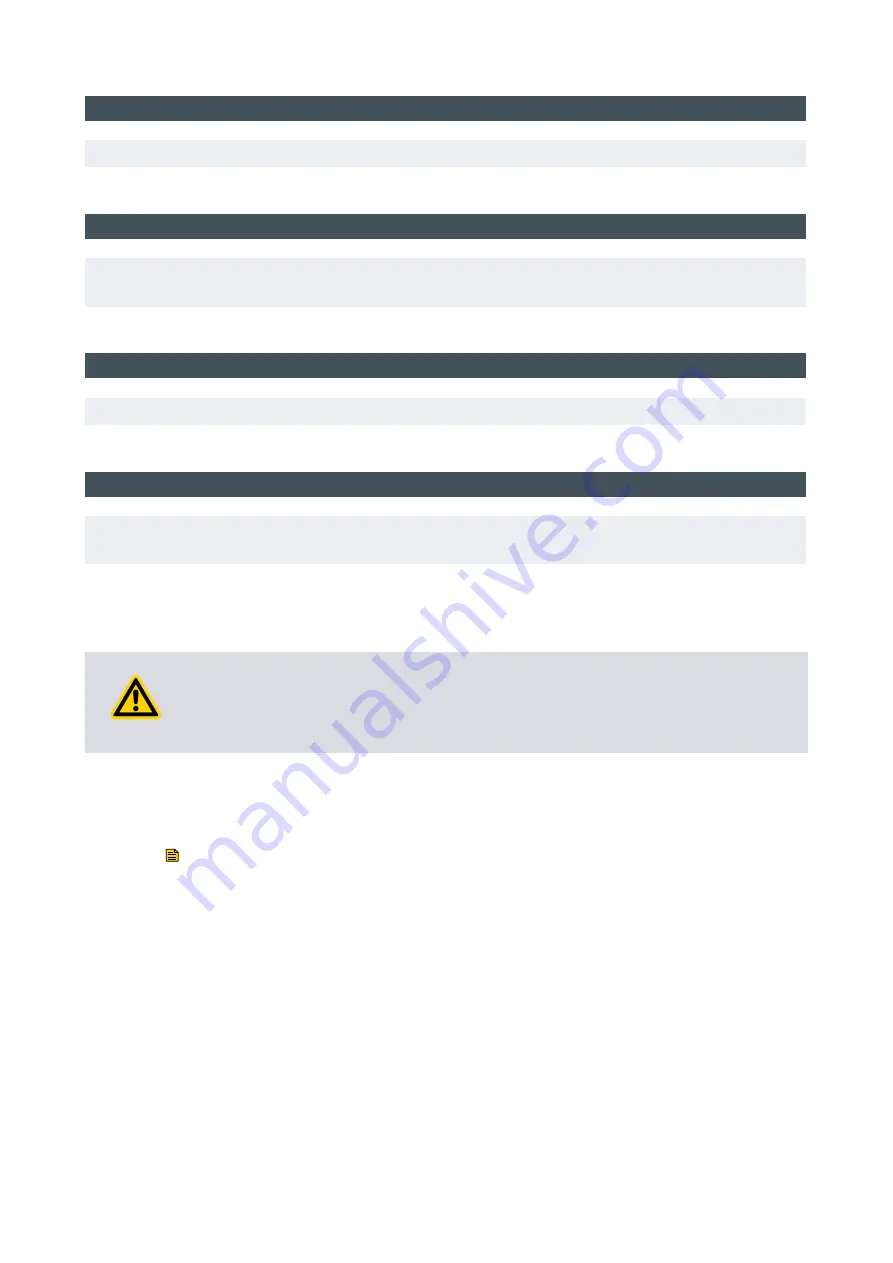
Fault
Alarm 184.10 - DP Low Speed
Cause
The dry pump speed is very low. The rotor is possibly locked.
Remedy
Cycle the power to the pump and attempt to restart. If this fails, contact us.
Fault
Alarm 186.01 - DP INV zzzzzzzzzzzzz
Cause
DP Inverter gives alarm code xxxx yyyy / Diagnostic registers aaaa bbbb. ffff is the
inverter fault count.
Remedy
Refer to
on page 83 for more information.
Fault
Alarm 186.01 - DP Not Running
Cause
Dry Pump Inverter will not start up when requested.
Remedy
Examine inverter fault history.
Fault
Alarm 186.13 - No DP Inv Comms
Cause
The pump controller cannot communicate with the dry pump inverter during
start up checks.
Remedy
Examine the wiring between the pump controller and the dry pump inverter.
8.2.3 Alarm conditions
CAUTION: LOSS OF WARRANTY
If 'Run 'til crash' is selected, the pump(s) can get damaged and all the warranties are
invalidated on the system equipment.
Normally, if an alarm condition exists, the control system will shut down the system.
For pumping systems which has a dry pump and booster combination, some alarms will
cause only the booster to stop and not the full system.
Note:
If required 'Run 'til crash' operation can be requested. In this mode of operation most
alarm conditions will be ignored and the pump(s) will continue to operate. For safety
reasons, some alarms cannot be overridden and the system will automatically shut down
even if 'Run 'til crash' has been selected. Refer to
'Run 'til crash' is automatically reset to 'off ' when the electrical supply is removed.
The Tool Interface overrides the 'Run 'til crash' state selected if it has control of the
pump.
10/2020 - ©Edwards Limited
Page 79
M56635880_D
M56635880_D - Fault finding
Summary of Contents for iXM Series
Page 1: ...Dry Pump System iXM INSTRUCTION MANUAL M56635880_D Original instructions edwardsvacuum com...
Page 101: ...This page has been intentionally left blank...
Page 102: ...This page has been intentionally left blank...
Page 103: ...This page has been intentionally left blank...
Page 104: ...edwardsvacuum com...