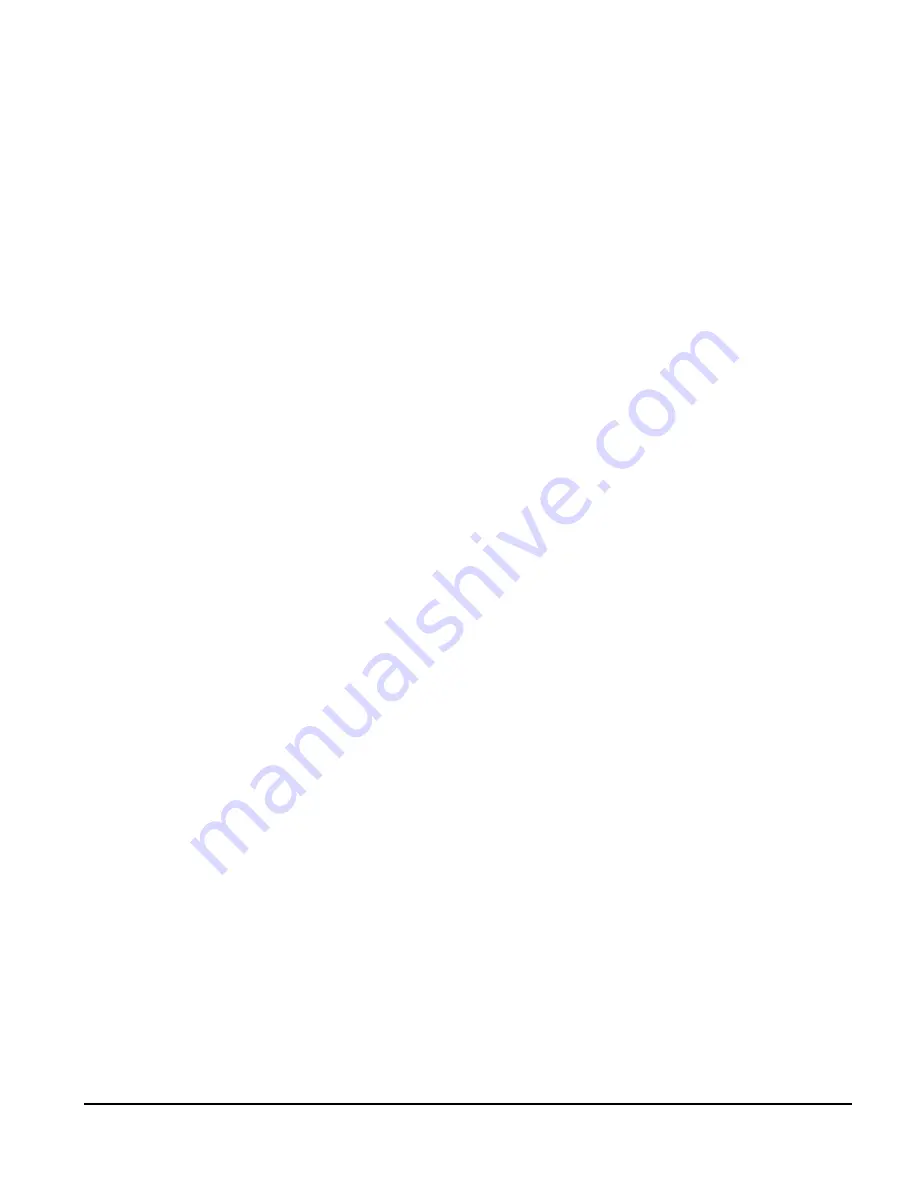
217
Tuning Procedures
Response
The Response adjusts the velocity and position loop bandwidths with a range of 1 to 500 Hz.
In general, it affects how quickly the drive will respond to commands, load disturbances and
velocity corrections. The effect of Response is greatly influenced by the status of the High
Performance Gains.
