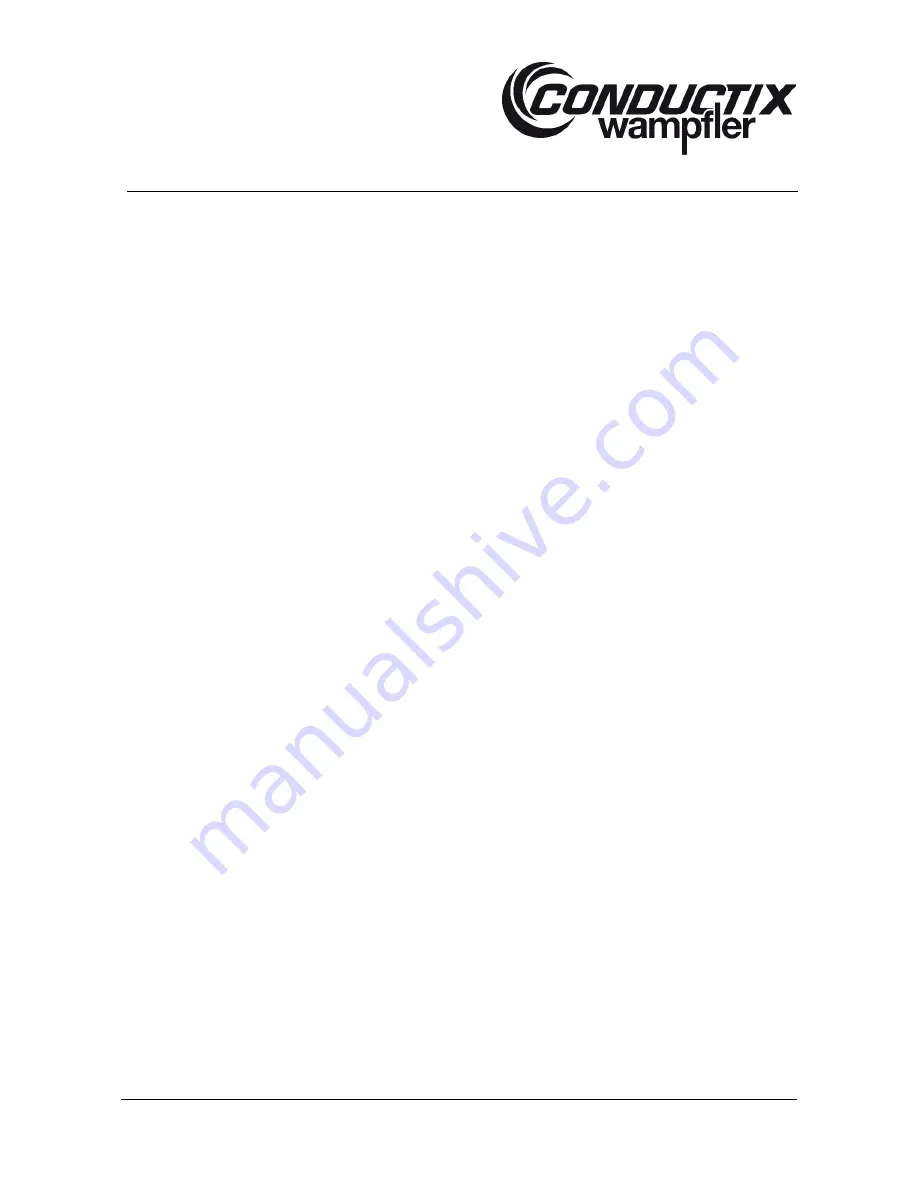
Operating Instructions
Single-pole Conductor Rail System
BAL0815-0002g-US
www.conductix.us
translated document
page 4 of 128
13
Index ....................................................................................................................................................................................... 127