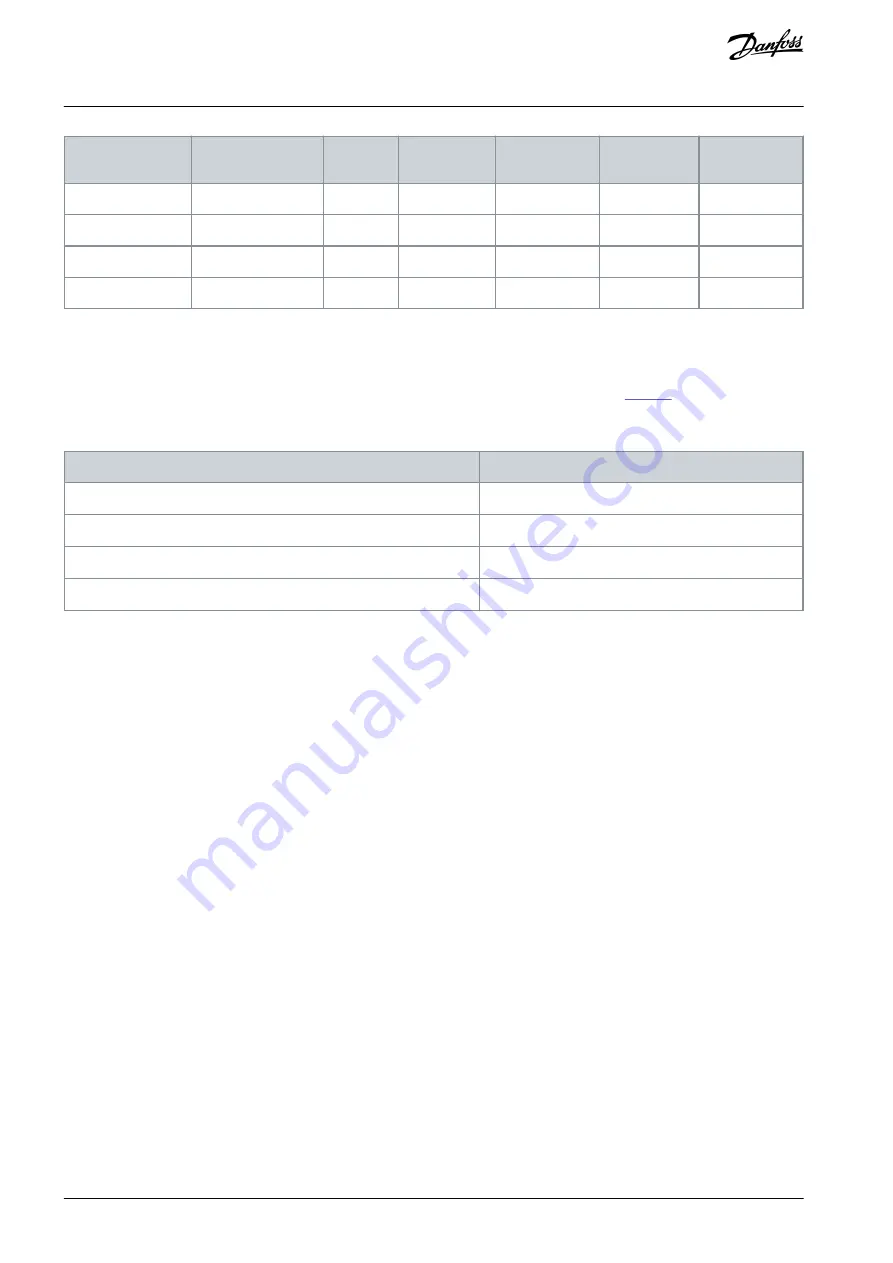
•
•
-
-
-
-
-
-
•
•
•
•
•
•
Enclosure sizes
Power size [kW (hp)] Voltage
[V]
1 cable [m
(ft)]
2 cables [m (ft)] 3 cables [m
(ft)]
4 cables [m (ft)]
500
150 (492)
75 (246)
50 (164)
37 (121.4)
A3
1.1–7.5 (1.5–10)
525–690
100 (382)
50 (164)
33 (108)
25 (82)
B4
11–30 (15–40)
525–690
150 (492)
75 (246)
50 (164)
37 (121.4)
C3
37–45 (50–60)
525–690
150 (492)
75 (246)
50 (164)
37 (121.4)
10.8.3 Motor Insulation
Modern motors for use with drives have a high degree of insulation to account for new generation high-efficiency IGBTs with high
dU/dt. For retrofit in old motors, confirm the motor insulation or mitigate with dU/dt filter or, if necessary, a sine-wave filter.
For motor cable lengths ≤ the maximum cable length listed in , the motor insulation ratings listed in
are recommended. If a
motor has lower insulation rating, use a dU/dt or sine-wave filter.
Table 86: Motor Insulation Ratings
Nominal mains voltage [V]
Motor insulation [V]
U
N
≤ 420
Standard U
LL
=1300
420 V < U
N
≤ 500
Reinforced U
LL
=1600
500 V < U
N
≤ 600
Reinforced U
LL
=1800
600 V < U
N
≤ 690
Reinforced U
LL
=2000
10.8.4 Motor Bearing Currents
To minimize DE (Drive End) bearing and shaft currents, ground the drive, motor, driven machine, and motor to the driven machine
properly. For more information, refer to the
Minimizing Bearing Failures in AC Drive Systems User Guide
.
Standard mitigation strategies
Use an insulated bearing.
Apply rigorous installation procedures:
Ensure that the motor and load motor are aligned.
Strictly follow the EMC Installation guideline.
Reinforce the PE so the high-frequency impedance is lower in the PE than the input power leads.
Provide a good high-frequency connection between the motor and the drive for instance by shielded cable which has a
360° connection in the motor and the drive.
Make sure that the impedance from the drive to the building ground is lower than the grounding impedance of the ma-
chine. This can be difficult for pumps.
Make a direct ground connection between the motor and load motor.
Lower the IGBT switching frequency.
Modify the inverter waveform, 60° AVM vs. SFAVM.
Install a shaft grounding system or use an isolating coupling.
Apply conductive lubrication.
Use minimum speed settings if possible.
Try to ensure that the line voltage is balanced to ground. This can be difficult for IT, TT, TN-CS, or Grounded leg systems.
10.9 Braking
10.9.1 Selection of Brake Resistor
To handle higher demands by regenerative braking, a brake resistor is necessary. Using a brake resistor ensures that the energy is
absorbed in the brake resistor and not in the drive. For more information, see the VLT® Brake Resistor MCE 101 Design Guide.
AJ300847815559en-000101 / 130R0337
138 | Danfoss A/S © 2020.09
Electrical Installation
Considerations
VLT® AQUA Drive FC 202
Design Guide