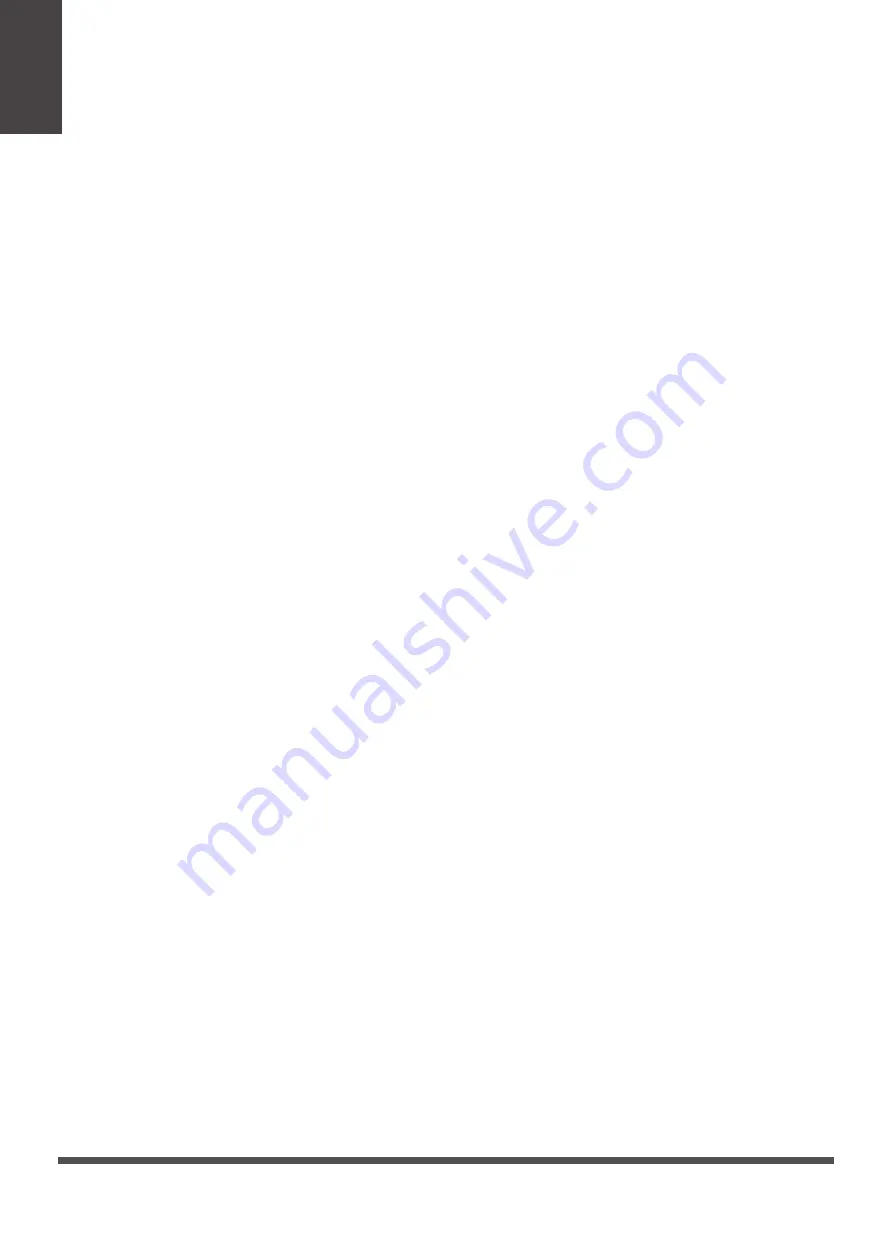
cylinders. (No more than 80 % volume liquid charge).i) Do not exceed the maximum working
pressure of thecylinder, even temporarily.j) When the cylinders have been filled correctly and the
process completed, make sure that the cylinders and the equipment are removed from site promptly
and all isolation valves on the equipment are closed off.k) Recovered refrigerant shall not be charged
into another refrigeration system unless it has been cleaned and checked.
15.Labelling
Equipment shall be labelled stating that it has been de-commissioned and emptied of refrigerant. The
label shall be dated and signed. Ensure that there are labels on the equipment stating the equipment
contains flammable refrigerant.
Before carrying out this procedure, it is essential that the technician is completely familiar with the
equipment and all its detail. It is recommended good practice that all refrigerants are recovered safely.
Prior to the task being carried out, an oil and refrigerant sample shall be taken in case analysis is
required prior to re-use of reclaimed refrigerant. It is essential that electrical power is available before
the task is commenced.
14.Decommissioning
a) Become familiar with the equipment and its operation.b) Isolate system electrically.c) Before
attempting the procedure ensure that: Mechanical handling equipment is available, if required, for
handling refrigerant cylinders;All personal protective equipment is available and being used correctly;
The recovery process is supervised at all times by a competent person; Recovery equipment and
cylinders conform to the appropriate standards.d) Pump down refrigerant system, if possible.e) If a
vacuum is not possible, make a manifold so that refrigerant can be removed from various parts of the
system.f) Make sure that cylinder is situated on the scales before recovery takes place.g) Start the
recovery machine and operate in accordance with manufacturer's instructions.h) Do not overfill
13.Charging procedures
In addition to conventional charging procedures, the following requirements shall be followed. Ensure
that contamination of different refrigerants does not occur when using charging equipment. Hoses or
lines shall be as short as possible to minimise the amount of refrigerant contained in them.
Cylinders shall be kept upright.
Ensure that the refrigeration system is earthed prior to charging the system with refrigerant.
Label the system when charging is complete (if not already).
Extreme care shall be taken not to overfill the refrigeration system. Prior to recharging the system it
shall be pressure tested with OFN. The system shall be leak tested on completion of charging but prior
to commissioning. A follow up leak test shall be carried out prior to leaving the site.
12.Removal and evacuation
When breaking into the refrigerant circuit to make repairs or for any other purpose conventional
procedures shall be used. However, it is important that best practice is followed since flammability is
a consideration. The following procedure shall be adhered to:
Remove refrigerant; Purge the circuit with inert gas; Evacuate; Purge again with inert gas; Open the
circuit by cutting or brazing.
The refrigerant charge shall be recovered into the correct recovery cylinders. The system shall be flu-
shed with OFN to render the unit safe. This process may need to be repeated several times. Comp-
ressed air oroxygen shall not be used for this task.
Flushing shall be achieved by breaking the vacuum in the system with OFN and continuing to fill until
the working pressure is achieved, then venting to atmosphere, and finally pulling down to a vacuum.
This process shall be repeated until no refrigerant is within the system. When the final OFN charge is
used, the system shall be vented down to atmospheric pressure to enable work to take place. This
operation is absolutely vital if brazing operations on the pipe-work are to take place.
Ensure that the outlet for the vacuum pump is not close to any ignition sources and there is ventila-
tion available.
Safety
Precautions
Page 8
Summary of Contents for CH-STLS-14AC
Page 27: ......