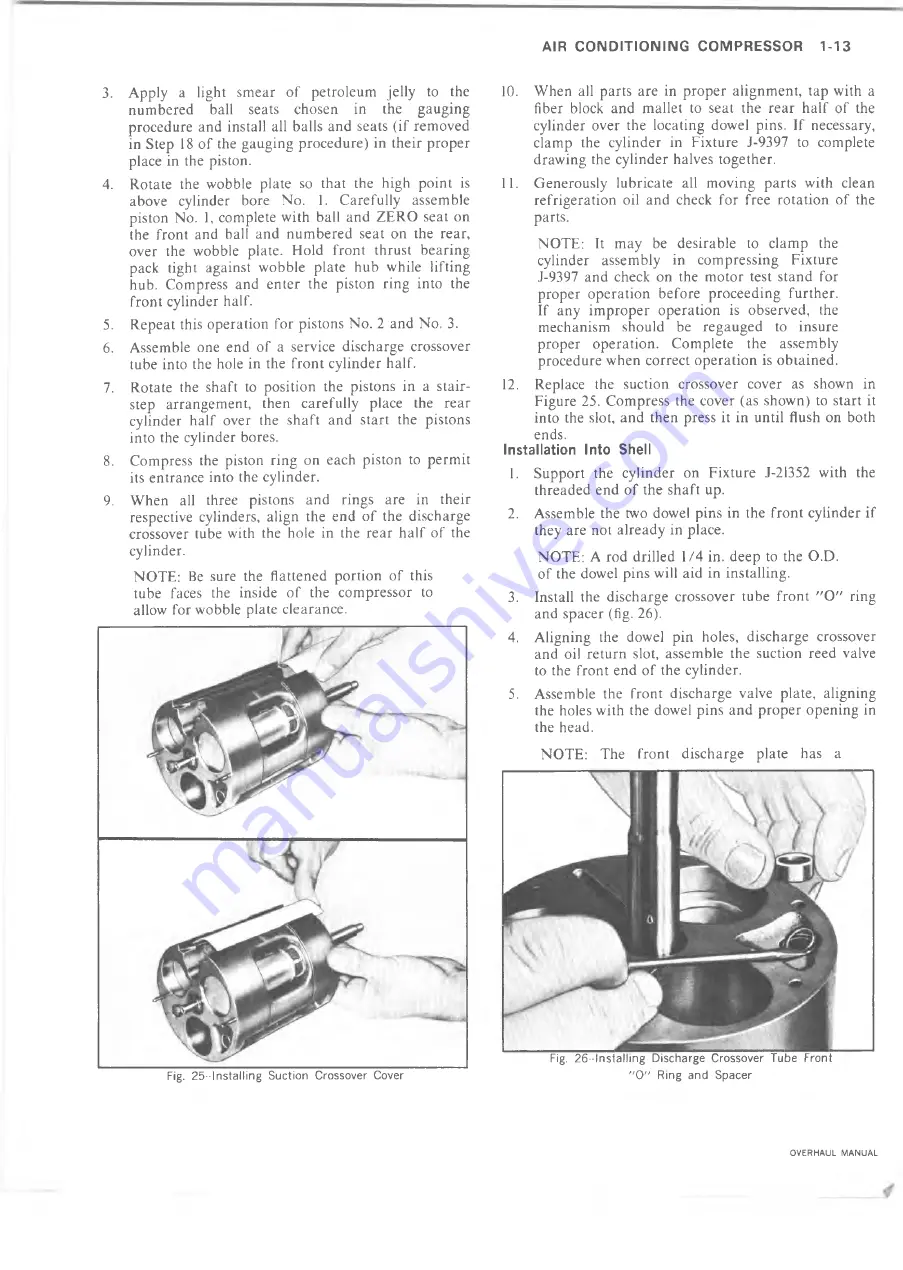
AIR C O N D IT I O N I N G CO M PR ES SO R
1-13
3. Apply a light smear of petroleum jelly to the
numbered ball seats chosen in the gauging
procedure and install all balls and seats (if removed
in Step 18 of the gauging procedure) in their proper
place in the piston.
