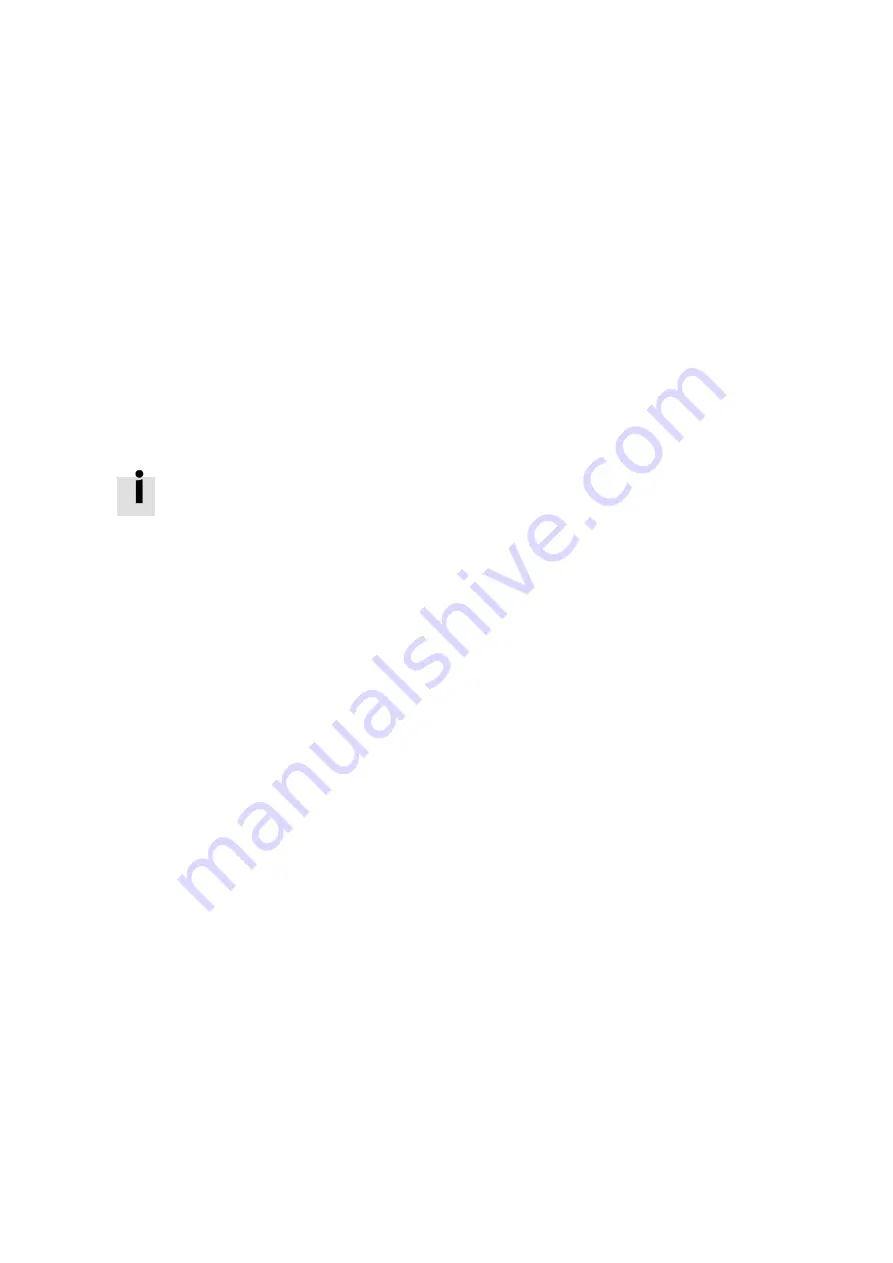
4. Commissioning
4-15
Festo P.BE-SPC11-SYS-ASI-EN en 0203NH
4.3.1 Preparations for the teach procedure
Teach procedure
During the teach procedure movement is made at first cycli-
cally and slowly to the end positions. In this way the SPC11
learns the mechanical end positions and some characteristic
system values such as friction and hysteresis. The SPC11
saves these values in the integrated EEPROM.
In order to check the set parameters for plausibility, the
moveable mass is first brought dynamically into the centre of
the positioning stroke used and then moved to just in front of
end position P.01. The teach procedure is concluded when
the moveable mass is pressed against end position P.01 and
the output bit O1 (D0) supplies a 1-signal.
Before commissioning can be undertaken, the pneumatic
drive must be ready for operation. The teach procedure
should be carried out with maximum permitted mass load.
During the teach procedure there must be a 0-signal at inputs
P.01 to P.04.
Proceed as follows in order to prepare the teach procedure:
1. Check the complete system structure, especially the drive
tubing (see chapter 3). Special specifications for your
drive can be found in the “Drive-specific supplement.”
2. Check the electrical circuitry.
3. If fixed stops are used, set the fixed stops accurately in
the desired end positions. The positioning stroke per-
mitted for the drive used can be found in the “Drive-
specific supplement.”
4. Check whether the parameters (amplification stage,
cushioning stage and system parameter) have already
been set correctly during pre-commissioning in accord-
ance with the components used and the mass load to be
moved.
Summary of Contents for Soft Stop SPC11 Series
Page 2: ......
Page 14: ...Contents and general instructions XII Festo P BE SPC11 SYS ASI EN en 0203NH ...
Page 15: ...Summary of components 1 1 Festo P BE SPC11 SYS ASI EN en 0203NH Chapter 1 ...
Page 25: ...Fitting 2 1 Festo P BE SPC11 SYS ASI EN en 0203NH Chapter 2 ...
Page 28: ...2 Fitting 2 4 Festo P BE SPC11 SYS ASI EN en 0203NH ...
Page 29: ...Installation 3 1 Festo P BE SPC11 SYS ASI EN en 0203NH Chapter 3 ...
Page 61: ...Commissioning 4 1 Festo P BE SPC11 SYS ASI EN en 0203NH Chapter 4 ...
Page 100: ...4 Commissioning 4 40 Festo P BE SPC11 SYS ASI EN en 0203NH ...
Page 101: ...Diagnosis and error treatment 5 1 Festo P BE SPC11 SYS ASI EN en 0203NH Chapter 5 ...
Page 114: ...5 Diagnosis and error treatment 5 14 Festo P BE SPC11 SYS ASI EN en 0203NH ...
Page 127: ...Technical appendix B 1 Festo P BE SPC11 SYS ASI EN en 0203NH Appendix B ...