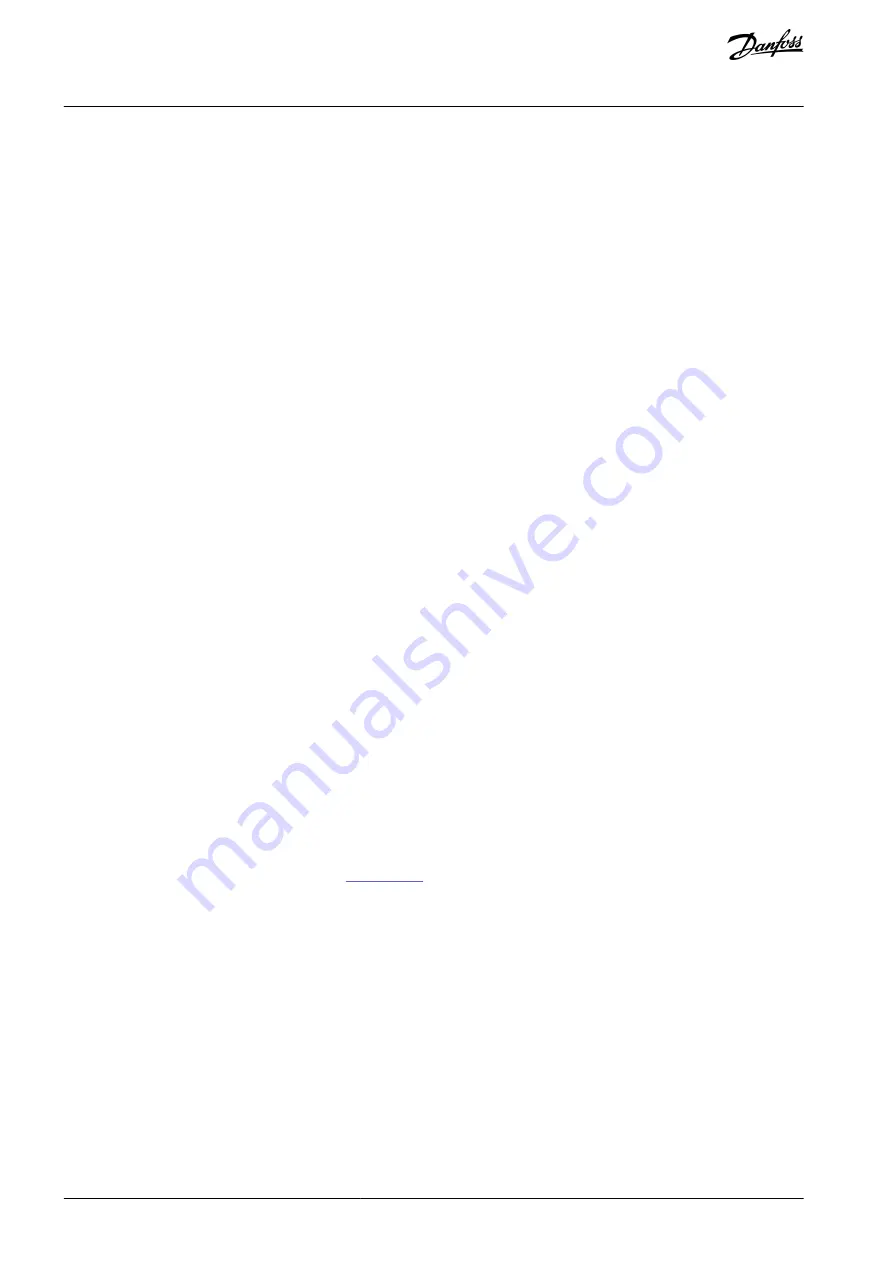
This feature eliminates the need for manual resetting and enhances automated operation for remotely controlled systems. The
number of restart attempts and the duration between attempts can be limited.
6.2.7 Flying Start
Flying start allows the drive to synchronize with an operating motor rotating at up to full speed in either direction. This prevents
trips due to overcurrent draw. It minimizes mechanical stress to the system since the motor receives no abrupt change in speed
when the drive starts.
6.2.8 Full Torque at Reduced Speed
The drive follows a variable V/Hz curve to provide full motor torque even at reduced speeds. Full output torque can coincide with
the maximum designed operating speed of the motor. This drive differs from variable torque drives and constant torque drives.
Variable torque drives provide reduced motor torque at low speed. Constant torque drives provide excess voltage, heat, and motor
noise at less than full speed.
6.2.9 Frequency Bypass
In some applications, the system can have operational speeds that create a mechanical resonance. This mechanical resonance can
generate excessive noise and possibly damage mechanical components in the system. The drive has 4 programmable bypass-fre-
quency bandwidths (
parameters 4-60
to
4-63
). The bandwidths allow the motor to step over speeds that induce system resonance.
6.2.10 Motor Preheat
To preheat a motor in a cold or damp environment, a small amount of DC current can be trickled continuously into the motor to
protect it from condensation and cold starts.
See
parameter 2-00 DC Hold Current in the programming guide
) for more detail.
The motor preheat function can eliminate the need for a space heater.
6.2.11 Programmable Set-ups
The drive has 4 set-ups that can be independently programmed. Using multi-setup, it is possible to switch between independently
programmed functions activated by digital inputs or a serial command. Independent set-ups are used, for example, to change refer-
ences, or for day/ night or summer/winter operation, or to control multiple motors. The LCP shows the active set-up.
Set-up data can be copied from drive to drive by downloading the information from the removable LCP, by using MCT 10, or by
using a smart device if a VLT® Wireless Control Panel LCP 103 is installed.
6.2.12 Smart Logic Controller
Smart logic control (SLC) is a sequence of user-defined actions (see
parameter 13-52 SL Controller Action
[x]) executed by the SLC
when the associated user-defined event (see
parameter 13-51 SL Controller Event
[x]) is evaluated as true by the SLC.
It is possible to create up to 4 independent sequences. Linking between sequences can be done by using logic rules. Use the SLC
settings to activate, deactivate, and reset the smart logic control sequence. The logic functions and comparators are always running
in the background, which opens for separate control of digital inputs and outputs. In MCT 10, it is possible to program the SLC
sequences via the graphics plug-in.
The condition for an event can be a particular status or that the output from a logic rule or a comparator operand becomes true.
That leads to an associated action as shown in the
AJ300847815559en-000101 / 130R0337
48 | Danfoss A/S © 2020.09
Product Features
VLT® AQUA Drive FC 202
Design Guide