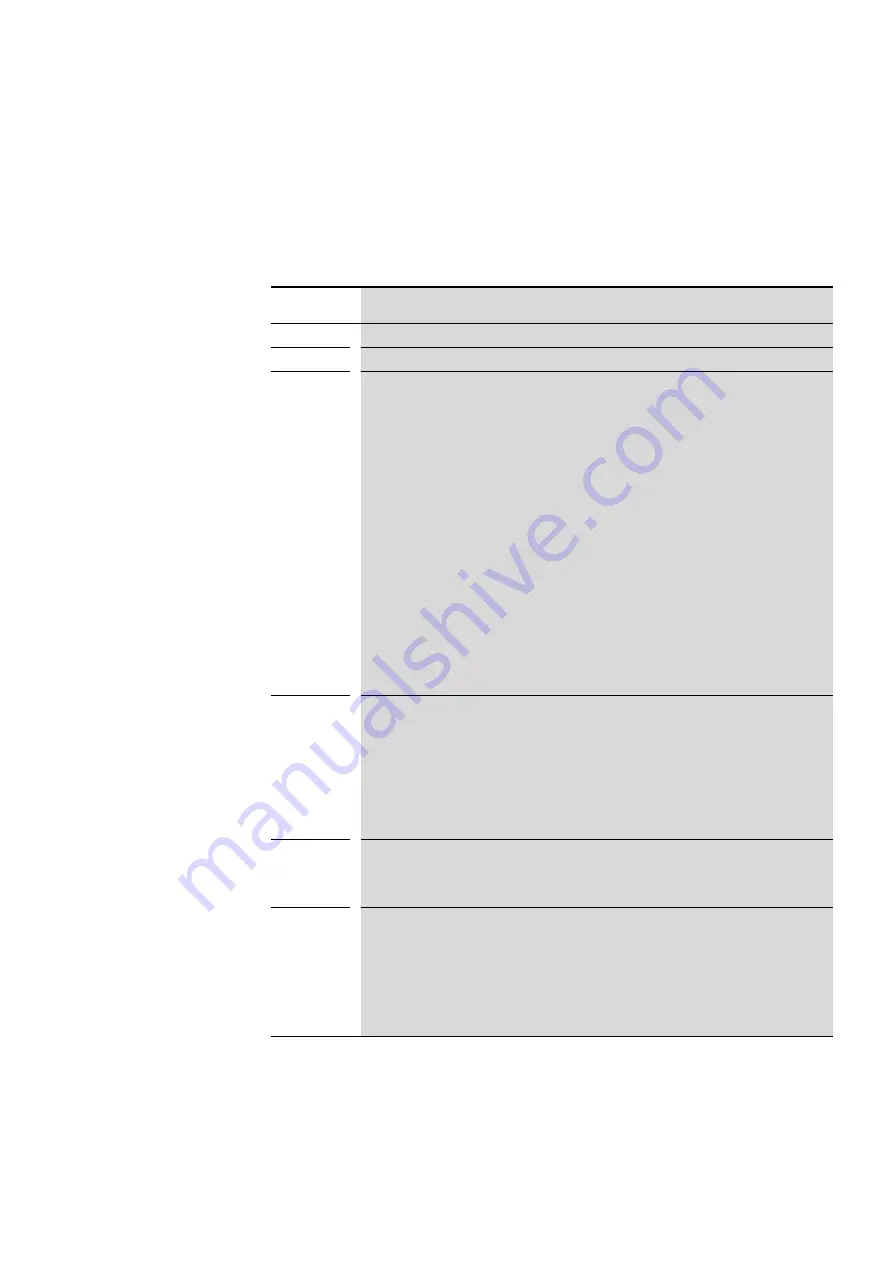
6 Parameter structure
6.5 Messages
DC1-S…20…, DC1-S…OE1 Variable Frequency Drives
05/21 MN040058EN
www.eaton.com
139
6.5 Messages
6.5.1 List of messages
Table 45: Messages
Message
Possible causes and fixes
STOP
Ready to start. There is no drive enable signal present. There are no fault messages present.
P-dEf
The parameters’ default settings have been loaded.
O-I
Overcurrent at variable frequency drive output
Occurs right after switching on the unit:
• Check the cable connection between the variable frequency drive and the motor
• Check the motor for shorted turns and ground faults
Occurs when starting the motor:
• Check whether the motor can rotate freely and make sure that it is not being blocked
mechanically.
• Motor with mechanical brake: Check whether the brake is being applied.
• Check the connection configuration (star/delta)
• Check to make sure that the correct rated motor current has been entered in P-08
• Increase the acceleration ramp time (t-acc, P-03) if necessary.
• Reduce the voltage boost with P-11.
Occurs during operation at a constant speed:
• Check whether the motor is overloaded.
Occurs during acceleration/deceleration:
• The ramp times are too short and require too much power.
If P-03 / P-04 cannot be increased, a larger device may be required.
I.t-trP
Motor overload. The thermal protection mechanism has tripped as a result of the device being
run above the rated motor current set with P-08 longer than a specific time.
• Check to make sure that the rated motor current has been entered in P-08.
• Check the motor’s connection configuration (e.g., start/delta)
• If the decimal points on the display flash during operation, this means that the unit is being
run in its overload range (> P-08). In this case, use P-03 to make the acceleration ramp longer
or reduce the load.
• Check whether the motor is being blocked mechanically or whether there are any additional
loads.
OI-b
Excessively high braking current
• Check the brake resistor and its wiring for short-circuits and ground faults.
• Make sure that the braking resistance value is not lower than the minimum permissible
braking resistance.
OL-br
Thermal overload on brake resistor. The drive has been switched off in order to prevent the brake
resistor from being thermally destroyed. This message will only be output if P-34 = 1 (“braking
chopper”)
• Make the P-04 and P-24 ramp times longer in order to have less frequent braking.
• Reduce the load’s inertia (if possible).
If the protection achieved with P-34 = 1 is not adequate for the brake resistor being used:
• Provide external protection for the brake resistor and set P-34 to a value of 2.
Summary of Contents for DC1-S1011NB-A20CE1 1
Page 4: ......