With High Performance Gains disabled, the actual command bandwidth of the drive system
will be equal to the Response value. In this case the load disturbance correction bandwidth is
very low (approximately 0.1 Hz). Increasing the Response value will reduce the drive’s
response time to velocity command changes but will not affect the response to load or speed
disturbances.
When High Performance Gains are enabled, the Response bandwidth is set to the Response
value. In this case, it reflects both the velocity command and the load disturbance correction
bandwidth. Increasing the Response when the High Performance Gains are enabled will
increase loop stiffness. With High Performance gains enabled, the maximum Response level
recommended is approximately 100 Hz.
If the Inertia Ratio and Friction values are exactly correct and the High Performance Gains
are enabled, changing the Response will not affect the damping (percent of overshoot and
number of ringout cycles) to velocity command changes or load disturbance corrections but
will affect their cycle frequency. The response level generally should be decreased as the load
to motor inertia ratio increases or if High Performance Gains are enabled.
Feedforwards
Feedforward gains are essentially open loop gains that generate torque commands based on
the commanded velocity, accel/decel and the known load parameters (Inertia Ratio and
Friction). Using the feedforwards reduces velocity error during steady state and reduces
overshoot during ramping. This is because the Feedforwards do not wait for error to build up
to generate current commands.
Feedforwards should be disabled unless the absolute maximum performance is required from
the system. Using them reduces the forgiveness of the servo loop and can create instability if
the actual inertia and/or friction of the machine varies greatly during operation or if the Inertia
Ratio or Friction parameters are not correct.
The internal feedforward velocity and acceleration gains are calculated by using the Inertia
Ratio and Friction parameters. The feedforward acceleration gain is calculated from the
Inertia Ratio parameter and the feedforward velocity gain is calculated from the Friction
parameter.
When Feedforwards are enabled, the accuracy of the Inertia Ratio and Friction parameters is
very important. If the Inertia Ratio parameter is larger than the actual inertia, the result would
be a significant velocity overshoot during ramping. If the Inertia parameter is smaller than the
actual inertia, velocity error during ramping will be reduced but not eliminated. If the Friction
parameter is greater than the actual friction, it may result in velocity error or instability. If the
Summary of Contents for FM-3
Page 2: ......
Page 14: ...xii ...
Page 16: ...2 FM 3 Programming Module Reference Manual Figure 2 FM 3 Programming Module Features ...
Page 128: ...114 FM 3 Programming Module Reference Manual ...
Page 156: ...142 FM 3 Programming Module Reference Manual ...
Page 196: ...182 FM 3 Programming Module Reference Manual ...
Page 238: ...224 FM 3 Programming Module Reference Manual ...
Page 251: ...237 Diagnostics and Troubleshooting Figure 97 Diagnostic Cable DGNE Diagram ...
Page 262: ...248 FM 3 Programming Module Reference Manual ...
Page 264: ...250 FM 3 Programming Module Reference Manual AX4 CEN CDRO ...
Page 265: ...251 Specifications Cable Diagrams ...
Page 266: ...252 FM 3 Programming Module Reference Manual SNCE XXX Cable SNCDD 001 5 Cable ...
Page 267: ...253 Specifications SNCO 003 Cable SNCI 003 Cable ...
Page 268: ...254 FM 3 Programming Module Reference Manual SNCLI 003 Cable ...
Page 272: ...258 FM 3 Programming Module Reference Manual TIA XXX Cable DDS XXX Cable ...
Page 274: ...260 FM 3 Programming Module Reference Manual CMDS XXX Cable CMMS XXX Cable ...
Page 275: ...261 Specifications CFCS XXX Cable ...
Page 276: ...262 FM 3 Programming Module Reference Manual CFCO XXX Cable ...
Page 277: ...263 Specifications CFOS XXX Cable ...
Page 278: ...264 FM 3 Programming Module Reference Manual ...
Page 286: ...272 FM 3 Programming Module Reference Manual ...
Page 290: ...276 FM 3 Programming Module Reference Manual ...
Page 291: ......