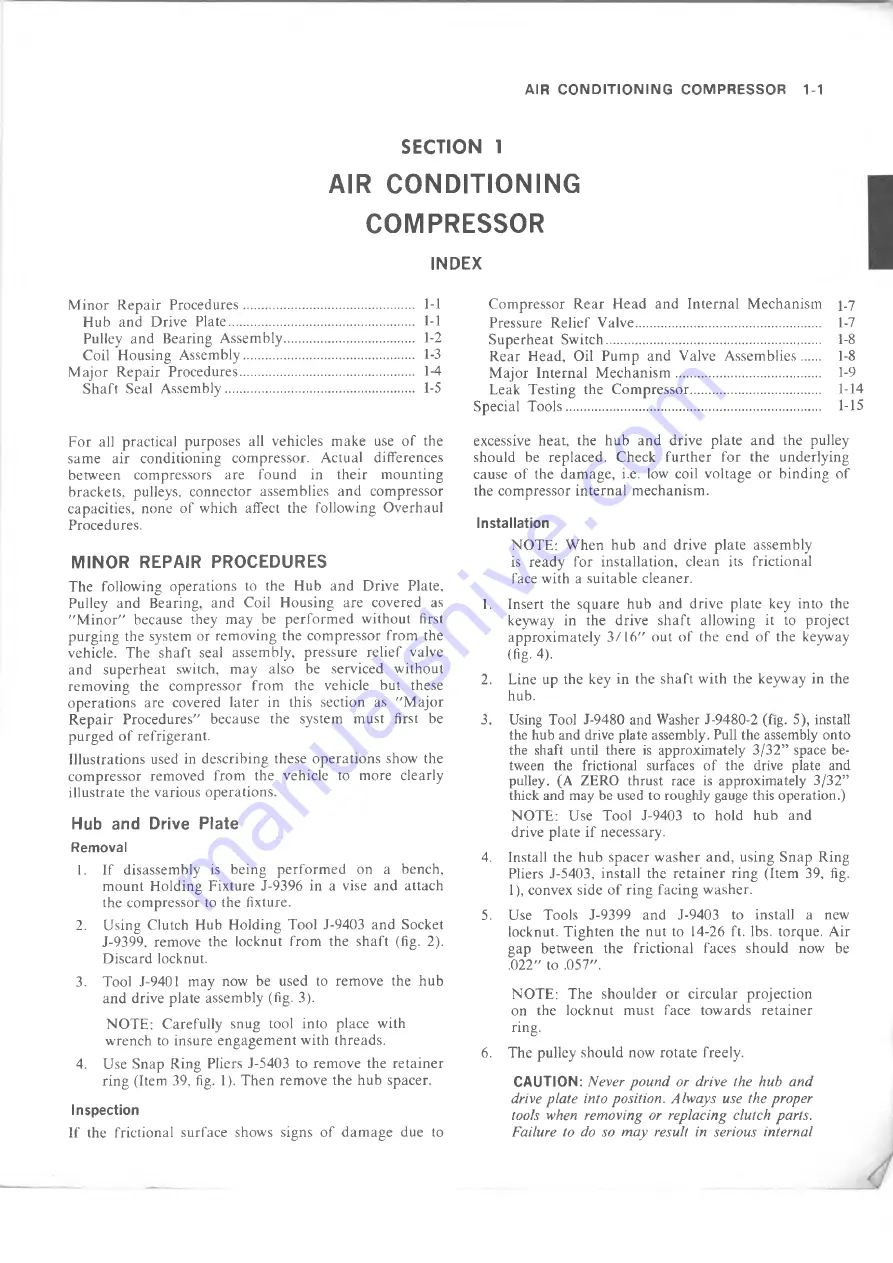
AIR C O N D I T I O N I N G CO M PR ES SO R
1-1
SECTION 1
AIR CONDITIONING
COMPRESSOR
INDEX
Hub and Drive Plate.......................................................1-1
Pulley and Bearing Assembly.......................................1-2
Coil Housing Assembly...................................................1-3
Shaft Seal Assembly........................................................1-5
For all practical purposes all vehicles make use of the
same air conditioning compressor. Actual differences
between compressors are found in their mounting
brackets, pulleys, connector assemblies and compressor
capacities, none of which affect the following Overhaul
Procedures.
