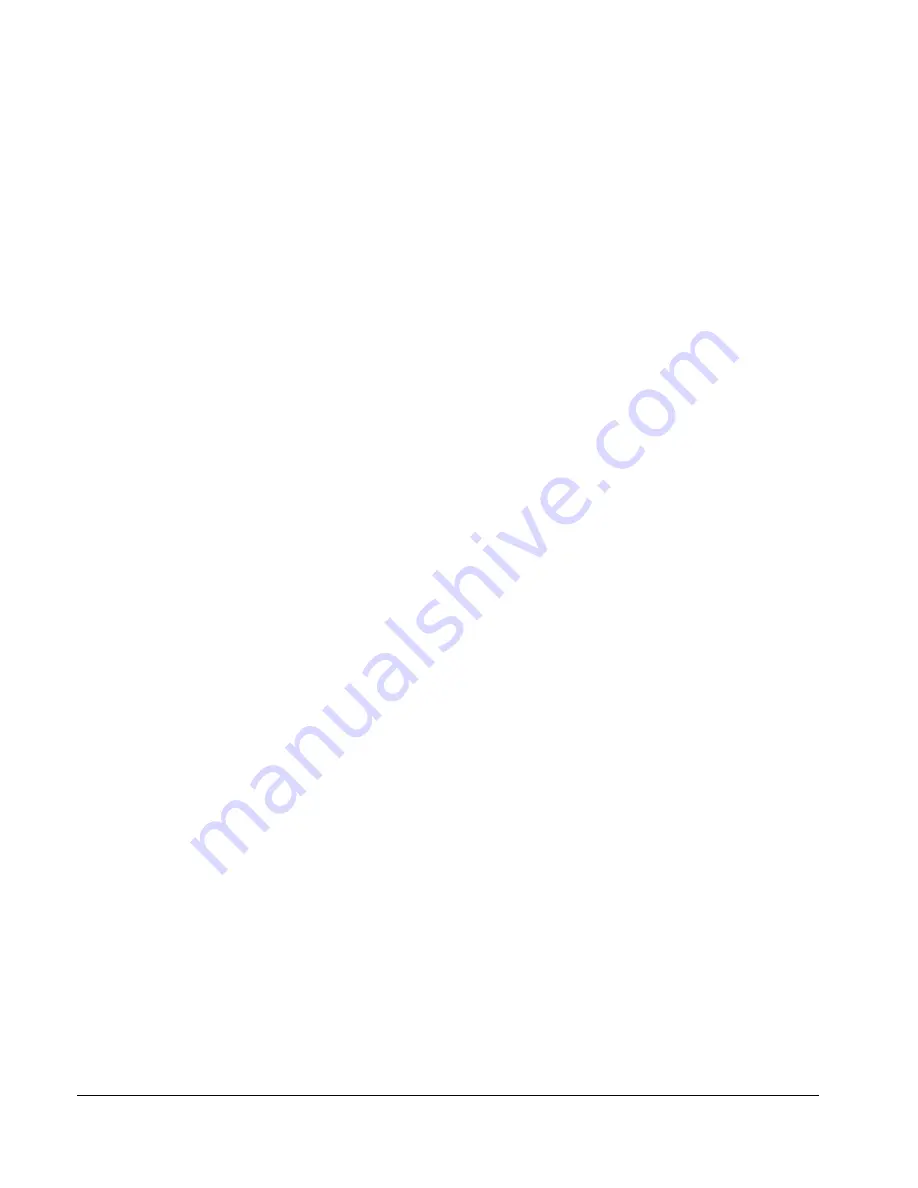
. .
Dyadic Systems – Mechatronics Cylinder Manual
MF
-005500-EN-8/63
1.1.2. This section is to introduce some product features and notes in detail:
(1) SCN-5 All-In-One Actuator: The Mechatronics Cylinder model SCN5 is a fully integrated actuator
including linear actuation mechanism, motor, servo drive and controller. Therefore after connecting
the power supply and some signal wiring, the SCN5 is ready for operation.
Other models (SCN6, SCLL, some SCLT models) have external controllers but the programming
software and ease of use are the same and the controllers are included in the part number.
(2) All actuators can be set such that the home position is at either end. The default home position is the
return (motor) end. The PC tool software allows the user to change homing parameters such as
speed and target thrust. The coordinate system is negative for the return home position and positive
for the forward home position.
(3) There is a close correlation between thrust and speed. If the necessary thrust is large, the max speed
is reduced. Please consult with the speed-thrust curve.
(4) Thrust capacity is the same for forward motion and return motion.
(5) The “Push Force” mode uses a high-speed, position-controlled approach move, followed by a lower
speed force controlled move. The speed of the force-controlled part of the move can be changed on
some Dyadic actuators. However, the max speed of the force controlled move will be limited by the
amount of current allowed for the target force (ie the actuator will not achieve full speed in this mode
if the target force is low). Also please keep in mind that high-speed impact to a hard target may
shorten the life of the actuator.
(6) In vertical use, the max load at power-up is lower. This value is published in the specs for each
actuator.
(7) There are 3 types of power saving functions (PC tool software is necessary to access these modes):
-1 Current setting at homing
-2 Current setting during positioning motion
-3 Current shut off after positioning
(8) Mechatronics Cylinder amplifiers have PNP models and NPN models. Please wire carefully following
the correct schematics.
(9) Mechatronics Cylinder outputs are open collector type. In case of driving a load like a coil, please
provide a surge absorber diode.
(10) The shafts of rod-type actuators are not designed for radial loading. Please provide external guides
and ensure proper alignment as poor alignment will transfer radial stress to the shaft nut and reduce
actuator life.
(11) Linear guides should be aligned within 0.1mm over the length of travel. Rough installation will
reduce the product life.
(12) The short cables protruding from the actuator motor are not flex-rated. If the application requires
cable motion, please use high flex cables (marked with “R” after the cable part number).
(13) Tightening torque for shaft-tip nuts is as follows: 30 kg-cm for SCN5, 45 kg-cm for SCN6
(14) Clean room actuators may be available depending on the requirement.
(15) Stroke limits for both directions can be set.
(16) The shaft tip screw is: M10, 1.25mm pitch for SCN5, M14, 1.5mm pitch for SCN6 models
(17) The front mounting block has a pilot diameter to make centering easily. (for SCN5 and SCN6)
(18) Shafts are anti-rotational. Please do not turn the shaft. (for SCN5 and SCN6)
(19) Multiple axis operation through serial communication is possible. DeviceNET, ccLink, and ASCII
interfaces can be used.
The operational PLC are; Mitsubishi, Keyence, OMRON as follows:
Mitsubishi PLC - MELSEC-A series (PC link unit)
AJ71UC24,
A1SJ71US24-R2/R4/PRF,
A1SJ71C24-R2/R4/PRF, A1SCPUC24-R2,
A2CCPUC24(PRF)
Mitsubishi PLC - MELSEC-F series (Communication board)
FX2N-232-BD, FX1N-232-BD, FX2NC-232-ADP
Notes: Sample programs can be provided in the project file of Mitsubishi GX Developer Version 7,
therefore the customer must have the program GX Developer Version 7 or newer.
Keyence PLC – KV-700 (Communication unit) KV-L20 attached
OMRON PLC – CS/CJ series (CPU unit)
CS1H-CPU*H, CS1G-CPU4*H, CS1H-CPU6*-V1, CS1G-CPU4*-V1, CJ1H-CPU6*H,