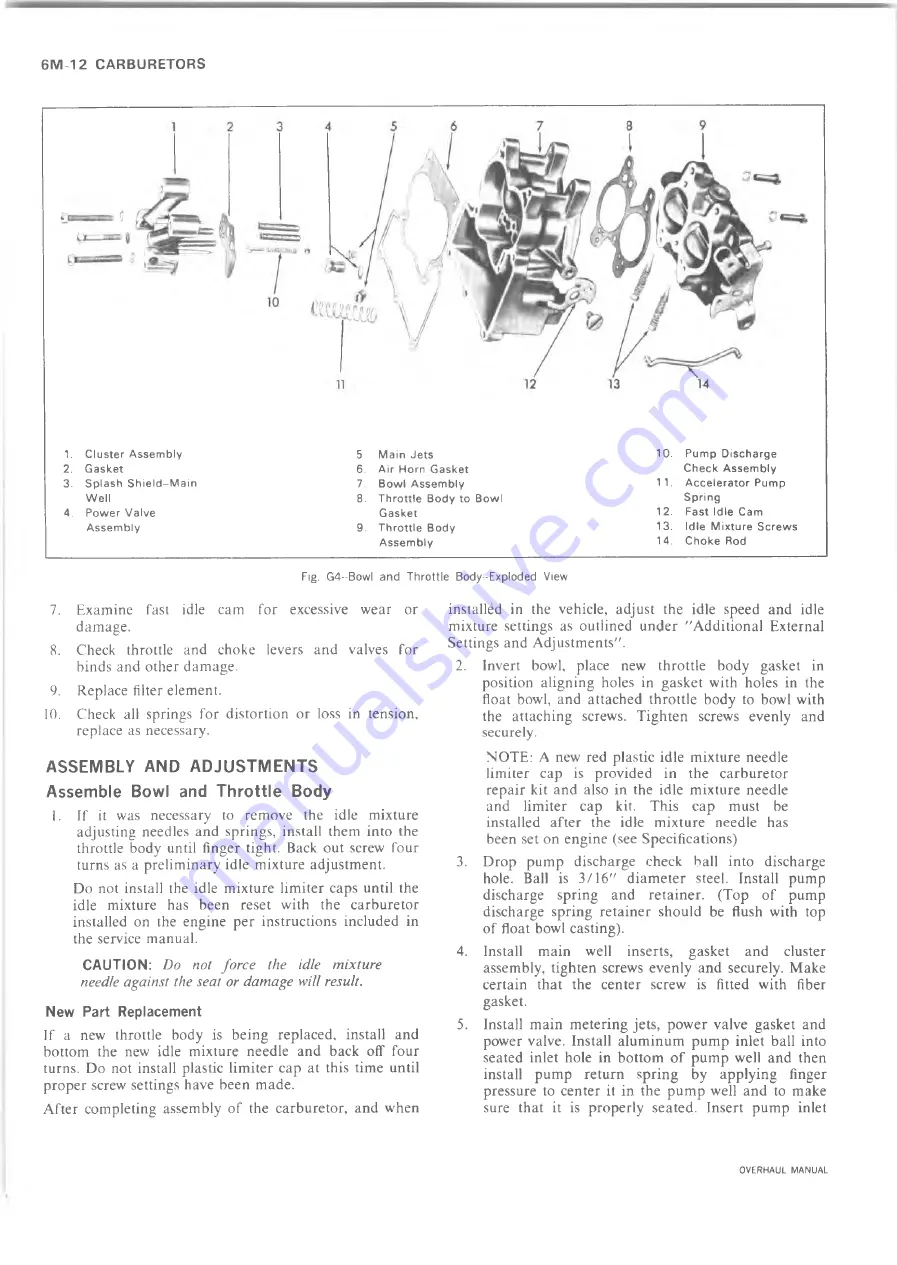
6 M 12 CARBURETORS
1.
C luster A ssem bly
2.
G asket
3.
S plash S h ie ld -M a in
W e ll
4.