M IN O R REPAIR PROCEDURES
The following operations to the Hub and Drive Plate,
Pulley and Bearing, and Coil Housing are covered as
"Minor" because they may be performed without first
purging the system or removing the compressor from the
vehicle. The shaft seal assembly, pressure relief valve
and superheat switch, may also be serviced without
removing the compressor from the vehicle but these
operations are covered later in this section as "Major
Repair Procedures" because the system must first be
purged of refrigerant.
Illustrations used in describing these operations show the
compressor removed from the vehicle to more clearly
illustrate the various operations.
Hub and Drive Plate
Removal
1. If disassembly is being performed on a bench,
mount Holding Fixture J-9396 in a vise and attach
the compressor to the fixture.
2. Using Clutch Hub Holding Tool J-9403 and Socket
J-9399, remove the locknut from the shaft (fig. 2).
Discard locknut.
3. Tool J-9401 may now be used to remove the hub
and drive plate assembly (fig. 3).
NOTE: Carefully snug tool into place with
wrench to insure engagement with threads.
4. Use Snap Ring Pliers J-5403 to remove the retainer
ring (Item 39, fig. 1). Then remove the hub spacer.
Inspection
If the frictional surface shows signs of damage due to
Compressor Rear Head and Internal Mechanism
1-7
Pressure Relief Valve.........................................................1-7
Superheat Switch..................................................................1-8
Rear Head, Oil Pump and Valve Assemblies.........1-8
Major Internal Mechanism......................................... ....1-9
Leak Testing the Compressor..................................... ....1-14
excessive heat, the hub and drive plate and the pulley
should be replaced. Check further for the underlying
cause of the damage, i.e. low coil voltage or binding of
the compressor internal mechanism.
Installation
NOTE: When hub and drive plate assembly
is ready for installation, clean its frictional
face with a suitable cleaner.
1. Insert the square hub and drive plate key into the
keyway in the drive shaft allowing it to project
approximately 3/16" out of the end of the keyway
(fig- 4).
2. Line up the key in the shaft with the keyway in the
hub.
3. Using Tool J-9480 and Washer J-9480-2 (fig. 5), install
the hub and drive plate assembly. Pull the assembly onto
the shaft until there is approximately 3/32” space be
tween the frictional surfaces of the drive plate and
pulley. (A ZERO thrust race is approximately 3/32”
thick and may be used to roughly gauge this operation.)
NOTE: Use Tool J-9403 to hold hub and
drive plate if necessary.
4. Install the hub spacer washer and, using Snap Ring
Pliers J-5403, install the retainer ring (Item 39, fig.
1), convex side of ring facing washer.
5. Use Tools J-9399 and J-9403 to install a new
locknut. Tighten the nut to 14-26 ft. lbs. torque. Air
gap between the frictional faces should now be
.022" to .057".
NOTE: The shoulder or circular projection
on the locknut must face towards retainer
ring.
6. The pulley should now rotate freely.
CAUTION:
Never pound or drive the hub and
drive plate into position. Always use the proper
tools when removing or replacing clutch parts.
Failure to do so may result in serious internal
Summary of Contents for 10 series 1973
Page 1: ......
Page 3: ...r...
Page 5: ......
Page 21: ......
Page 31: ......
Page 34: ...REAR AXLE DIFFERENTIAL CARRIER 4 3 OVERHAUL MANUAL...
Page 85: ...4 54 REAR AXLE DIFFERENTIAL CARRIER OVERHAUL MANUAL...
Page 93: ...4 62 REAR AXLE DIFFERENTIAL CARRIER OVERHAUL MANUAL...
Page 103: ...V...
Page 141: ...I...
Page 144: ...ENGINE 6 3 OIL PRESSURE SENDING UNIT Fig 1 In Line Engine Lubrication OVERHAUL MANUAL...
Page 179: ......
Page 185: ...6M 6 CARBURETORS Fig M6 Monojet See Fig M7 for legend...
Page 219: ...L...
Page 289: ...7M 70 CLUTCHES AND MANUAL TRANSMISSIONS Fig 13F Transfer Case Exploded View OVERHAUL MANUAL...
Page 352: ...AUTOMATIC TRANSMISSION 7A 49 Fig 85M Planetary Gear Train Exploded View OVERHAUL MANUAL...
Page 363: ...7A 60 AUTOMATIC TRANSMISSION Fig IT S ide Cross Section Typical OVERHAUL MANUAL...
Page 457: ......
Page 459: ......
Page 522: ......