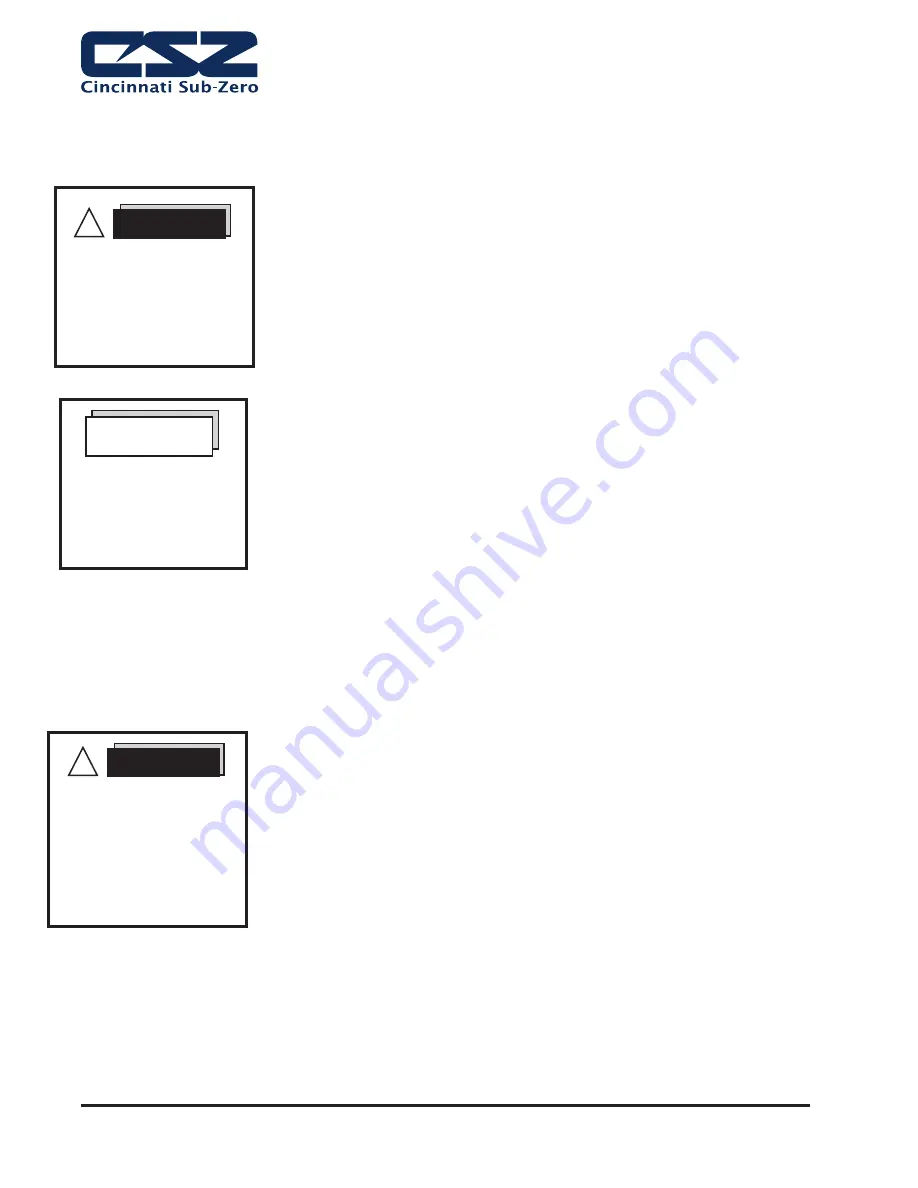
GENERAL DESCRIPTION
Page 2-12
PROGRAMMABLE DOOR LOCK (OPTIONAL)
The optional programmable door lock can be con
fi
gured to automatically lock or
unlock the chamber based on the desired con
fi
guration either at certain temperature
setpoints, or in pro
fi
le steps. See Chapter 4 of this manual for further details.
GN2 PURGE SYSTEM
(OPTIONAL)
The GN2Purge system must be vented outdoors. To prevent displacement of oxygen
around the unit. DO NOT enter the chamber while the boost/purge is turned on.
