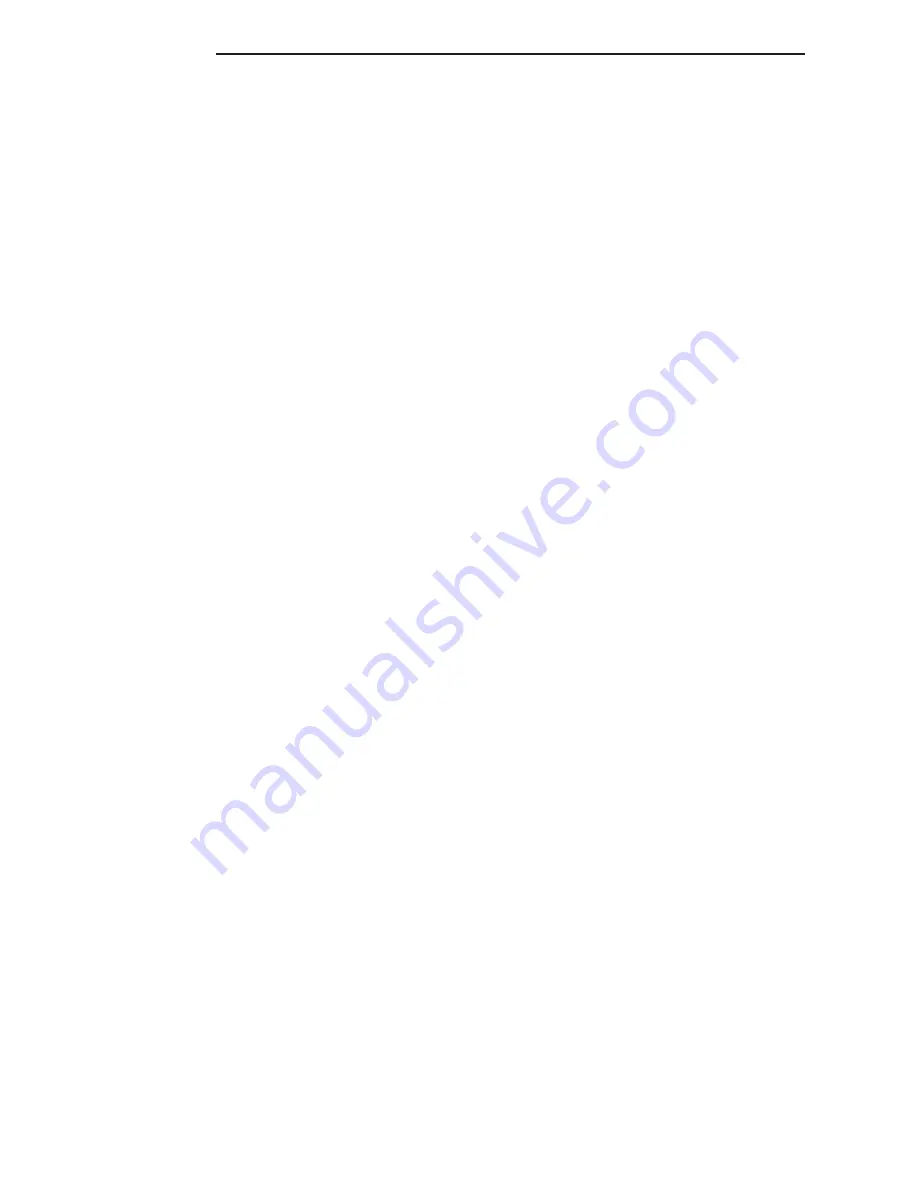
(4) Reverse and LR clutch pressure should read
165 to 235 psi.
(5) This test checks the reverse clutch hydraulic
circuit.
TEST RESULT INDICATIONS
(1) If proper line pressure is found in any one test,
the pump and pressure regulator are working prop-
erly.
(2) Low pressure in all positions indicates a defec-
tive pump, a clogged filter, or a stuck pressure regu-
lator valve.
