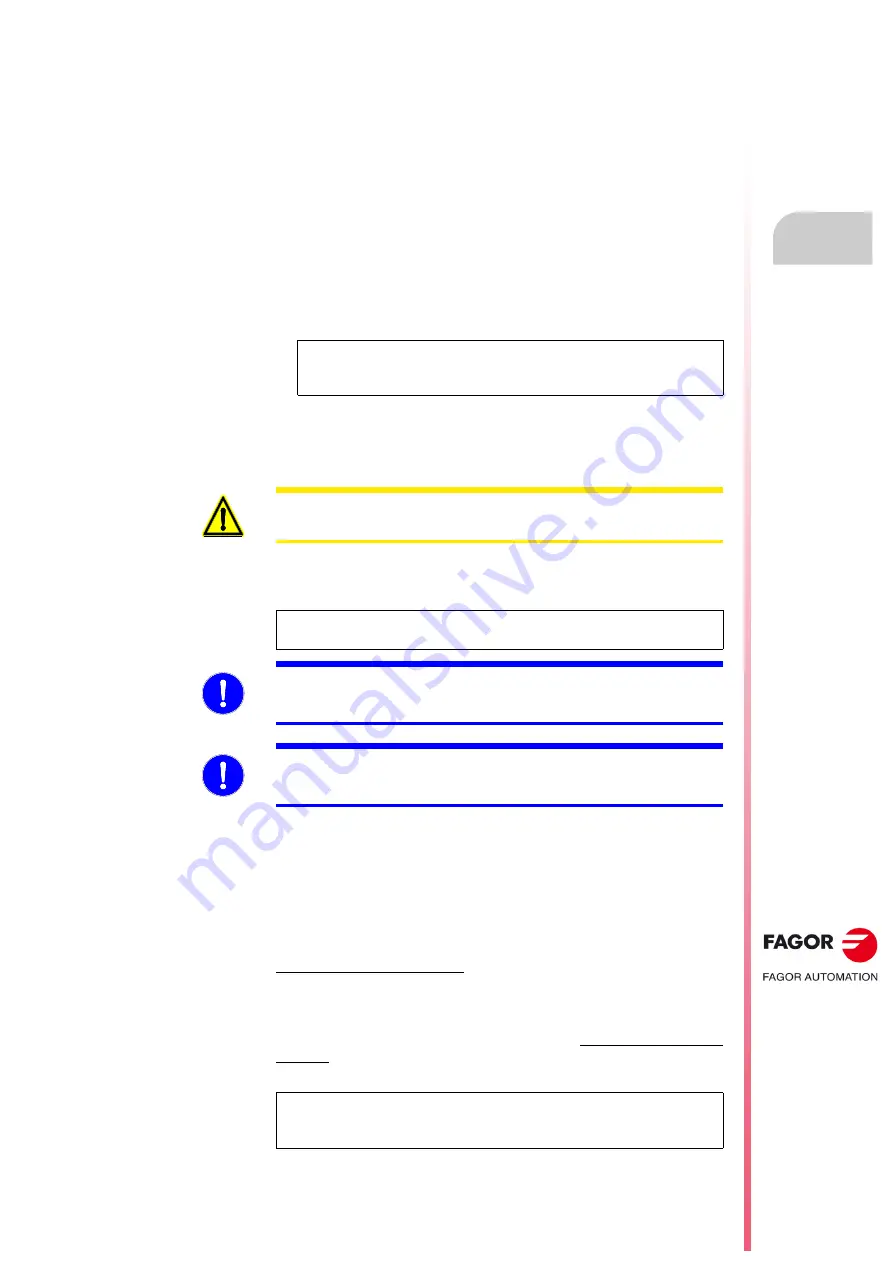
Connection diagrams
10.
Ref.1912
· 337 ·
DDS
HARDWARE
Even when having activated the Ballast circuit, if there is a problem with
it (e.g. poor connection of the external resistor) the bus voltage would
keep rising until reaching its maximum value allowed (790 V DC) and
would issue error
E215
for bus over-voltage. It would deactivate the
“Drive Enable” function and the motor would stop by friction without
motor torque.
Opening of power contactor - KM1
because the contact KA1
associated with the relay - KA1 has opened. The braking operation
would be the same as in the previous case when using a PS-65A or a
PS-25B4 power supply. If it is a regenerative power supply (XPS or RPS)
it brakes with emergency ramps if they have been previously set by
parameters. The excess energy generated by braking is returned to
mains just a few seconds before opening contactor - KM1 thanks to the
delayed deactivation of the relay - KA3. If for any reason the power bus
voltage kept rising, the braking operation would be the same as that of
the previous case.
Holding brake control
In some applications (e.g. the vertical Z axis on a milling machine) a
electromechanical holding brake is used on the rotor of the motor.
Hence, the brake holds the rotor when loses voltage at its terminals. When
the machine is out of service, the brake locks up the vertical Z axis to keep
it from falling due to gravity.
Remember that
The control circuits of compact drives as well as RPS, XPS and PS-25B4
power supplies are powered at 24 V DC by an internal auxiliary power
supply. PS-65A power supplies will need an external APS-24 auxiliary
power supply to power them because they do not have one integrated into
them.
For both ACD/SCD/CMC compact drives and PS/XPS main power supplies,
for 400/460 V AC line voltages, power the auxiliary power supply using a
two-phase 400/460 V AC line voltage. This is not the case for RPS main
power supplies where the auxiliary power supply must be supplied using a
three-phase 400/460 V AC line voltage.
For ACD/SCD/CMC compact drives designed for 200/240 V AC line
voltages (see "-L" in the commercial reference), power your integrated
auxiliary power supply using two-phase 200/240 V AC line voltages.
NOTE.
Remember that RPS power supplies do not have a Ballast
circuit and if the application requires one, an off-the-shelf circuit will
have to be used.
WARNING.
This brake must never be used to brake moving axes. It must
only be used to hold or lock vertical axes that have been stopped previously!
NOTE.
The reaction time of a brake integrated into an axis feeding FAGOR
motor may vary between 7 ms and 97 ms depending on the model.
MANDATORY.
While the brake is locking the vertical axis motor, the motor
must be kept with torque. See parameter GP9 in chapter 13 of the
“man_dds_soft.pdf” manual.
MANDATORY.
When powering the machine up, the brake must never be
released until the system assumes control of that axis. See the TV100 variable
in chapter 13 of the “man_dds_soft.pdf” manual.
NOTE.
FAGOR does not provide exterior main or auxiliary 200/240 V AC
power supplies. All these are designed to be supplied with line voltages
of between 400 (1-10%) V AC and 460 (1+10%) V AC.
Summary of Contents for DDS APS-24
Page 1: ...DRIVE DDS Hardware manual Ref 1912...
Page 6: ...6 Ref 1912 DDS HARDWARE 6 I This page intentionally left blank...
Page 9: ......
Page 10: ......
Page 11: ......
Page 12: ......
Page 16: ...Ref 1912 DDS HARDWARE 16...
Page 20: ...Ref 1912 DDS HARDWARE 20...
Page 179: ...3 Drives Ref 1912 179 DDS HARDWARE...
Page 180: ...3 Drives Ref 1912 DDS HARDWARE 180...
Page 200: ...4 AUXILIARY MODULES Auxiliary modules Ref 1912 DDS HARDWARE 200...
Page 260: ...7 Cables Ref 1912 DDS HARDWARE 260...
Page 397: ...Sales models 12 Ref 1912 397 DDS HARDWARE 12 9 Order example F H12 21 Order example...
Page 404: ...13 Compatibility Ref 1912 DDS HARDWARE 404...
Page 405: ......