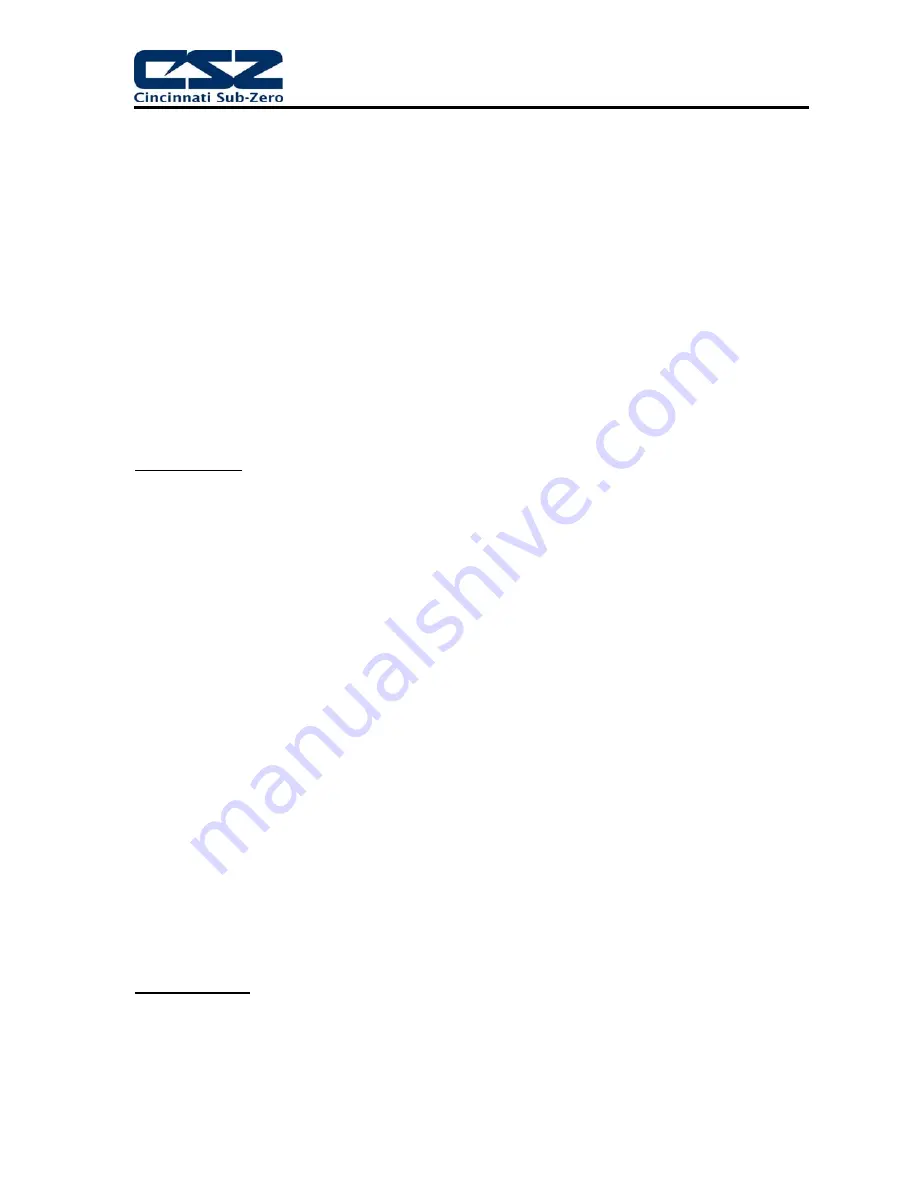
EZT-570S User Manual
62
Therefore, as the product set point is changed, the deviation band changes with it so you always
maintain an air temperature control range around the product set point. This provides a stable and
accurate control method throughout the product’s test range. Knowing what values to set for the
lower and upper set points may require some trial and error.
A good starting point is to run a simple air temperature control test where you set the air temperature
set point (no product control) to the upper test set point and then the lower test set point in order to
see how the product responds to the changing air temperature. During the transitions, monitor the
difference between the air temperature and the product temperature. Using the maximum difference
observed, double the value and use that as the lower set point. The upper set point should then be
set to four times that difference.
The reason for the larger offset on the heating side (upper set point) is due to the fact that when air
temperature increases, its density decreases. Cooler air is denser and thus has greater heat content
than warmer air. This increase in density transfers more heat between the product and air than at
warmer temperatures. Therefore, a larger deviation is required at warmer air temperatures in order to
maintain the same rate of heat transfer with the product.
Process Control
If there is a minimum and maximum air temperature that the product can be exposed too, which is, or
very close to, the minimum and maximum product temperature you need to achieve, process control
may be the better choice. This allows you to set the upper and lower set point limits that the air
temperature is allowed to reach regardless of the product temperature set point.
For example, if a product test requires it to run between 70 and -20, but the air temperature is not to
exceed 75 or -25, you can set the upper and lower product control set points to 75 and -25. The air
temperature loop will then be sent a set point between 75 and -25 regardless of what the product set
point is. This will maximize the rate of change of the product temperature by allowing the air
temperature set points to reach maximum limits. However, once the product reaches set point, the
larger air temperature control range may cause undesired oscillation once set point is achieved.
5.5.1.3
Implementing Product Control on “Live Loads”
A “live load” is a term describing a product that generates heat. This is typically some type of
electrical product that is being tested while under power. Live loads tend to lead the air temperature
when increasing in temperature, and can severely lag behind the air temperature when decreasing in
temperature since they are self-heating. Since they usually lag in only one direction, the product
control settings usually need to be adjusted to go considerably below the desired product temperature
in order to drive it to set point. The upper set point is typically a smaller value.
When using product control on a live load, the location of the product temperature sensor is critical.
Since the product is generating heat, placing the sensor on a heated component as compared to a
non-heated surface, like a portion of the product case, will dramatically affect performance and test
results. It is up to the user as to what component or location on the product is required to get the
proper test results. Just consider that if the sensor is placed on a heated surface, the chamber may
not be able to control it to the desired temperature due to airflow constraints or the amount of heat
being produced.
Deviation Control
Deviation control, when used for live loads, operates in the same manner as for dead loads described
above; however, determining the lower and upper set point limits are where they differ. The
maximum deviation between air temperature and product temperature should be found in the same
manner as for dead loads, but the value is then applied differently.
Summary of Contents for EZT-570S
Page 150: ......