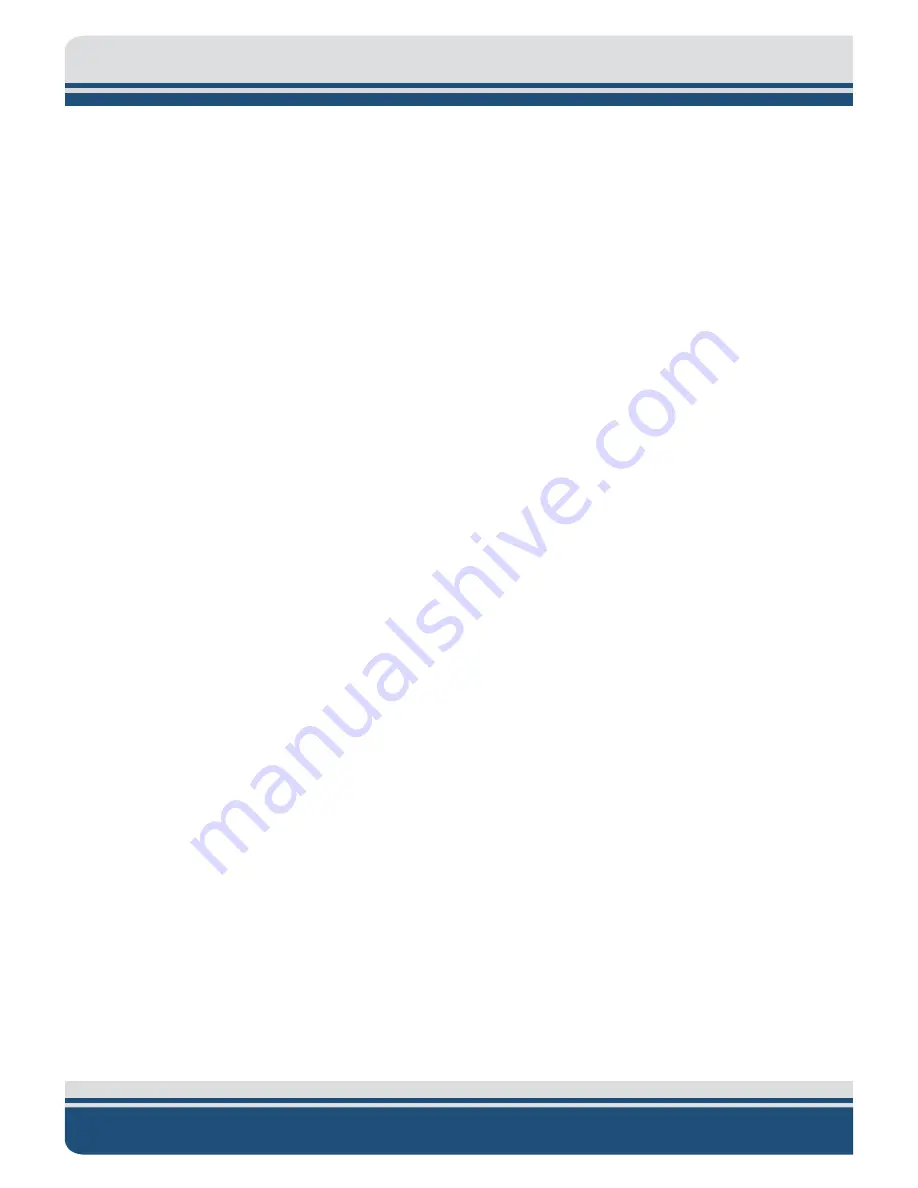
6.0: TROUBLESHOOTING
6-6
2000-DSS COMBINED SONAR
0009335_REV_D
occurred between the topside DISCOVER software, and tow vehicle. Self-Test FAIL tones repeat
indefinitely.
There will also be a video acknowledgement of successful self-test and linkup in the topside processor's
DISCOVER display window. Self-test status will also be displayed on an external video monitor if attached
directly to the tow vehicle’s CPU board's VGA connector.
If the topside processor is unavailable and the tow vehicle is dismantled, an external keyboard, mouse
and video monitor may be connected to the tow vehicle’s CPU board to provide some diagnostic testing.
An external power unit will still be required.
6.3.4
Topside Power Unit
Tow vehicle power is supplied either from an individual power/modem unit or from an integrated topside
processor. Voltage and current to the tow vehicle are important parameters. They must be within
acceptable limits for the tow vehicle to work properly. Check the tow cable output voltage with the system
connected and, if possible, the current drain with an inline connection. Cable current should be between
120mA (Idle) and 250mA.
The topside units supply 400VDC to the tow cable. The voltage at the tow vehicle end of the cable must
be not less than 300VDC to start the system and not be less than 200V during operation.
6.3.5
Command and Data Link
To check that the command and data link over the tow cable is operational, start the Remote Desktop
application on the topside control computer. There is normally a shortcut on the EdgeTech Desktop for
this. The tow vehicle's PC screen should appear in a window on the Topside Processor screen. This will
appear as a yellow desktop with the sonar application dialog box visible. If this is successful then the
command link is working.
6.3.6
Data Link
A good, quick qualitative test of the data link and tow vehicle electronics is to perform a rub test on each
transducer. Set the Range to 200 meters for both frequencies and start the system running in HDM mode
for both. Set screen gain to +30dB for both frequencies and briskly rub each aft transducer face one at a
time. A dark band should appear on the sonar processor screen corresponding to the side rubbed.
Data throughput rates on the uplink (vehicle to topside) can be critical in getting smooth data from the
tow vehicle. The data throughput rate can be checked using EdgeTech supplied utilities at each end of the
link
The sockBlast application is used to test network throughput between the tow vehicle and the Topside
Processor. This application is normally kept in C:\EdgeTech\Utilities folder on the topside unit, and
D:\EdgeTech\Utilities folder on the tow vehicle.
Summary of Contents for 2000-DSS
Page 20: ......
Page 56: ...Figure 4 2 2000 Digital Telemetry Link Electronics Block Diagram...
Page 57: ...Figure 4 3 2000 Digital Telemetry Link Wiring Diagram...
Page 59: ...Figure 4 4 Tow Vehicle Electronic Block Diagram...
Page 60: ...Figure 4 5 Tow Vehicle Interconnect Drawing...
Page 63: ...Figure 4 6 Armored Cable PMI Grip Unterminated Topside...
Page 64: ...Figure 4 7 Test Cable...
Page 77: ...5 13 Figure 5 16 Magnetic Declination Estimated Value Screen...
Page 79: ...5 15 getDeclination CR Figure 5 18...
Page 80: ......
Page 94: ......
Page 96: ......
Page 98: ......