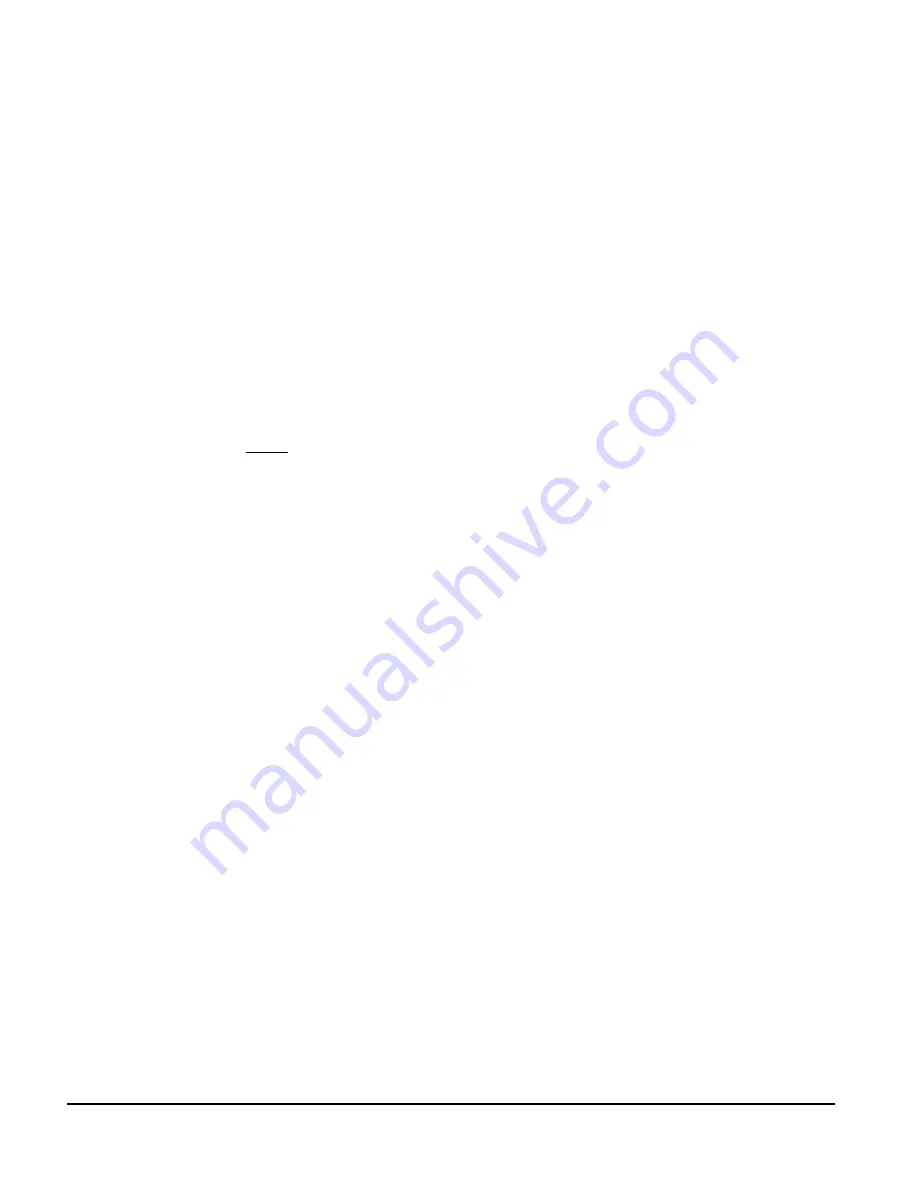
216
FM-3 Programming Module Reference Manual
Tuning Parameters
Inertia Ratio
Inertia Ratio specifies the load to motor inertia ratio and has a range of 0.0 to 50.0. A value
of 1.0 specifies that load inertia equals the motor inertia (1:1 load to motor inertia). The drives
can control up to a 10:1 inertia mismatch with the default Inertia Ratio value of 0.0. Inertial
mismatches of over 50:1 are possible if response is reduced.
The Inertia Ratio value is used to set the internal gains in the velocity and position loops,
including feedforward compensation if enabled.
To calculate the Inertia Ratio value, divide the load inertia reflected to the motor by the motor
inertia of the motor. Include the motor brake as a load where applicable. The resulting value
should be entered as the Inertia Ratio parameter.
Where:
IR = Inertia Ratio
RLI = Reflected Load Inertia (lb-in-sec
2
)
MI = Motor Inertia (lb-in- sec
2
)
If the exact inertia is unknown, a conservative approximate value should be used. If you enter
an inertia value higher than the actual inertia, the resultant motor response will tend to be
more oscillatory.
If you enter an inertia value lower than the actual inertia, but is between 10 and 90 percent of
the actual, the drive will tend to be more sluggish than optimum but will usually operate
satisfactorily. If the value you enter is less than 10 percent of the actual inertia, the drive will
have a low frequency oscillation at speed.
Friction
In the drive, this is a viscous friction parameter, characterized in terms of the rate of friction
increase per 100 motor RPM. The range is 0.00 to 100.00 in units of percent continuous
torque of the specified motor/drive combination. The Friction value can either be estimated
or measured.
If estimated, always use a conservative (less than or equal to actual) estimate. If the friction
is completely unknown, a value of zero should be used. A typical value used here would be
less than one percent.
If the value entered is higher than the actual, system oscillation is likely. If the value entered
is lower than the actual a more sluggish response is likely but generally results in good
operation.
MRI
RLI
R
I
=
Summary of Contents for FM-3
Page 2: ......
Page 14: ...xii ...
Page 16: ...2 FM 3 Programming Module Reference Manual Figure 2 FM 3 Programming Module Features ...
Page 128: ...114 FM 3 Programming Module Reference Manual ...
Page 156: ...142 FM 3 Programming Module Reference Manual ...
Page 196: ...182 FM 3 Programming Module Reference Manual ...
Page 238: ...224 FM 3 Programming Module Reference Manual ...
Page 251: ...237 Diagnostics and Troubleshooting Figure 97 Diagnostic Cable DGNE Diagram ...
Page 262: ...248 FM 3 Programming Module Reference Manual ...
Page 264: ...250 FM 3 Programming Module Reference Manual AX4 CEN CDRO ...
Page 265: ...251 Specifications Cable Diagrams ...
Page 266: ...252 FM 3 Programming Module Reference Manual SNCE XXX Cable SNCDD 001 5 Cable ...
Page 267: ...253 Specifications SNCO 003 Cable SNCI 003 Cable ...
Page 268: ...254 FM 3 Programming Module Reference Manual SNCLI 003 Cable ...
Page 272: ...258 FM 3 Programming Module Reference Manual TIA XXX Cable DDS XXX Cable ...
Page 274: ...260 FM 3 Programming Module Reference Manual CMDS XXX Cable CMMS XXX Cable ...
Page 275: ...261 Specifications CFCS XXX Cable ...
Page 276: ...262 FM 3 Programming Module Reference Manual CFCO XXX Cable ...
Page 277: ...263 Specifications CFOS XXX Cable ...
Page 278: ...264 FM 3 Programming Module Reference Manual ...
Page 286: ...272 FM 3 Programming Module Reference Manual ...
Page 290: ...276 FM 3 Programming Module Reference Manual ...
Page 291: ......