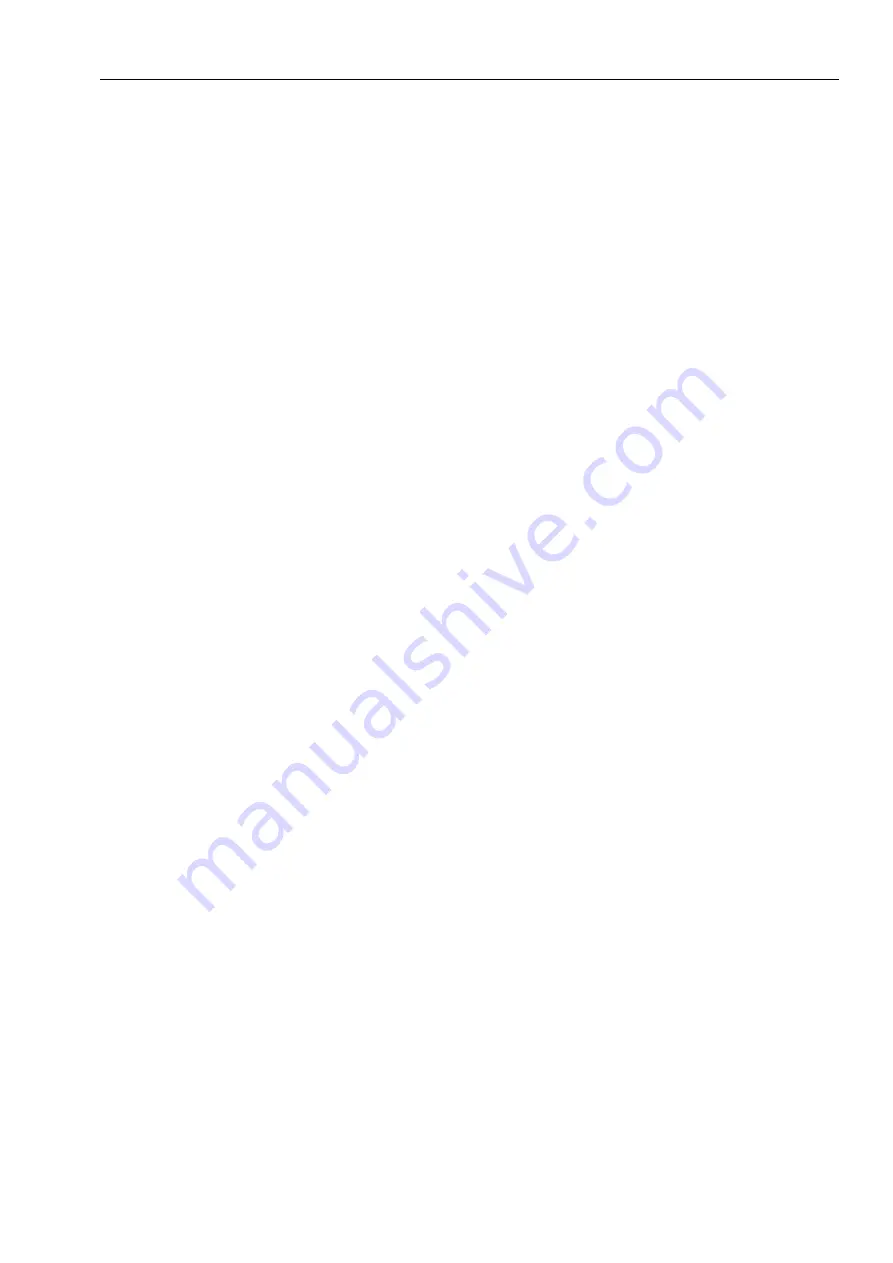
Faults and warnings
105
9.3
Other faults and messages
9.3.1
Automatic feeder
9.3.1.1
Starting program
The message
Smart Vxx.xx starting program
appears when the control program of the auto-
matic feeder starts.
Wait until the automatic feeder is ready to operate.
9.3.1.2
Initialization of the feeder
The message
first startup Press enter to start installation
will appear in the display in the
following cases:
•
When the automatic feeder starts for the first time.
•
If the processor card must be replaced due to a hardware defect.
Follow the instructions on the screen. The following steps can be performed in the course of the
initialization:
•
Restoration of the last backup (if available).
•
Entry of the language for the user interface.
•
Entry of the current date and time.
9.3.2
Hand terminal
9.3.2.1
CAN bus off
If a short circuit or electromagnetic discharges negatively affect the CAN cable, the message
terminal Vxx.xx CAN bus off
will appear in the display.
You can correct the fault as follows:
Check the CAN bus for short circuits and other faults and correct them.
9.3.2.2
CAN bus heavy
The following faults trigger the message
terminal Vxx.xx CAN bus heavy
:
•
Short circuit.
•
Terminating resistor not set.
•
Break in the data line.
•
CAN cable incorrectly attached.
•
No connection for automatic feeder control unit.
You can correct the fault as follows:
•
Check the CAN bus for short circuits.
•
Check that the terminating resistor has been properly set.
•
Check whether the data line has been interrupted.
•
Check that the CAN cables are correctly connected.
•
Check that the data line is correctly wired and that the feeder control is working.