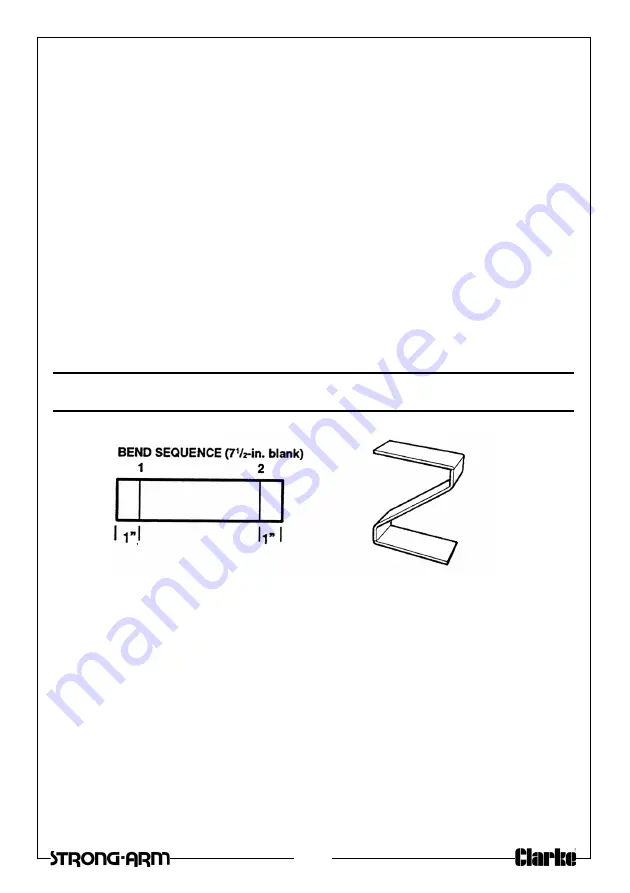
45
• 1 x 3-3/4” Blank
SETUP
Make chalk marks on the blank as shown on the “Bend Sequence.”
BEND NO. 1
Insert the blank into the Bender to the #1 chalk mark (as in A), and bend it to
80°. Re-check the angle.
BEND NO. 2
Slide the stock to the #2 chalk mark (as in B), and bend it to 80°. Re-check the
angle.
To remove the part, pull the pin from the sharp-angle-bend attachment.
FINISHING
Grind and sand all sharp corners.
LETTER Z
STOCK REQUIRED:
• 3/16” STOCK; 2” MAX WIDTH
• 2 x 7-1/2” Blanks
SETUP
Make chalk marks on the 7-1/2” blank as shown on the “Bend Sequence.”
BEND NO. 1
Insert the blank into the Bender to the #1 chalk mark (as in A), and bend it to
50°. Re-check the angle.