4. Rotate the wobble plate so that the high point is
above cylinder bore No. 1. Carefully assemble
piston No. 1, complete with ball and ZERO seat on
the front and ball and numbered seat on the rear,
over the wobble plate. Hold front thrust bearing
pack tight against wobble plate hub while lifting
hub. Compress and enter the piston ring into the
front cylinder half.
5. Repeat this operation for pistons No. 2 and No. 3.
6. Assemble one end of a service discharge crossover
tube into the hole in the front cylinder half.
7. Rotate the shaft to position the pistons in a stair
step arrangement, then carefully place the rear
cylinder half over the shaft and start the pistons
into the cylinder bores.
8. Compress the piston ring on each piston to permit
its entrance into the cylinder.
9. When all three pistons and rings are in their
respective cylinders, align the end of the discharge
crossover tube with the hole in the rear half of the
cylinder.
NOTE: Be sure the flattened portion of this
tube faces the inside of the compressor to
allow for wobble plate clearance.
10. When all parts are in proper alignment, tap with a
fiber block and mallet to seat the rear half of the
cylinder over the locating dowel pins. If necessary,
clamp the cylinder in Fixture J-9397 to complete
drawing the cylinder halves together.
11. Generously lubricate all moving parts with clean
refrigeration oil and check for free rotation of the
parts.
NOTE: It may be desirable to clamp the
cylinder assembly in compressing Fixture
J-9397 and check on the motor test stand for
proper operation before proceeding further.
If any improper operation is observed, the
mechanism should be regauged to insure
proper operation. Complete the assembly
procedure when correct operation is obtained.
12. Replace the suction crossover cover as shown in
Figure 25. Compress the cover (as shown) to start it
into the slot, and then press it in until flush on both
ends.
Installation Into Shell
1. Support the cylinder on Fixture J-21352 with the
threaded end of the shaft up.
2. Assemble the two dowel pins in the front cylinder if
they are not already in place.
NOTE: A rod drilled 1/4 in. deep to the O.D.
of the dowel pins will aid in installing.
3. Install the discharge crossover tube front "O" ring
and spacer (fig. 26).
4. Aligning the dowel pin holes, discharge crossover
and oil return slot, assemble the suction reed valve
to the front end of the cylinder.
5. Assemble the front discharge valve plate, aligning
the holes with the dowel pins and proper opening in
the head.
Fig. 2 5 - 1nstalling Suction Crossover Cover
NOTE: The front discharge plate has a
Fig. 2 6 -In s ta llin g Discharge Crossover Tube Front
" O " Ring and Spacer
OVERHAUL MANUAL
Summary of Contents for 10 series 1973
Page 1: ......
Page 3: ...r...
Page 5: ......
Page 21: ......
Page 31: ......
Page 34: ...REAR AXLE DIFFERENTIAL CARRIER 4 3 OVERHAUL MANUAL...
Page 85: ...4 54 REAR AXLE DIFFERENTIAL CARRIER OVERHAUL MANUAL...
Page 93: ...4 62 REAR AXLE DIFFERENTIAL CARRIER OVERHAUL MANUAL...
Page 103: ...V...
Page 141: ...I...
Page 144: ...ENGINE 6 3 OIL PRESSURE SENDING UNIT Fig 1 In Line Engine Lubrication OVERHAUL MANUAL...
Page 179: ......
Page 185: ...6M 6 CARBURETORS Fig M6 Monojet See Fig M7 for legend...
Page 219: ...L...
Page 289: ...7M 70 CLUTCHES AND MANUAL TRANSMISSIONS Fig 13F Transfer Case Exploded View OVERHAUL MANUAL...
Page 352: ...AUTOMATIC TRANSMISSION 7A 49 Fig 85M Planetary Gear Train Exploded View OVERHAUL MANUAL...
Page 363: ...7A 60 AUTOMATIC TRANSMISSION Fig IT S ide Cross Section Typical OVERHAUL MANUAL...
Page 457: ......
Page 459: ......
Page 522: ......