The door must be left open to ventilate the chamber before entering. A GN2 Purge
system reduces condensation within the test chamber and is used when low humidity
is required. The purge system consists of a control solenoid and
fl
ow meter. GN2
has a dewpoint approaching -300ºF (-185ºC) that when introduced into the chamber
workspace, creates a slightly positive pressure within the chamber to minimize
the migration of moist ambient air into the chamber. The system requires
approximately 5 scfm (142 std liters/minute) of GN2 at 70 psig (560 kpa).
DRY AIR PURGE (OPTIONAL)
A Dry Air Purge system can be provided to reduce condensation within the test
chamber and for use when low humidity is required. Compressed air is dried to a
dewpoint below -40ºF (-40ºC) then introduced into the chamber workspace, creating
a slightly positive pressure within the chamber to minimize the migration of moist
ambient air into the chamber. The system requires approximately 5 scfm (142 std
liters/minute) of compressed air at 90 psig (720 kpa) free of all oil and entrained water
droplets. The system features a dropout
fi
lter and oil removal
fi
lter at the inlet. See
Operating Instructions in Chapter 4 for more information regarding Dry Air Purge.
LIMITED TEMPERATURE SHEATH HEATER (OPTIONAL)
Each heater has its own temperature controller and redundant high limit safety. The
temperature controller is set to maintain the heater sheath temperature below 80% of
the auto ignition temperature of the
fl
uid or vapor in the chamber. The temperature
high limit is set +10°C above the temperature controller as a safety.
Per section 501-10 of the N.E.C.:
“The heater shall not exceed 80 percent of the ignition temperature in degrees Celsius
of the gas or vapor involved on any surface that is exposed to the gas or vapor when
continuously energized at the maximum rated ambient temperature.”
GAS MONITOR (OPTIONAL)
The optional gas monitoring system measures and detects hazardous gases. The
gases monitored are speci
fi
c to the application and determined based on what
products will be tested in the environmental test chamber. The gas monitor uses a
sampling hose for individual or multiple gases. Examples include carbon monoxide
(CO), carbon dioxide (CO2), hydrocarbons (HC), and variations in oxygen (O2)
content. When a gas is detected, the chamber will shut down and an alarm will be
shown on the chamber display. The gas monitor also includes a stand-alone display
which provides readings for the gases speci
fi
ed. The alarm setpoints can also be
adjusted as needed.
For additional details on the use and care of the Gas Monitor system, see the
manufacturer’s manual found in the Accessories folder on the electronic media.
A chamber equipped with
sheath heaters may no
longer posses a CE mark
in accordance to IEC
publication 610 10-1;
2000.
NOTE
Gaseous Nitrogen/CO2 vent
must be ducted out doors.
To prevent displacement
of oxygen around the unit.
Asphyxia can occur if this is
not installed properly.
WARNING
!
Check the Gas Monitor
water
fi
lter daily.
Empty
when full as required. Failure
to follow this procedure
will result in damage to
the Gas Monitor and is not
covered under warranty.
WARNING
!
Summary of Contents for ZP 16
Page 1: ...Installation Operation Maintenance Manual ZP Series 56120 REV AH 10 2019...
Page 4: ...INTRODUCTION THIS PAGE INTENTIONALLY LEFT BLANK...
Page 6: ...CHAMBER LABELS MEANINGS THIS PAGE INTENTIONALLY LEFT BLANK...
Page 40: ...GENERAL DESCRIPTION Page 2 24 THIS PAGE INTENTIONALLY LEFT BLANK...
Page 42: ...INSTALLATION Page 3 2 Figure 1 Transporting a Chamber...
Page 46: ...INSTALLATION Page 3 6 Table 2 Water Usage SI Units...
Page 62: ...OPERATION Page 4 14 THIS PAGE INTENTIONALLY LEFT BLANK...
Page 82: ...MAINTENANCE WITH Q A Page 5 20 THIS PAGE INTENTIONALLY LEFT BLANK...
Page 84: ...SERVICE PARTS WARRANTY Page 6 2 THIS PAGE INTENTIONALLY LEFT BLANK...
Page 88: ...SYSTEM DIAGRAMS Page 9 4 THIS PAGE INTENTIONALLY LEFT BLANK...