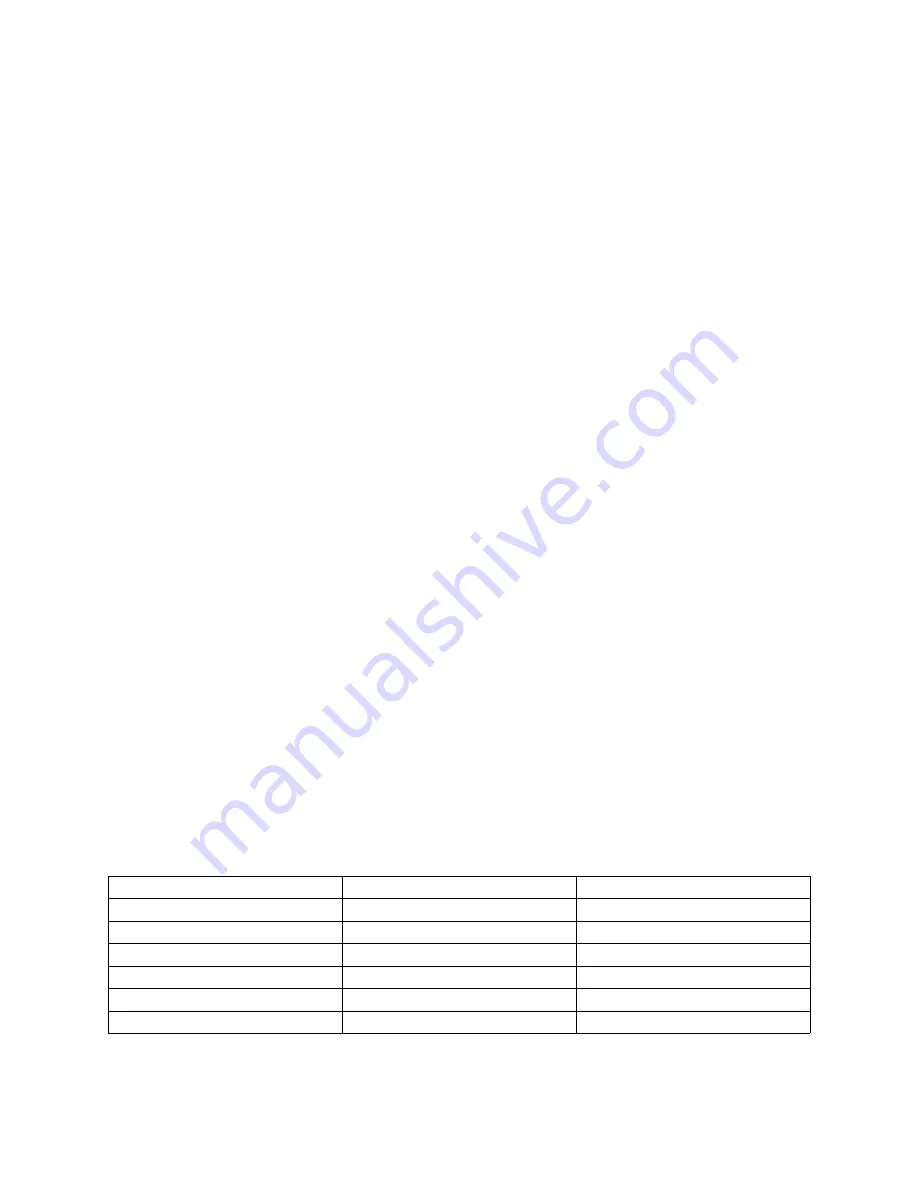
S0702170K
Page 21
Hydraulic System Troubleshooting, Testing and
Adjustment
FLOW METER AND FLOW METER KIT INSTALLATION
AND TESTING
Checking regulator and pump output, to assess the output balance between the front and rear pumps and
to verify operating adjustment of each regulator, will require installation of a flow meter.
The After Sales Service department of the nearest local Daewoo dealer can assist you with these tests or,
if you prefer carrying out your own testing, they should be able to help in putting together a hose and fitting
kit (or the required dimensions and specifications for hoses and fittings) to allow you to install a flow meter
downstream from the main pump assembly.
Installation and Testing Procedure
•
Turn off the engine and operate controls to release hydraulic pressure from the accumulator.
•
Vent the reservoir to release all pressure from the hydraulic system.
•
Remove guard panels from around the main pump assembly.
•
Disconnect the main pump discharge output line. Install the input flange of the flow meter on the
pump end of the output line.
•
Cap off the unused (input) end of the pump discharge line with a blocking flange.
•
Bolt up a pre-measured length of hydraulic hose, between the output end of the flow meter
assembly and the top of the reservoir. Use appropriate fittings and adapter flanges to guarantee
a pressure tight seal.
NOTE:
Be sure to maintain even tightening torque on all flange fittings. Use Loctite brand “PST
545” (or an alternate manufacturer’s hydraulic system joint seal) if required, to give an
airtight seal.
