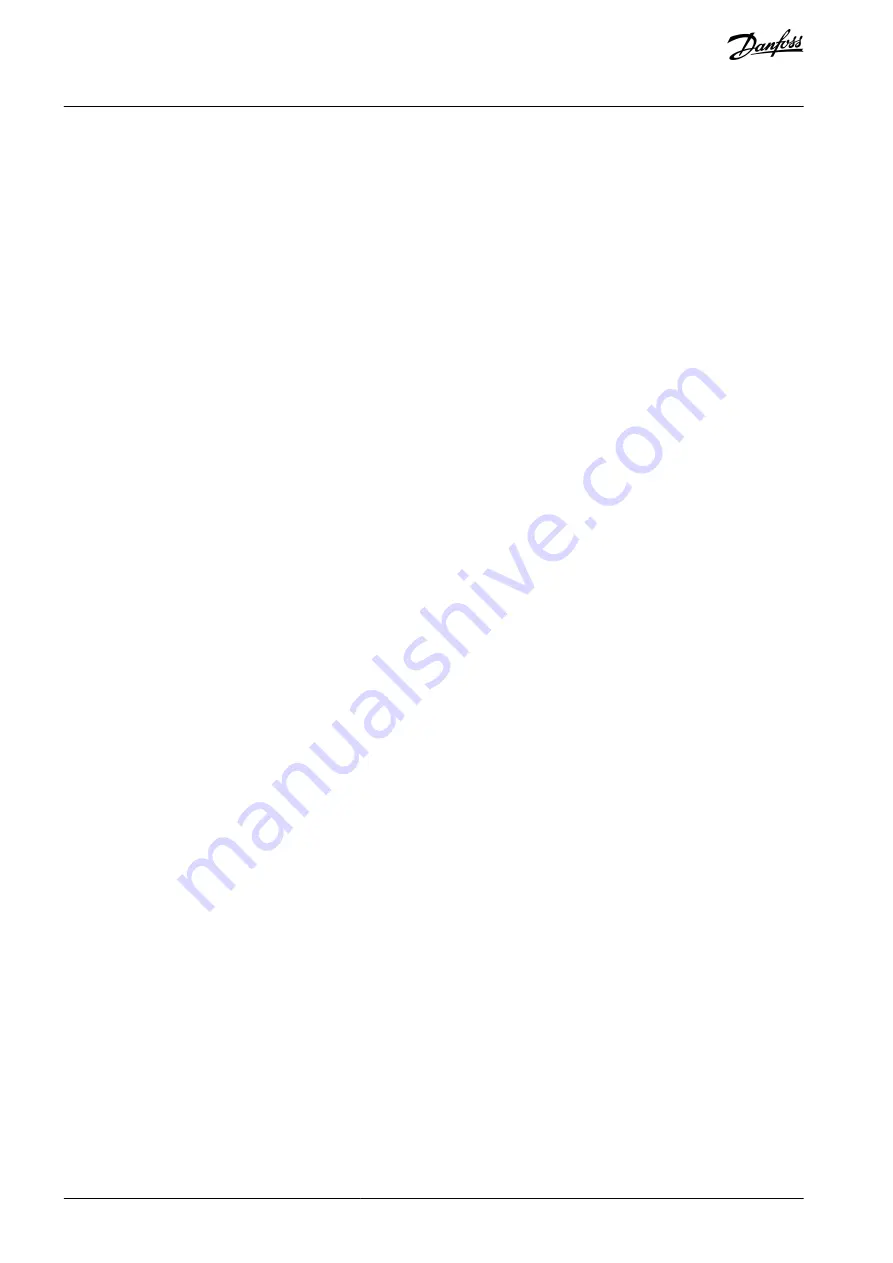
•
•
•
•
•
•
•
6.1.9.8 Current
Derate the output current at high temperatures. This calculation takes place after the calculations for derating the switching fre-
quency. The result is an attempt to lower the temperatures by first lowering the switching frequency, and then lowering the output
current. Current derating only takes place if the user has programmed the unit to derate in overtemperature situations. If the user
has selected a trip function for overtemperature situations, the current derate factor is not lowered.
6.1.10 Automatic Switching Frequency Modulation
The drive generates short electrical pulses to form an AC wave pattern. The switching frequency is the rate of these pulses. A low
switching frequency (slow pulsing rate) causes audible noise in the motor, making a higher switching frequency preferable. A high
switching frequency, however, generates heat in the drive that can limit the amount of current available to the motor.
Automatic switching frequency modulation regulates these conditions automatically to provide the highest switching frequency
without overheating the drive. By providing a regulated high switching frequency, it quiets motor operating noise at slow speeds,
when audible noise control is critical, and produces full output power to the motor when required.
6.1.11 Automatic Derating for High Switching Frequency
The drive is designed for continuous, full-load operation at switching frequencies between 1.5–2 kHz for 380–480 V, and 1–1.5 kHz
for 525–690 V. The frequency range depends on power size and voltage rating. A switching frequency exceeding the maximum
allowed range generates increased heat in the drive and requires the output current to be derated.
An automatic feature of the drive is load-dependent switching frequency control. This feature allows the motor to benefit from as
high a switching frequency as the load allows.
6.1.12 Power Fluctuation Performance
The drive withstands mains fluctuations such as:
Transients.
Momentary dropouts.
Short voltage drops.
Surges.
The drive automatically compensates for input voltages ±10% from the nominal to provide full rated motor voltage and torque.
With auto restart selected, the drive automatically powers up after a voltage trip. With flying start, the drive synchronizes to motor
rotation before start.
6.1.13 Resonance Damping
Resonance damping eliminates the high-frequency motor resonance noise. Automatic or manually selected frequency damping is
available.
6.1.14 Temperature-controlled Fans
Sensors in the drive regulate the operation of the internal cooling fans. Often, the cooling fans do not run during low load opera-
tion, or when in sleep mode or standby. These sensors reduce noise, increase efficiency, and extend the operating life of the fan.
6.1.15 EMC Compliance
Electromagnetic interference (EMI) and radio frequency interference (RFI) are disturbances that can affect an electrical circuit due to
electromagnetic induction or radiation from an external source. The drive is designed to comply with the EMC product standard for
drives IEC 61800-3 and the European standard EN 55011. Motor cables must be shielded and properly terminated to comply with
the emission levels in EN 55011. For more information regarding EMC performance, see the EMC Test Results section.
6.1.16 Galvanic Isolation of Control Terminals
All control terminals and output relay terminals are galvanically isolated from mains power, which completely protects the controller
circuitry from the input current. The output relay terminals require their own grounding. This isolation meets the stringent protec-
tive extra-low voltage (PELV) requirements for isolation.
The components that make up the galvanic isolation are:
Supply, including signal isolation.
Gate drive for the IGBTs, trigger transformers, and optocouplers.
The output current Hall effect transducers.
AJ300847815559en-000101 / 130R0337
44 | Danfoss A/S © 2020.09
Product Features
VLT® AQUA Drive FC 202
Design Guide