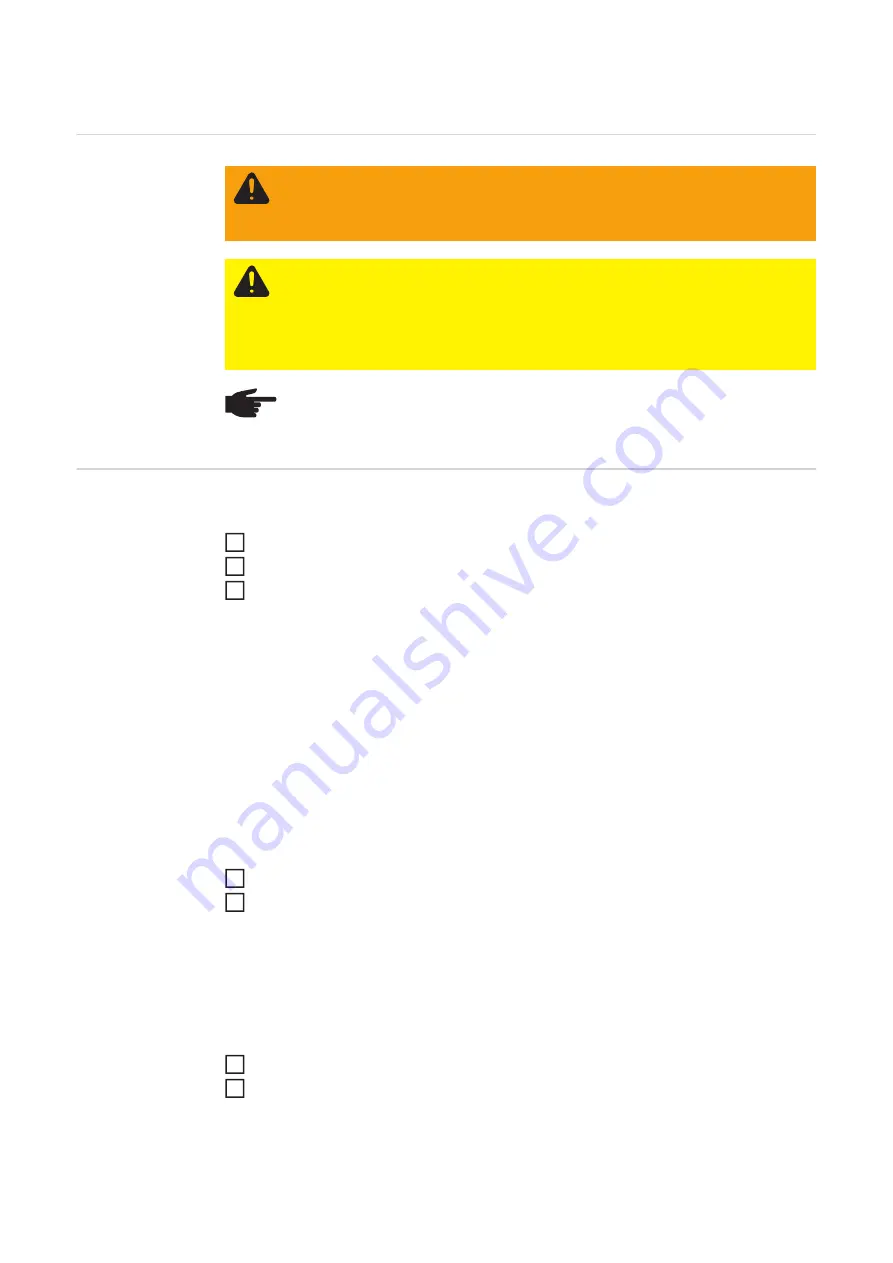
72
Signal sequence for LaserHybrid welding
Safety
Signal sequence
for LaserHybrid
welding
Robot start position:
Set the "extraction on" signal
Set the "crossjet on" signal
Select the mode
e.g. mode "3" (internal parameter selection for adjustment purposes):
set mode bit "0" to "1"
set mode bit "1" to "1"
set mode bit "2" to "0"
If "Job" mode is selected, see the operating instructions for the MIG/MAG power
source for more detailed information about this mode.
If preheating is not required, continue from "LaserHybrid welding start position".
Preheating start position:
Requirement: the laser must be ready to enable the beam.
Set the "gas test" signal
Set the "laser on" signal
The preheating temperature comes from the following factors:
travel speed,
laser power,
distance to the surface of the workpiece
Preheating end position:
Reset the "laser on" signal
Reset the "gas test" signal
WARNING!
Work that is carried out incorrectly can cause serious injury or dam-
age. The welding sequence must only be programmed by trained specialist per-
sonnel. Observe the safety rules in the operating instructions, paying particular
attention to the section entitled "Safety inspection".
CAUTION!
Risk of damage to optical fibre if laser welding head is positioned per-
pendicular to the surface of the workpiece during welding.
If the laser optics system is placed at a right angle to the surface of the workpiece,
the laser will be reflected directly into the laser optics system. The optical fibre can
be seriously damaged if this occurs.
Always set the laser welding head at a forwards or backwards tilt angle.
NOTE!
When welding a number of short weld seams one after the other, do not
switch off the crossjet flow and external extraction until the end of the entire se-
quence. This will prevent welding smoke from making the protective glass dirty.
1
2
3
1
2
1
2
Summary of Contents for LaserHybrid Ultracompact Twin
Page 2: ...2...
Page 4: ...4...
Page 8: ...8...
Page 18: ...18...
Page 19: ...General information...
Page 20: ......
Page 34: ...34...
Page 35: ...Control elements and connections...
Page 36: ......
Page 41: ...Start up...
Page 42: ......
Page 76: ...76...
Page 77: ...Maintenance...
Page 78: ......
Page 94: ...94 3 Position the gas nozzle and secure using a 2 5 mm Al len key Tightening torque 1 Nm 5...
Page 96: ...96 Fit the spatter guard plate using two Al len screws 3 mm 2 2 2...
Page 110: ...110...
Page 111: ...Appendix...
Page 112: ......
Page 114: ...114 Spare parts list LaserHybrid Ultracompact Twin...
Page 115: ...115...
Page 116: ...116...
Page 118: ...118...
Page 119: ...119...