(3) Clutch circuit leaks are indicated if pressures
do not fall within the specified pressure range.
(4) If the overdrive clutch pressure is greater than
5 psi in Step 4 of Test Three, a worn reaction shaft
seal ring or a defective solenoid assembly is indi-
cated.
(5) If the underdrive clutch pressure is greater
than 5 psi in Step 4 of Test 2A, a defective solenoid
assembly or TCM is the cause.
CLUTCH AIR PRESSURE TESTS
Inoperative clutches can be located using a series
of tests by substituting air pressure for fluid pressure
(Fig. 5) (Fig. 6). The clutches may be tested by apply-
ing air pressure to their respective passages. The
valve body must be removed and Tool 6056 installed.
To make air pressure tests, proceed as follows:
NOTE: The compressed air supply must be free of
all dirt and moisture. Use a pressure of 30 psi.
Remove oil pan and valve body. See Valve body
removal.
OVERDRIVE CLUTCH
Apply air pressure to the overdrive clutch apply
passage and watch for the push/pull piston to move
forward. The piston should return to its starting
position when the air pressure is removed.
REVERSE CLUTCH
Apply air pressure to the reverse clutch apply pas-
sage and watch for the push/pull piston to move rear-
ward. The piston should return to its starting
position when the air pressure is removed.
2/4 CLUTCH
Apply air pressure to the feed hole located on the
2/4 clutch retainer. Look in the area where the 2/4
piston contacts the first separator plate and watch
carefully for the 2/4 piston to move rearward. The
piston should return to its original position after the
air pressure is removed.
LOW/REVERSE CLUTCH
Apply air pressure to the low/reverse clutch feed
hole (rear of case, between 2 bolt holes). Then, look
in the area where the low/reverse piston contacts the
first separator plate. Watch carefully for the piston to
move forward. The piston should return to its origi-
nal position after the air pressure is removed.
UNDERDRIVE CLUTCH
Because this clutch piston cannot be seen, its oper-
ation is checked by function. Air pressure is applied
to the low/reverse and the 2/4 clutches. This locks the
output shaft. Use a piece of rubber hose wrapped
around the input shaft and a pair of clamp-on pliers
to turn the input shaft. Next apply air pressure to
the underdrive clutch. The input shaft should not
rotate with hand torque. Release the air pressure
and confirm that the input shaft will rotate.
FLUID LEAKAGE-TORQUE CONVERTER HOUSING
AREA
(1) Check for source of leakage.
(2) Fluid leakage at or around the torque converter
area may originate from an engine oil leak. The area
should be examined closely. Factory fill fluid is red
and, therefore, can be distinguished from engine oil.
(3) Prior to removing the transaxle, perform the
following checks:
(4) When leakage is determined to originate from
the transaxle, check fluid level prior to removal of
the transaxle and torque converter.
(5) High oil level can result in oil leakage out the
vent in the manual shaft. If the fluid level is high,
adjust to proper level.
(6) After performing this operation, inspect for
leakage. If a leak persists, perform the following
operation on the vehicle. This will determine if the
torque converter or transaxle is leaking.
TORQUE CONVERTER LEAKAGE
Possible sources of torque converter leakage are:
•
Torque converter weld leaks at the outside
(peripheral) weld.
•
Torque converter hub weld.
NOTE: Hub weld is inside and not visible. Do not
attempt to repair. Replace torque converter.
NOTE: If the torque converter must be replaced,
refer to Torque Converter Clutch Break-in Proce-
dure in this section. This procedure will reset the
transmission control module break-in status. Fail-
ure to perform this procedure may cause transaxle
shutter.
21 - 8
TRANSAXLE
JX
DIAGNOSIS AND TESTING (Continued)
Summary of Contents for 1997 Stratus Convertible LHD
Page 22: ......
Page 186: ......
Page 224: ......
Page 234: ......
Page 237: ...Charging System Schematic Typical JX CHARGING SYSTEM 8C 3 DIAGNOSIS AND TESTING Continued ...
Page 246: ......
Page 320: ......
Page 326: ......
