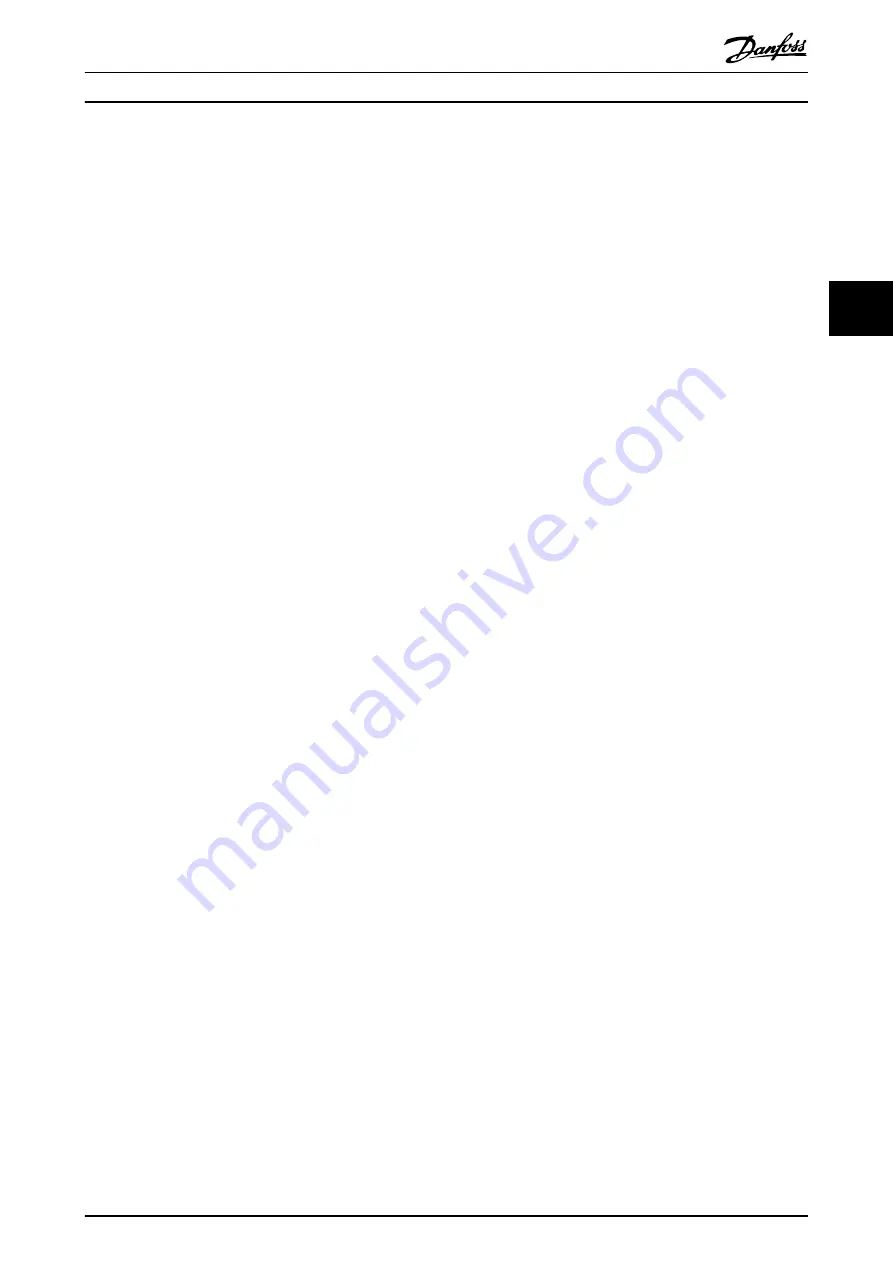
Troubleshooting
•
Check that the ambient operating temperature is
within the limits.
•
Check for clogged filters.
•
Check the fan operation.
•
Check the control card.
WARNING 66, Heat sink temperature low
The frequency converter is too cold to operate. This
warning is based on the temperature sensor in the IGBT
module.
Increase the ambient temperature of the unit. Also, a
trickle amount of current can be supplied to the frequency
converter whenever the motor is stopped by setting
parameter 2-00 DC Hold/Preheat Current
at 5% and
parameter 1-80 Function at Stop
.
ALARM 67, Option module configuration has changed
1 or more options have either been added or removed
since the last power-down. Check that the configuration
change is intentional and reset the unit.
ALARM 68, Safe Stop activated
STO has been activated. To resume normal operation,
apply 24 V DC to terminal 37, then send a reset signal (via
bus, digital I/O, or by pressing [Reset]).
ALARM 69, Power card temperature
The temperature sensor on the power card is either too
hot or too cold.
Troubleshooting
•
Check that the ambient operating temperature is
within limits.
•
Check for clogged filters.
•
Check fan operation.
•
Check the power card.
ALARM 70, Illegal FC configuration
The control card and power card are incompatible. To
check compatibility, contact the Danfoss supplier with the
type code of the unit from the nameplate and the part
numbers of the cards.
ALARM 71, PTC 1 safe stop
STO has been activated from the VLT
®
PTC Thermistor Card
MCB 112 (motor too warm). Normal operation can be
resumed when the MCB 112 applies 24 V DC to terminal
37 again (when the motor temperature reaches an
acceptable level) and when the digital input from the MCB
112 is deactivated. When that happens, send a reset signal
(via bus or digital I/O, or press [Reset]).
ALARM 72, Dangerous failure
STO with trip lock. An unexpected combination of STO
commands has occurred:
•
VLT
®
PTC Thermistor Card MCB 112 enables
X44/10, but STO is not enabled.
•
MCB 112 is the only device using STO (specified
through selection
[4] PTC 1 Alarm
or
[5] PTC 1
Warning
in
parameter 5-19 Terminal 37 Safe Stop
STO is activated, and X44/10 is not activated.
ALARM 80, Drive initialised to default value
Parameter settings are initialised to default settings after a
manual reset. To clear the alarm, reset the unit.
ALARM 92, No flow
A no-flow condition has been detected in the system.
Parameter 22-23 No-Flow Function
is set for alarm.
Troubleshooting
•
Troubleshoot the system and reset the frequency
converter after the fault has been cleared.
ALARM 93, Dry pump
A no-flow condition in the system with the frequency
converter operating at high speed may indicate a dry
pump.
Parameter 22-26 Dry Pump Function
is set for alarm.
Troubleshooting
•
Troubleshoot the system and reset the frequency
converter after the fault has been cleared.
ALARM 94, End of curve
The feedback is lower than the setpoint. This may indicate
leakage in the system.
is set for alarm.
Troubleshooting
•
Troubleshoot the system and reset the frequency
converter after the fault has been cleared.
ALARM 95, Broken belt
Torque is below the torque level set for no load, indicating
a broken belt.
Parameter 22-60 Broken Belt Function
is set
for alarm.
Troubleshooting
•
Troubleshoot the system and reset the frequency
converter after the fault has been cleared.
ALARM 96, Start delayed
Motor start has been delayed due to short-cycle
protection.
Parameter 22-76 Interval between Starts
is
enabled. Troubleshoot the system and reset the frequency
converter after the fault has been cleared.
WARNING 97, Stop delayed
Stopping the motor has been delayed due to short cycle
protection.
Parameter 22-76 Interval between Starts
is
enabled.
Troubleshooting
•
Troubleshoot the system and reset the frequency
converter after the fault has been cleared.
WARNING 98, Clock fault
Time is not set or the RTC clock has failed. Reset the clock
in
.
Troubleshooting
Programming Guide
MG11CE02
Danfoss A/S © 03/2015 All rights reserved.
221
4
4