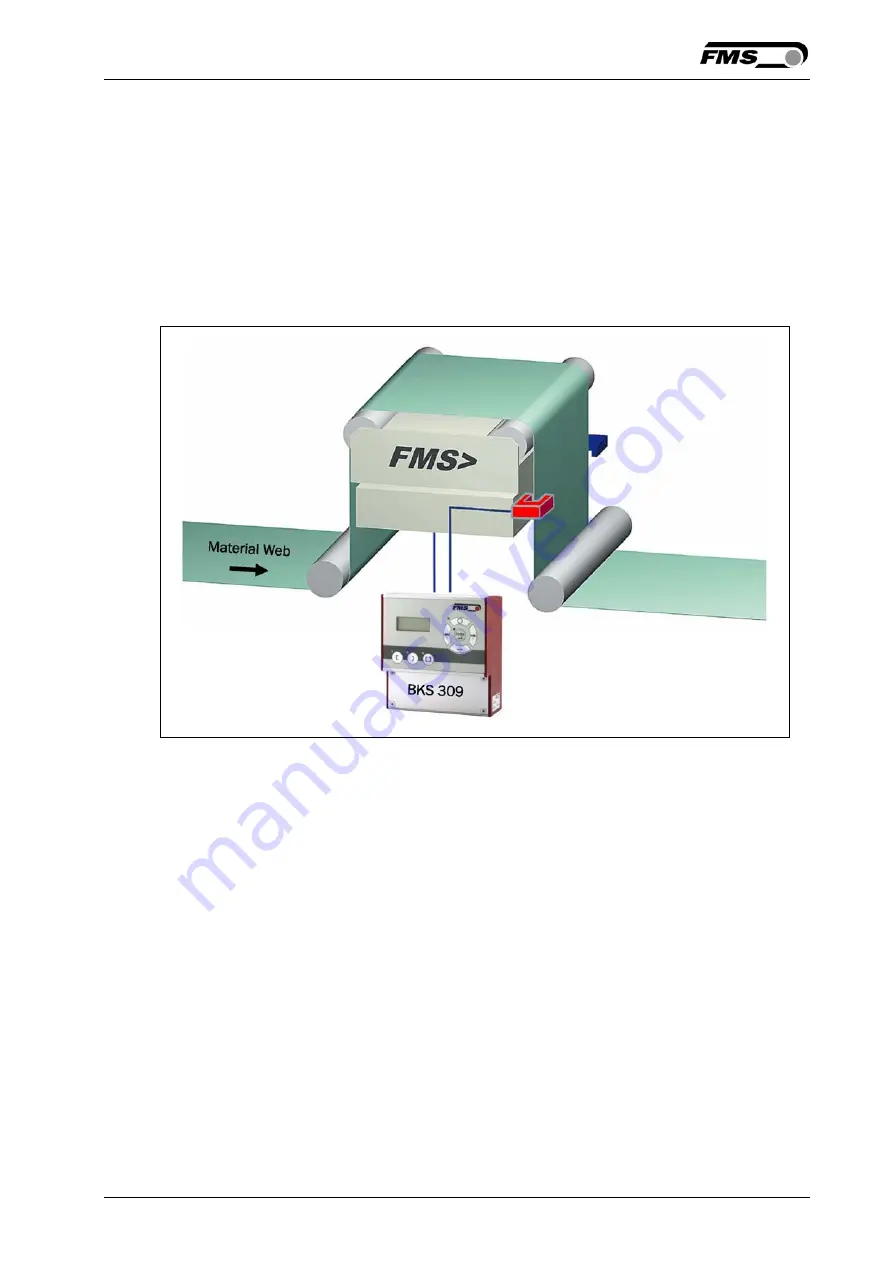
Operating Manual BKS309.MS
14.08.2018
5
2
System Description
2.1
Functional Description Standard Web Guide Controller
Figure 1 shows a typical web guiding system with its basic components.
The sensors measure the position of the web edge and send this information as an
analogue signal to the web guide controller BKS309. This electronics compares the
position feedback signal with the reference. If the difference of these two values is
higher then the stored dead band value, the steering frame will be adjusted.
Fig. 1: Basic system arrangement with BKS309 web guide controller
K309003e
2.2
Web Guide Controller with Master-Slave Functionality
For the lamination of two webs Chase & Follow Control Systems are often used. This
control system enables the exact positioning of two webs one above the other. The
BKS309.MS web guide controller with Master-Slave functionality measures the
position of a first web (Master) and guide a second web (Slave) so that both webs
exactly match each other. Chase & Follow guiding requires at least one steering
frame (or actuator) and two material sensors.
The material sensors are mounted on the same side of the corresponding webs.
Either both on the left, or both on the right hand side.