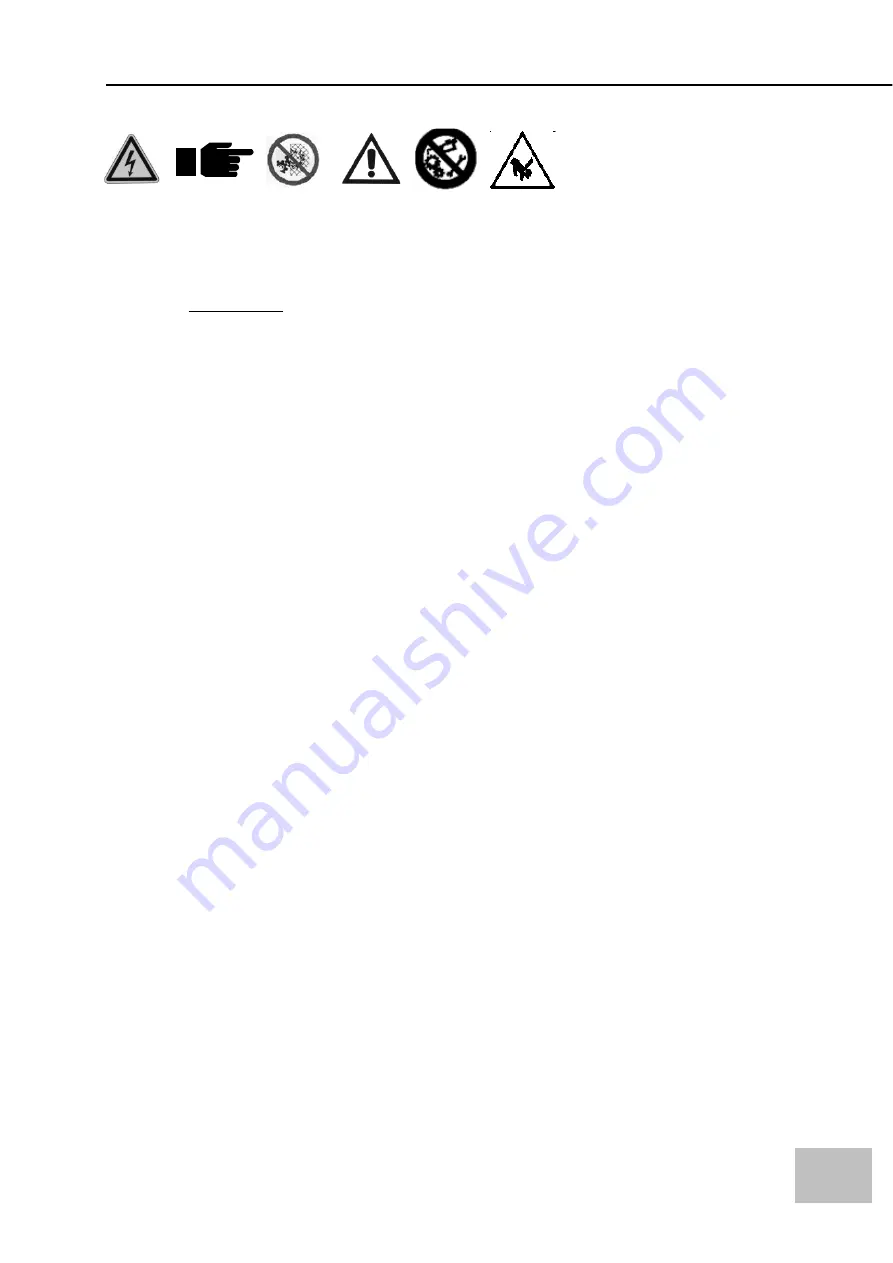
FS4.1893-Manual-30.18XX.02-EN-Version02_R1
FROMM
It is forbidden to duplicate this manual or parts of it in any way or any form without written permission of the author © 2013
www.fromm-stretch.com
47
STARTING AND STOPPING OF THE TURNTABLE WRAPPING CYCLE
Automatic run mode with settable cycles
Activate this run mode, after the machine has been turned on and the safety conditions have been
complied with, by pressing the START pushbutton provided that the corresponding work cycle has
been set via the pushbutton panel.
ATT.
The acoustic signal is active during approximately 3 seconds before the automatic wrapping cycle
will be executed. The machine will only start to operate after this period has been elapsed.
N.B
.
The automatic wrapping cycle is only started, if the start conditions are fulfilled.
A failure indication is displayed, if not all start conditions are fulfilled.
The start conditions for the automatic wrapping cycle are:
-
One of the WRAPPING PROGRAMS 1 - 30 should be selected;
-
Photocell "pallet height" should be activated;
-
Emergency stop not activated;
-
No failure detected;
Stop with table deceleration
This stop is commanded as follows:
- by pressing the stop pushbutton
- by pressure exerted on the crush-proof guard
- by the presence of an alarm that commands the immediate stop.
This stop mode envisages:
- the immediate stop of the film carriage
- the turnplate starts to slow down until it stops.
NOTE
: with this type of stop the machine can restart from the operating point in which it had stopped
by, pressing the start button.