•
An assistant – who must remain at the operator’s control station at all times – should restart the
engine and run it long enough (at minimum RPM) to de-aerate the system and warm up the
engine and hydraulic system to operating temperature.
Record the values of all test results in three columns, comparing 1) pump pressure (from the instrument
panel display) with 2) measured flow, in gallons or liters per minute, from the installed flow
meter. The third column of test results should provide a record of engine RPM measured during each of
the following tests – with the engine speed control dial set at maximum, the power mode selector at Power
Mode and the work mode selector at digging mode:
•
Unloaded maximum engine speed baseline test (all controls in neutral).
•
Front pump test – operate “travel right” lever. Record values at all specified pressures.
•
Rear pump test – operate “travel left” lever. Record values at all specified pressures.
Record the values for each of the three tests (neutral, travel right and travel left) at the following pump
pressure levels, with travel speed control set at “high speed.”
Engine RPM
Pressure
Flow
100 kg/cm2 (1,422 psi)
135 kg/cm2 (1,930 psi)
180 kg/cm2 (2,560 psi)
240 kg/cm2 (3,413 psi)
320 kg/cm2 (4,550 psi)*
*See Note, below
Summary of Contents for Solar 300LC-V
Page 2: ......
Page 4: ......
Page 7: ...1SAFETY...
Page 8: ......
Page 46: ...S0102000 Page 38 Track Excavator Safety...
Page 47: ...1SPECIFICATIONS...
Page 48: ......
Page 54: ...S0202080K Page 6 Specifications for Solar 300LC V...
Page 70: ...S0202080K Page 22 Specifications for Solar 300LC V...
Page 71: ...1GENERAL MAINTENANCE...
Page 72: ......
Page 86: ...S0302000 Page 14 General Maintenance Procedures Return to Master Table of Contents...
Page 99: ...1UPPER STRUCTURE...
Page 100: ......
Page 102: ...S0402040K Page 2 Cab TABLE OF CONTENTS Removal 3 Installation 6...
Page 116: ...S0403050K Page 8 Counterweight Return to Master Table of Contents...
Page 140: ...S0407000 Page 6 Swing Bearing...
Page 164: ...S0408070K Page 24 Swing Reduction Gear...
Page 165: ...1LOWER STRUCTURE AND CHASSIS...
Page 166: ......
Page 190: ...S0505000 Page 24 Track Assembly 7 Tighten plug 1 Figure 48 Figure 48...
Page 191: ...S0505000 Page 25 Track Assembly TRACK SPRING AND TRACK ADJUSTING CYLINDER PARTS LIST Figure 49...
Page 193: ...1ENGINE AND DRIVE TRAIN...
Page 194: ......
Page 205: ...S0605060K Page 11 Air Conditioner Face and Defroster ARS1300L Figure 12...
Page 220: ...S0605060K Page 26 Air Conditioner...
Page 229: ...1HYDRAULICS...
Page 230: ......
Page 262: ...S0703010K Page 2 Accumulator TABLE OF CONTENTS General Description 3 Specifications 4...
Page 266: ...S0703010K Page 6 Accumulator...
Page 274: ...S0704080K Page 8 Center Joint Swivel...
Page 283: ...S0705000 Page 9 Cylinders...
Page 287: ...S0705000 Page 13 Cylinders...
Page 291: ...S0705000 Page 17 Cylinders...
Page 299: ...S0705000 Page 25 Cylinders...
Page 308: ...S0705000 Page 34 Cylinders 17 Force out pin bushing 1 from body of cylinder Figure 28...
Page 312: ...S0705000 Page 38 Cylinders...
Page 324: ...S0707270K Page 12 Swing Motor Toshiba MFC200 PARTS LIST Figure 6...
Page 355: ...S0707315K Page 11 Travel Motor with Gearbox...
Page 424: ...S0708315K Page 28 Main Pump Kawasaki CONSTRUCTION OF REGULATOR Figure 22...
Page 444: ...S0708315K Page 48 Main Pump Kawasaki...
Page 450: ...S0709401K Page 6 Main Control Valve Kayaba Figure 1...
Page 451: ...S0709401K Page 7 Main Control Valve Kayaba Figure 2...
Page 453: ...S0709401K Page 9 Main Control Valve Kayaba...
Page 455: ...S0709401K Page 11 Main Control Valve Kayaba Figure 4...
Page 467: ...S0709401K Page 23 Main Control Valve Kayaba Figure 16...
Page 500: ...S0709401K Page 56 Main Control Valve Kayaba Figure 54...
Page 552: ...S0792160K Page 6 Hydraulic Schematic S300LC V...
Page 553: ...1ELECTRICAL SYSTEM...
Page 554: ......
Page 608: ...S0802220K Page 54 Electrical System...
Page 627: ...S0802220K Page 73 Electrical System...
Page 634: ...S0892160K Page 4 Electrical Schematic S300LC V SOLAR 300LC V Figure 2...
Page 636: ...S0892160K Page 6 Electrical Schematic S300LC V...
Page 637: ...1ATTACHMENTS...
Page 638: ......
Page 658: ......