Power V alve
A ssem bly
5
M ain Jets
6.
A ir Horn G asket
7.
B o w l Assem bly
8. T h ro ttle Body to B ow l
G asket
9. T h ro ttle Body
A sse m b ly
10.
Pum p D ischarge
C heck A ssem bly
11.
A c c e le ra to r Pump
S p rin g
1 2.
Fast Idle Cam
13.
Idle M ix tu re Screw s
1 4.
C hoke Rod
*
(}
Fig. G4--Bowl and T h ro ttle Body -Exploded View
7. Examine fast idle cam for excessive wear or
damage.
8. Check throttle and choke levers and valves for
binds and other damage.
9. Replace filter element.
10. Check all springs for distortion or loss in tension,
replace as necessary.
ASSEMBLY AND A D JU STM EN TS
Assemble Bowl and T h ro ttle Body
1. If it was necessary to remove the idle mixture
adjusting needles and springs, install them into the
throttle body until finger tight. Back out screw four
turns as a preliminary idle mixture adjustment.
Do not install the idle mixture limiter caps until the
idle mixture has been reset with the carburetor
installed on the engine per instructions included in
the service manual.
CAUTION:
Do not force the idle mixture
needle against the seat or damage will result.
New Part Replacement
If a new throttle body is being replaced, install and
bottom the new idle mixture needle and back off four
turns. Do not install plastic limiter cap at this time until
proper screw settings have been made.
After completing assembly of the carburetor, and when
installed in the vehicle, adjust the idle speed and idle
mixture settings as outlined under "Additional External
Settings and Adjustments".
2. Invert bowl, place new throttle body gasket in
position aligning holes in gasket with holes in the
float bowl, and attached throttle body to bowl with
the attaching screws. Tighten screws evenly and
securely.
NOTE: A new red plastic idle mixture needle
limiter cap is provided in the carburetor
repair kit and also in the idle mixture needle
and limiter cap kit. This cap must be
installed after the idle mixture needle has
been set on engine (see Specifications)
3. Drop pump discharge check ball into discharge
hole. Ball is 3/16" diameter steel. Install pump
discharge spring and retainer. (Top of pump
discharge spring retainer should be flush with top
of float bowl casting).
4. Install main well inserts, gasket and cluster
assembly, tighten screws evenly and securely. Make
certain that the center screw is fitted with fiber
gasket.
5. Install main metering jets, power valve gasket and
power valve. Install aluminum pump inlet ball into
seated inlet hole in bottom of pump well and then
install pump return spring by applying finger
pressure to center it in the pump well and to make
sure that it is properly seated. Insert pump inlet
OVERHAUL MANUAL
Summary of Contents for 10 series 1973
Page 1: ......
Page 3: ...r...
Page 5: ......
Page 21: ......
Page 31: ......
Page 34: ...REAR AXLE DIFFERENTIAL CARRIER 4 3 OVERHAUL MANUAL...
Page 85: ...4 54 REAR AXLE DIFFERENTIAL CARRIER OVERHAUL MANUAL...
Page 93: ...4 62 REAR AXLE DIFFERENTIAL CARRIER OVERHAUL MANUAL...
Page 103: ...V...
Page 141: ...I...
Page 144: ...ENGINE 6 3 OIL PRESSURE SENDING UNIT Fig 1 In Line Engine Lubrication OVERHAUL MANUAL...
Page 179: ......
Page 185: ...6M 6 CARBURETORS Fig M6 Monojet See Fig M7 for legend...
Page 219: ...L...
Page 289: ...7M 70 CLUTCHES AND MANUAL TRANSMISSIONS Fig 13F Transfer Case Exploded View OVERHAUL MANUAL...
Page 352: ...AUTOMATIC TRANSMISSION 7A 49 Fig 85M Planetary Gear Train Exploded View OVERHAUL MANUAL...
Page 363: ...7A 60 AUTOMATIC TRANSMISSION Fig IT S ide Cross Section Typical OVERHAUL MANUAL...
Page 457: ......
Page 459: ......
Page 522: ......