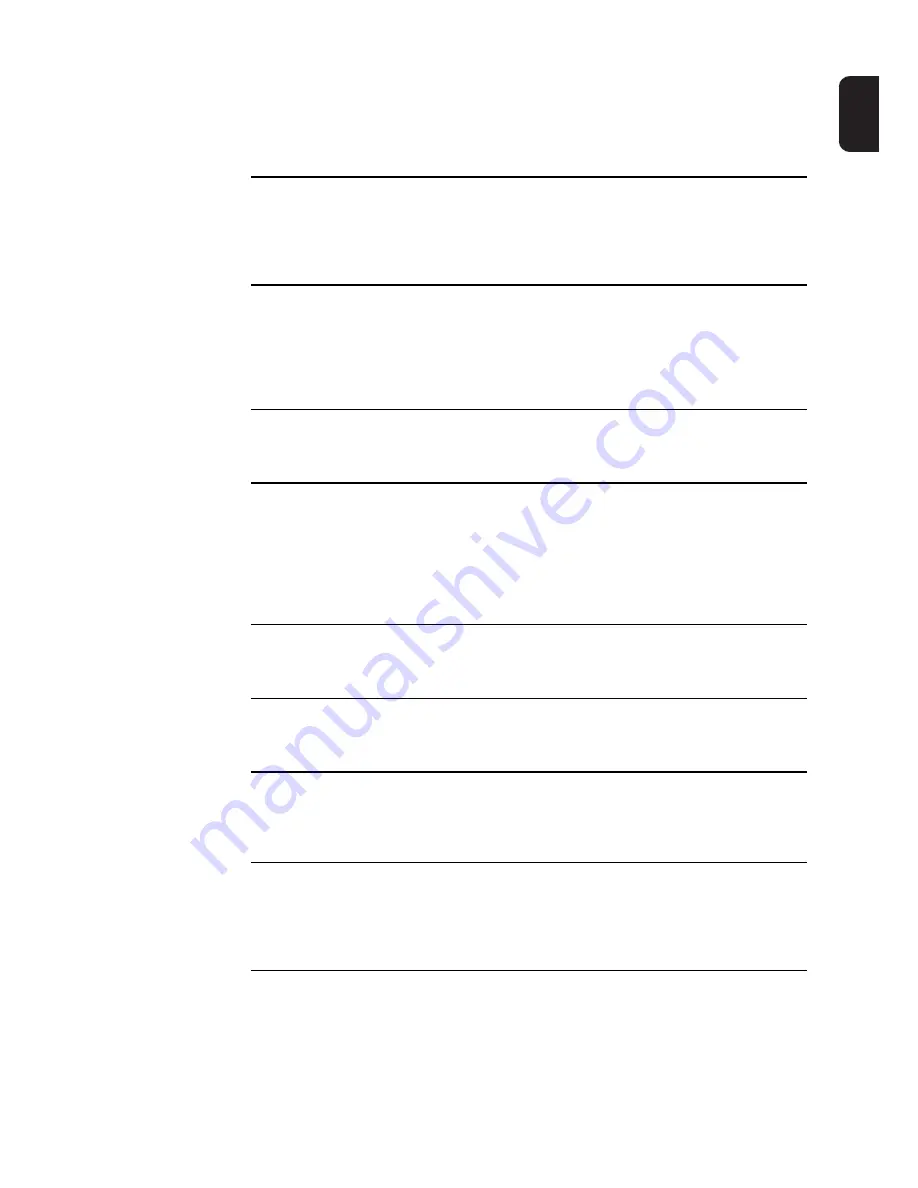
103
EN
tu7 | xxx
Note: xxx stands for a temperature value
Cause:
Undertemperature in the power source
Remedy:
Place power source in a heated room and allow it to warm up
no | H2O
Cause:
Coolant flow rate too low
Remedy:
Check coolant flow rate and cooling unit, including cooling circuit (for mini-
mum coolant flow, see "Technical Data" section in the device operating in-
structions)
hot | H2O
Cause:
The coolant temperature is too high
Remedy:
Allow cooling unit and cooling circuit to cool down, until "hot | H2O" is no
longer displayed. Open the cooling unit and clean the cooler, check fan is
working properly. Robot interface or field bus coupler: before resuming weld-
ing, set the "Source error reset" signal.
no | Prg
Cause:
No preconfigured program has been selected
Remedy:
Select a configured program
no | IGn
Cause:
"Ignition time out" function is active; no current started flowing before the
length of wire specified in the set-up menu had been fed. The power source
safety cut-out has tripped.
Remedy:
Shorten the wire end; press the torch trigger again; clean the surface of the
workpiece; if necessary, increase the wire length until the safety cut-out trips
in "Set-up menu: Level 2".
EPG | 17
Cause:
The welding program selected is invalid
Remedy:
Select valid welding program
EPG | 29
Cause:
The required wire-feed unit is not available for the selected characteristic
Remedy:
Connect correct wire-feed unit, check plug connections for the hosepack
EPG | 35
Cause:
Measurement of the welding circuit resistance "r" failed
Remedy:
Check grounding cable, current cable or hosepack and replace if necessary,
recalculate welding circuit resistance "r"
no | GAS
Cause:
The Gas watchdog option has detected that there is no gas pressure
Remedy:
Connect a new gas cylinder or open the gas cylinder valve/pressure regulator,
restart "Gas watchdog" option, reset "no | GAS" error message by pressing
any button.
Summary of Contents for TransSteel 2500c
Page 2: ...2...
Page 4: ...4...
Page 8: ...8...
Page 20: ...20...
Page 21: ...General information...
Page 22: ......
Page 29: ...Control elements and connections...
Page 30: ......
Page 39: ...Installation and commissioning...
Page 40: ......
Page 49: ...49 EN 3 4 3 4 IMPORTANT Tie the phase conductors near the luster terminal using cable ties...
Page 63: ...Welding...
Page 64: ......
Page 77: ...77 EN Number 3 Number 4 Number 5...
Page 78: ...78...
Page 79: ...Setup settings...
Page 80: ......
Page 93: ...Troubleshooting and maintenance...
Page 94: ......
Page 105: ...105 EN Disposal Dispose of in accordance with the applicable national and local regulations...