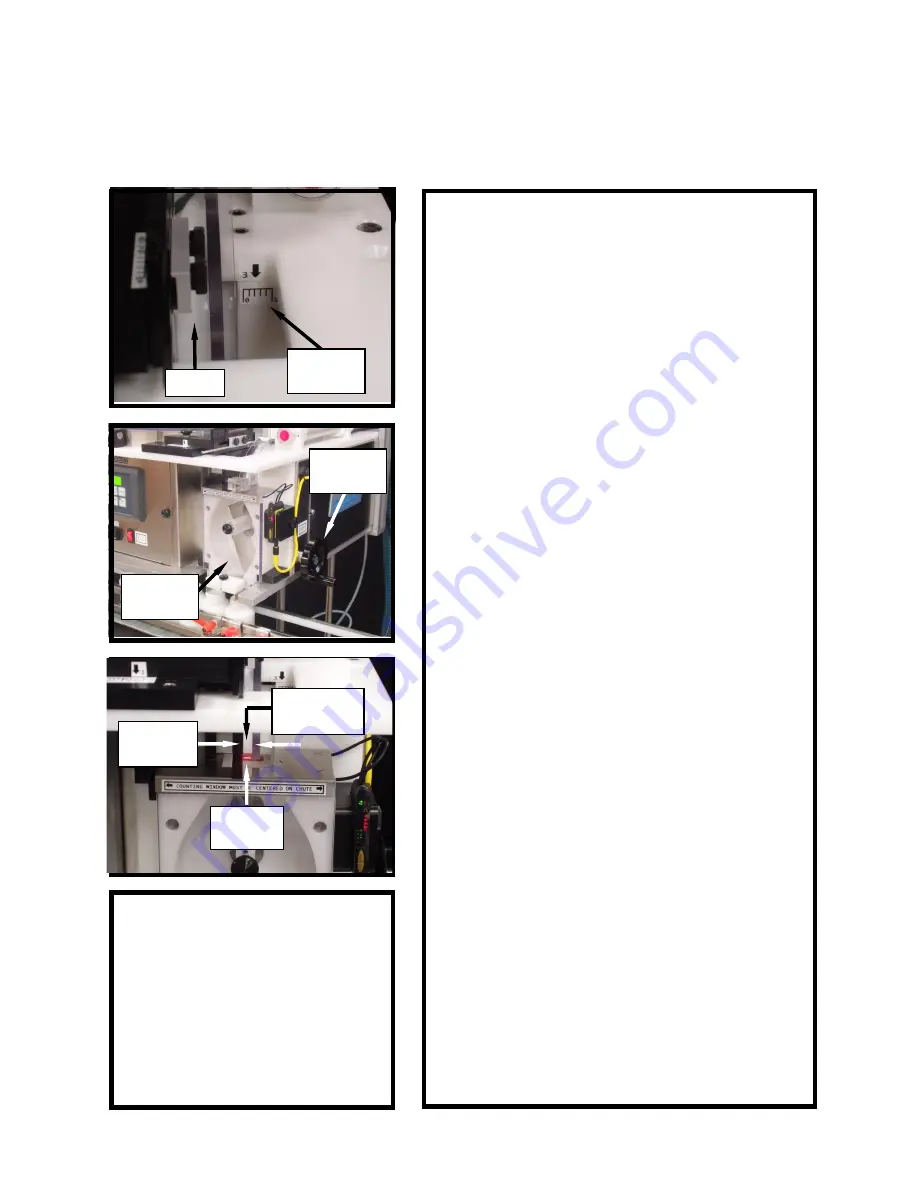
Rev 2022-03-08
Pharmafill Model TC3 User Manual
Deitz Company Inc.
TC3 User Manual
Page 31
8.1 - Product Guide Adjustments (Cont’d)
Adjustment 3 – CENTERING
To count properly, objects must fall directly from
the chute into the center of the counting head.
This way the object will fall through the center of
the light source of the counting window and strike
the divider flag at the same angle whether
diverting right or left.
The centering adjustment is needed because when
you make a change to the width of the Product
Guide, you are moving the left side of the chute.
As the width of the chute changes, so does the
location of the centerline.
Centering Adjustment
After changing the width of the Product Guides,
center the Counting Head by turning the
Centering Wheel on the right side of the machine.
Note the position of the Counting Head as
indicated on the Centering Scale. It should be
approximately the same number as on the Width
Scale
Visually confirm that the Counting Head is
centered on the chute by looking at the red light
source from directly in front of the chute. You
may remove the Clear Chute Cover for a better
view, or bend down to look up through the Clear
Front Cover of the Counting Head.
CENTERING
SCALE
CHUTE
CENTERING
WHEEL
CENTERLINE
OF CHUTE
LIGHT
SOURCE
WIDTH
OF CHUTE
COUNTING
HEAD
Summary of Contents for Pharmafill TC3
Page 1: ...Model TC3 Electronic Counter Operation Manual...
Page 44: ...Rev 2022 03 08 Pharmafill Model TC3 User Manual Deitz Company Inc TC3 User Manual Page 32...
Page 69: ......
Page 74: ......
Page 75: ......
Page 76: ......
Page 77: ......
Page 78: ......
Page 79: ......
Page 80: ......
Page 81: ......
Page 82: ......
Page 83: ......
Page 84: ......