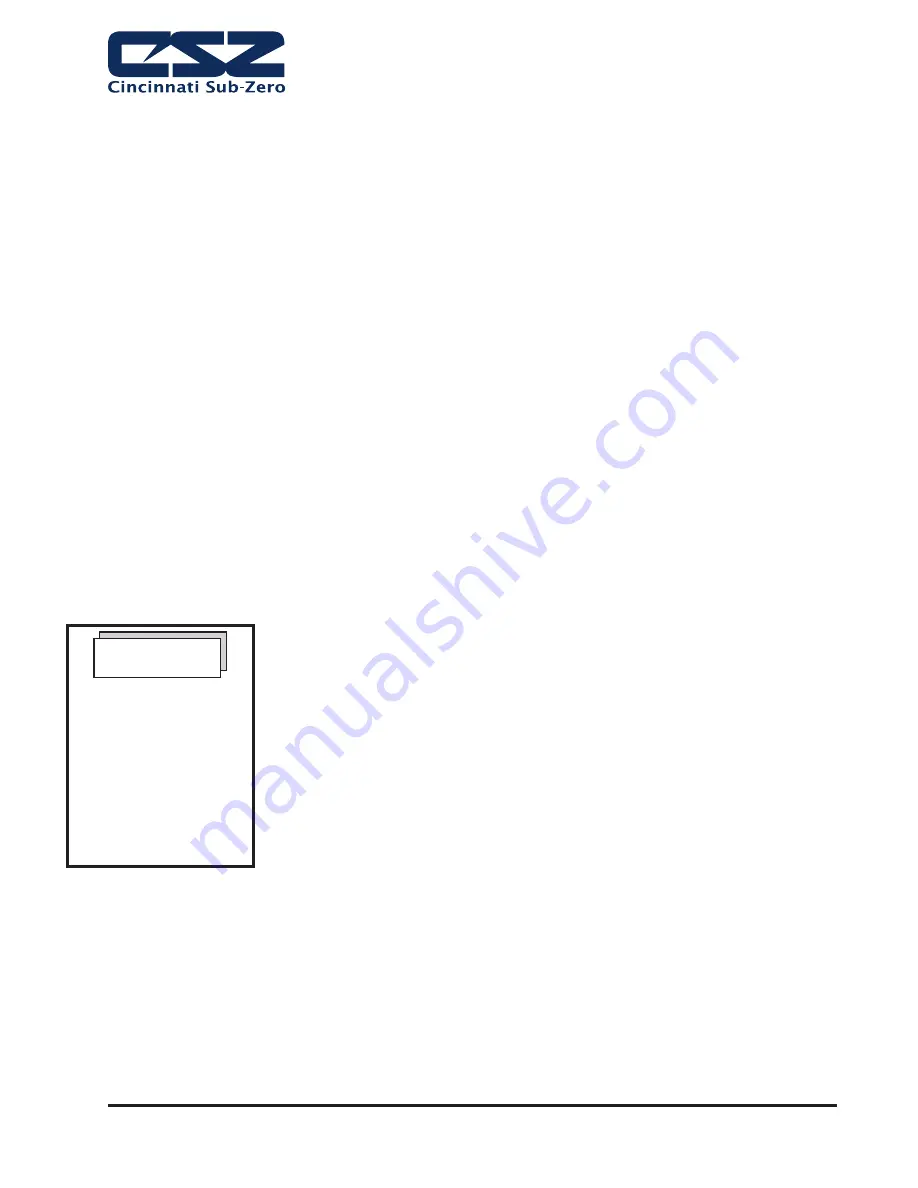
GENERAL DESCRIPTION
Page 2-21
Humidity Loop (Optional Equipment)
When humidity is called for, some of the liquid refrigerant is diverted to the humidity loop. The refrigerant
passes through a solenoid valve (item H27) and a wet coil capillary tube (item H23). Two phase refrigerant
exits the capillary tube and enters the wet coil (item H25). The wet coil is cold enough to attract moisture from
the chamber air, but not cold enough to freeze the water on the coil. The temperature of the coil is regulated
by a pressure regulating E.P.R. valve (item H26) and is intended to be a
fl
ooded coil by design. The warm
chamber air keeps the moisture from freezing on the coil. After the refrigerant leaves the wet coil, it enters the
suction line and returns to the compressor.
