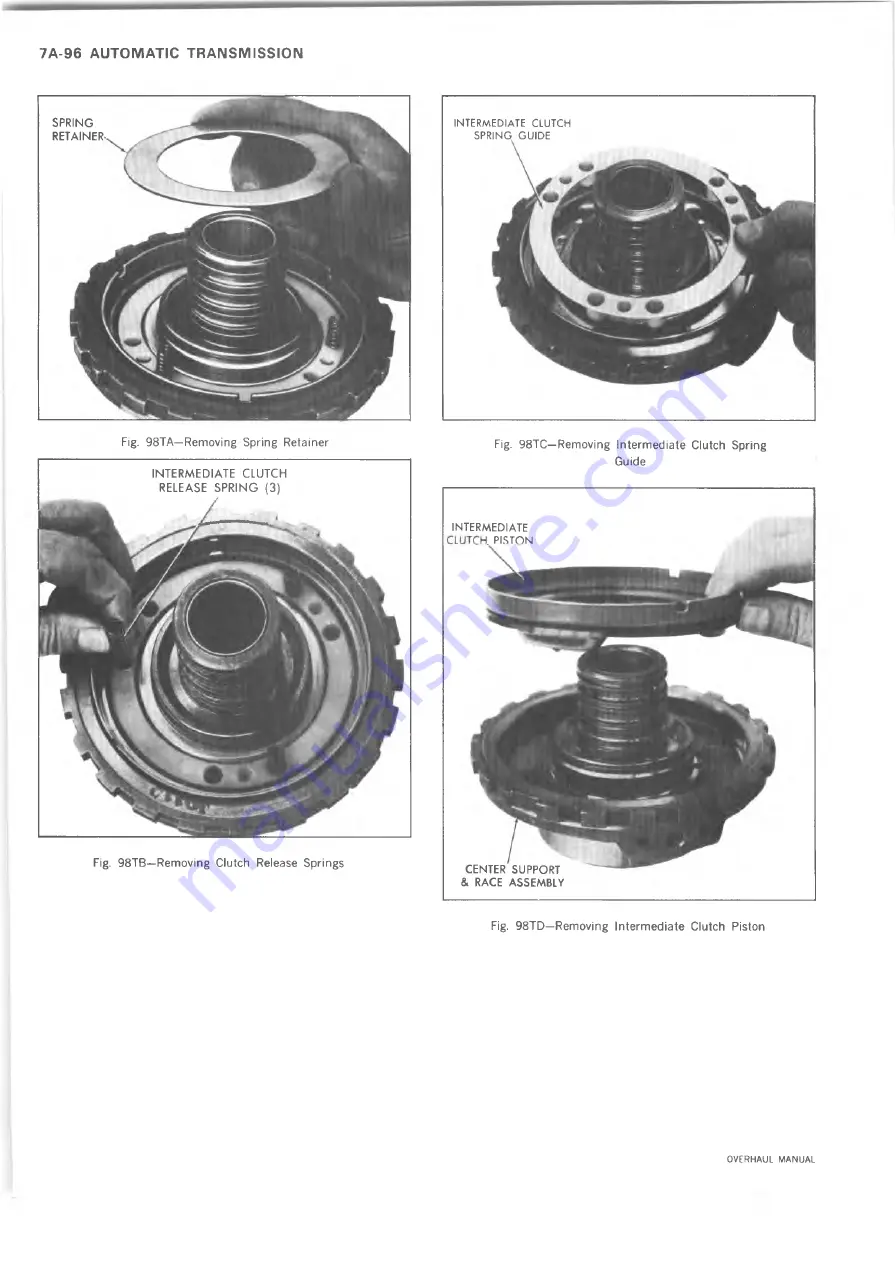
7 A -9 6 A U T O M A T IC T R A N S M IS S IO N
SPRIN G
RETAINER-
INTERMEDIATE CLUTCH
SPRING GUIDE
Fig. 98TC— Removing Intermediate Clutch Spring
Guide
Fig. 98TA— Removing Spring Retainer
IN T ERM ED IA TE CLUTCH
RELEASE S P R IN G (3)
Fig. 98T B— Removing Clutch Release Springs
CENTER SUPPORT
& RACE ASSEMBLY
INTERMEDIATE
___ P IS T O N
Fig. 98T D — Removing Intermediate Clutch Piston
OVERHAUL MANUAL
Summary of Contents for 10 series 1973
Page 1: ......
Page 3: ...r...
Page 5: ......
Page 21: ......
Page 31: ......
Page 34: ...REAR AXLE DIFFERENTIAL CARRIER 4 3 OVERHAUL MANUAL...
Page 85: ...4 54 REAR AXLE DIFFERENTIAL CARRIER OVERHAUL MANUAL...
Page 93: ...4 62 REAR AXLE DIFFERENTIAL CARRIER OVERHAUL MANUAL...
Page 103: ...V...
Page 141: ...I...
Page 144: ...ENGINE 6 3 OIL PRESSURE SENDING UNIT Fig 1 In Line Engine Lubrication OVERHAUL MANUAL...
Page 179: ......
Page 185: ...6M 6 CARBURETORS Fig M6 Monojet See Fig M7 for legend...
Page 219: ...L...
Page 289: ...7M 70 CLUTCHES AND MANUAL TRANSMISSIONS Fig 13F Transfer Case Exploded View OVERHAUL MANUAL...
Page 352: ...AUTOMATIC TRANSMISSION 7A 49 Fig 85M Planetary Gear Train Exploded View OVERHAUL MANUAL...
Page 363: ...7A 60 AUTOMATIC TRANSMISSION Fig IT S ide Cross Section Typical OVERHAUL MANUAL...
Page 457: ......
Page 459: ......
Page 522: ......