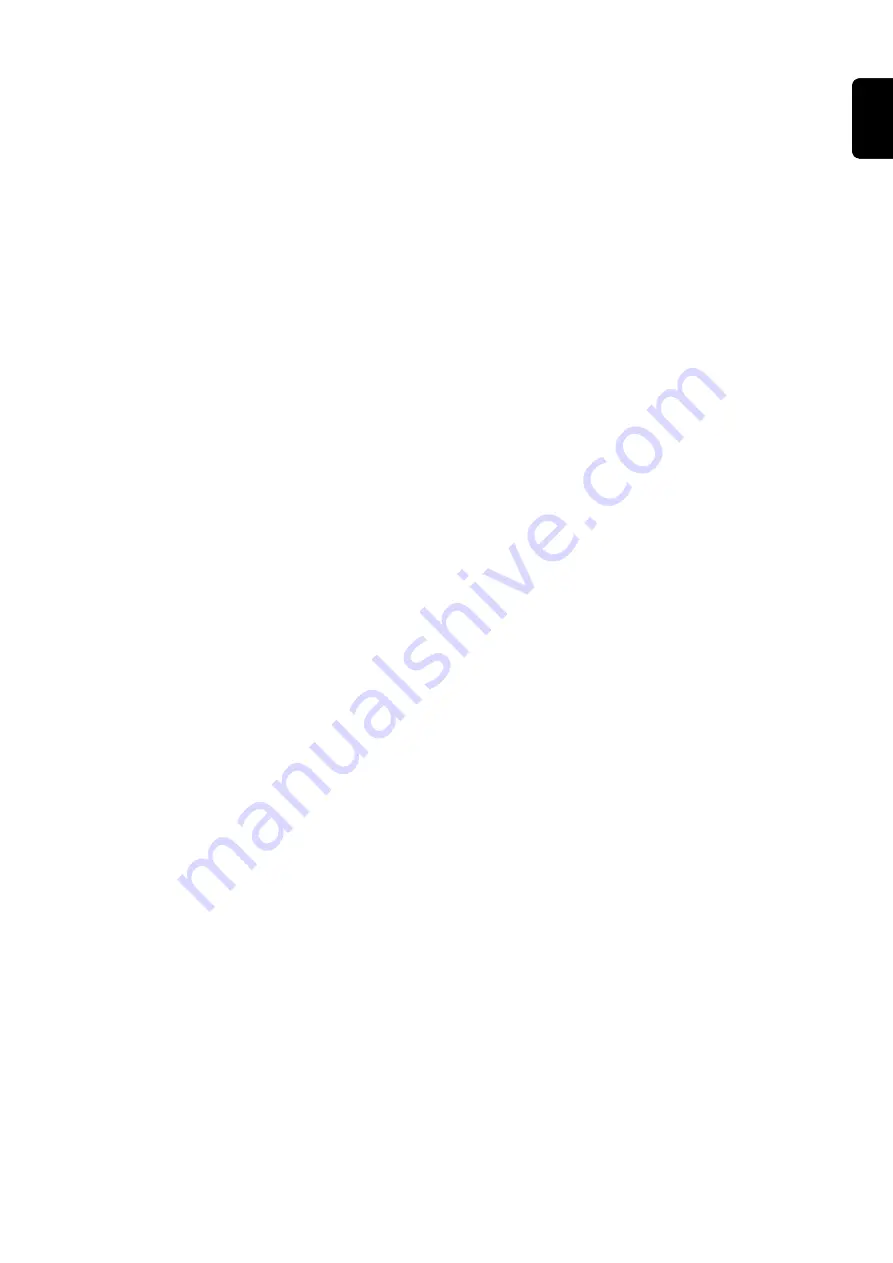
-
If the cleaning device wire cutter does not respond to the movement of the
valve lever, the cleaning device (including the wire cutter) is depressurised
-
If the wire cutter responds to the movement of the valve lever, the cleaning
device (and therefore also the wire cutter) is still connected to a compressed
air supply.
If this is the case, you must disconnect the cleaning device from the com-
pressed air supply and check again that the cleaning device is depressurised
before starting work
35
EN
Summary of Contents for Robacta Reamer Alu 3000upm
Page 2: ......
Page 12: ...12...
Page 13: ...General 13...
Page 14: ...14...
Page 23: ...Controls connections and mechan ical components 23...
Page 24: ...24...
Page 30: ...30...
Page 31: ...Installation and commissioning 31...
Page 32: ...32...
Page 40: ...Attach the spatter tray retainer as shown 3 40...
Page 67: ...Care maintenance and disposal 67...
Page 68: ...68...
Page 73: ...Troubleshooting 73...
Page 74: ...74...
Page 80: ...80...
Page 81: ...Technical data 81...
Page 82: ...82...
Page 85: ...Appendix 85...
Page 86: ...86...