Bypass Loop
- The bypass circuit is composed of two lines in parallel. The Hot Gas Bypass Line, and the
Liquid Injection Line. The hot gas bypass line consists of a solenoid valve (item 17) and Hot Gas Bypass
Regulator (item 18). The liquid injection line consists of a Liquid Injection Solenoid (item 21) and Liquid
Injection T.E.V. (item 23). The hot gas bypass solenoid (item 17) will open and close opposite of the liquid
line solenoid (item 49). It will allow hot discharge refrigerant vapor to
fl
ow directly to the suction line. This is
done as a means to control cooling capacity or to “unload” the system. The liquid injection T.E.V. will sense
the temperature of the suction line. It will open automatically to feed liquid refrigerant into the suction line.
This will provide cooling for the hot gas that is being fed into the suction line. The cooling effect keeps the
compressor from overheating. There is also a discharge temperature control valve (item 78). This control
valve receives liquid refrigerant from the liquid line and injects it into the scroll compressor. This prevents the
compressor from overheating and results in no loss of capacity or mass
fl
ow.
TUNDRA
®
CONTROL SYSTEM
Refer to Refrigeration Diagram in Drawing Section
Mode: Normal cooling/heating
When there is call for cooling the liquid line solenoid (1-SOL), and the Liquid Injection
Solenoid (8-SOL) energize, the compressor turns on. High pressure switch (1 PS) will
turn off the compressor if a high discharge pressure is reached. Contact Cincinnati
Sub-Zero’s service department if this occurs. The high pressure switch automatically
resets.
When there is a call for cooling 1-SOL is energized. When the chamber is near the
set point the controller begins to cycle 1-SOL on and off. At the same time the hot
gas by-pass solenoid (9-SOL) is cycling on and off opposite of 1-SOL. If the controller
does not call for cooling for ninety seconds the refrigeration system will turn off.
For heating, solenoid 1-SOL is de-energized and the heaters are activated
Mode: Humidity (Optional Equipment)
In humidity mode, the system starts in the same manner as above with the following
differences:
When Dehumidi
fi
cation is called for, Solenoid H-11 SOL is energized. This allows
refrigerant to
fl
ow in the humidity loop.
When humidity is called for, Solenoid H-11 SOL is de-energized.
For Dry Bulb Temperature cooling in humidity mode, solenoid 1-SOL is energized.
This allows refrigerant to
fl
ow through the main cooling T.E.V. to reduce the
temperature of the chamber. For Dry Bulb Temperature heating, solenoid 1-SOL is
de-energized and the heaters are activated.
Sizes 3.5HP and 6HP scroll
compressors are rotation
sensitive. A phase monitor
is installed on these units to
prevent them from running
the wrong direction. The
phase monitor will alarm
on the EZT-570S if the
compressor(s) are wired
incorrectly
NOTE
Summary of Contents for ZP 16
Page 1: ...Installation Operation Maintenance Manual ZP Series 56120 REV AH 10 2019...
Page 4: ...INTRODUCTION THIS PAGE INTENTIONALLY LEFT BLANK...
Page 6: ...CHAMBER LABELS MEANINGS THIS PAGE INTENTIONALLY LEFT BLANK...
Page 40: ...GENERAL DESCRIPTION Page 2 24 THIS PAGE INTENTIONALLY LEFT BLANK...
Page 42: ...INSTALLATION Page 3 2 Figure 1 Transporting a Chamber...
Page 46: ...INSTALLATION Page 3 6 Table 2 Water Usage SI Units...
Page 62: ...OPERATION Page 4 14 THIS PAGE INTENTIONALLY LEFT BLANK...
Page 82: ...MAINTENANCE WITH Q A Page 5 20 THIS PAGE INTENTIONALLY LEFT BLANK...
Page 84: ...SERVICE PARTS WARRANTY Page 6 2 THIS PAGE INTENTIONALLY LEFT BLANK...
Page 88: ...SYSTEM DIAGRAMS Page 9 4 THIS PAGE INTENTIONALLY LEFT BLANK...