Page 333: ...Fig 9 Wiper Motor Test JX WINDSHIELD WIPERS AND WASHERS 8K 7 DIAGNOSIS AND TESTING Continued ...
Page 358: ......
Page 380: ......
Page 386: ......
Page 396: ......
Page 398: ......
Page 414: ......
Page 464: ......
Page 468: ......
Page 472: ......
Page 496: ......
Page 532: ......
Page 536: ......
Page 572: ......
Page 584: ......
Page 592: ......
Page 598: ......
Page 610: ......
Page 624: ......
Page 628: ......
Page 632: ......
Page 636: ......
Page 640: ......
Page 702: ......
Page 726: ......
Page 733: ...Fig 8 Body Splices JX 8W 95 SPLICE LOCATIONS 8W 95 7 DESCRIPTION AND OPERATION Continued ...
Page 734: ...Fig 9 Rear Body Splices 8W 95 8 8W 95 SPLICE LOCATIONS JX DESCRIPTION AND OPERATION Continued ...
Page 735: ...Fig 10 Door Splices JX 8W 95 SPLICE LOCATIONS 8W 95 9 DESCRIPTION AND OPERATION Continued ...
Page 736: ......
Page 913: ...Fuel Line Adapter 1 4 JX FUEL SYSTEM 14 59 SPECIAL TOOLS Continued ...
Page 914: ......
Page 1033: ...41TE TRANSAXLE HYDRAULIC SCHEMATIC JX TRANSAXLE 21 65 SCHEMATICS AND DIAGRAMS Continued ...
Page 1034: ...41TE TRANSAXLE HYDRAULIC SCHEMATIC 21 66 TRANSAXLE JX SCHEMATICS AND DIAGRAMS Continued ...
Page 1035: ...41TE TRANSAXLE HYDRAULIC SCHEMATIC JX TRANSAXLE 21 67 SCHEMATICS AND DIAGRAMS Continued ...
Page 1036: ...41TE TRANSAXLE HYDRAULIC SCHEMATIC 21 68 TRANSAXLE JX SCHEMATICS AND DIAGRAMS Continued ...
Page 1037: ...41TE TRANSAXLE HYDRAULIC SCHEMATIC JX TRANSAXLE 21 69 SCHEMATICS AND DIAGRAMS Continued ...
Page 1038: ...41TE TRANSAXLE HYDRAULIC SCHEMATIC 21 70 TRANSAXLE JX SCHEMATICS AND DIAGRAMS Continued ...
Page 1039: ...41TE TRANSAXLE HYDRAULIC SCHEMATIC JX TRANSAXLE 21 71 SCHEMATICS AND DIAGRAMS Continued ...
Page 1040: ...41TE TRANSAXLE HYDRAULIC SCHEMATIC 21 72 TRANSAXLE JX SCHEMATICS AND DIAGRAMS Continued ...
Page 1041: ...41TE TRANSAXLE HYDRAULIC SCHEMATIC JX TRANSAXLE 21 73 SCHEMATICS AND DIAGRAMS Continued ...
Page 1042: ...41TE TRANSAXLE HYDRAULIC SCHEMATIC 21 74 TRANSAXLE JX SCHEMATICS AND DIAGRAMS Continued ...
Page 1043: ...41TE TRANSAXLE HYDRAULIC SCHEMATIC JX TRANSAXLE 21 75 SCHEMATICS AND DIAGRAMS Continued ...
Page 1044: ...41TE TRANSAXLE HYDRAULIC SCHEMATIC 21 76 TRANSAXLE JX SCHEMATICS AND DIAGRAMS Continued ...
Page 1045: ...41TE TRANSAXLE HYDRAULIC SCHEMATIC JX TRANSAXLE 21 77 SCHEMATICS AND DIAGRAMS Continued ...
Page 1054: ......
Page 1070: ......
Page 1166: ......
Page 1169: ...JX EMISSION CONTROL SYSTEMS 25 3 DESCRIPTION AND OPERATION Continued ...
Page 1196: ......