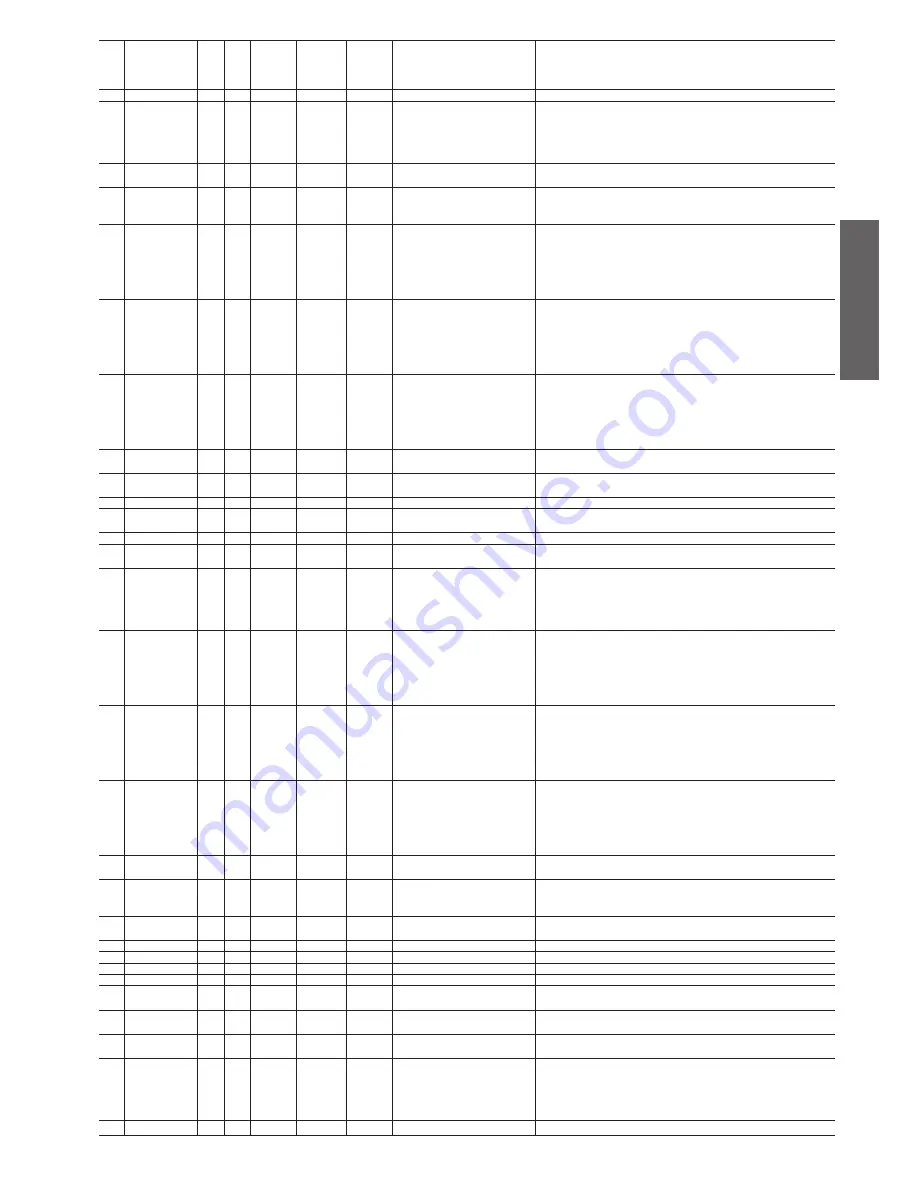
37
ENGL
ISH
EVD
4
+030220227 - rel. 2.1 - 12.06.2008
HP-Proportional
gain
A
26
3
3
3
PID proportional factor in HP mode
This is the PID proportional factor for operation in HP mode, increasing the value in-
creases the reactivity of the valve and therefore of SH control, however for high values
control may become unstable. This depends on the ratio between circuit capacity and
valve capacity and on the maximum number of valve control steps.
HP-Superheat set
A
23
7
7
10
superheat set point in HP mode
Superheat set point in HP mode
KEY1
I
1
0
0
0
special functions
“If set to 14797, allows the user to reset all the parameters to the default values, by
enabling the Reset to default variable. If set to 19157, allows the user to remain in
functional test mode, enabling the Functional test variable within 30 s from when the
driver is switched on (see the paragraph “”Application as positioner”” in the EVD400
Manual)”
KEY11
I
11
0
0
0
enable write advanced valve parameters
if set to 24717 (Service only)
Enable write advanced valve parameters if set to 24717 (Service only)
KEY12
I
14
0
0
0
special functions
If set to 12233 within 250 s from when the driver is switched on, disables the termina-
tion of the functional test by timeout (see the paragraph “Application as positioner” in
the EVD400 Manual)
LOP Cool Mode
A
50
-5
-5
-45
temperature at minimum operating
pressure (MOP) in CH mode
Temperature at the minimum operating pressure allowed at the evaporator outlet, in
CH mode. When the temperature is less than the set threshold, the system goes into
LOP status, activating the LOP status digital variable and LOP control: the driver stops
SH control and starts controlling the valve position so as to reach the LOP set point,
considering the LOP integral time parameter. The driver resumes SH control when the
temperature returns above the set threshold.
LOP Defr. Mode
A
52
-30
-30
-30
temperature at minimum operating
pressure (LOP) in DF mode
Temperature at the minimum operating pressure allowed at the evaporator outlet, in
DF mode. When the temperature is less than the set threshold, the system goes into
LOP status, activating the LOP status digital variable and LOP control: the driver stops
SH control and starts controlling the valve position so as to reach the LOP set point,
considering the LOP integral time parameter. The driver resumes SH control when the
temperature returns above the set threshold.
LOP Heat Mode
A
51
-25
-20
-45
temperature at minimum operating
pressure (LOP) in HP mode
Temperature at the minimum operating pressure allowed at the evaporator outlet, in
HP mode. When the temperature is less than the set threshold, the system goes into
LOP status, activating the LOP status digital variable and LOP control: the driver stops
SH control and starts controlling the valve position so as to reach the LOP set point,
considering the LOP integral time parameter. The driver resumes SH control when the
temperature returns above the set threshold.
LOP integral time
A
34
1,5
1,5
0
integral time for low evaporation
pressure control (LOP)
Integral time for low evaporation pressure (LOP) control, see LOP cool mode
LOP status
D
50
0
0
0
active when in minimum evaporation
pressure control status
Active when in LOP control status, see LOP cool mode
Low SH int. time
A
33
1
1
15
integral time for low superheat control
Integral time for low superheat control, see CH-Low Superheat
Low SH status
D
52
0
0
0
active when in low superheat control
status
Active when the superheat measured is lower than CH-Low Superheat (or similar in
HP or DF mode)
Maximum steps
I
23
480
480
480
maximum control steps
Position beyond which the valve is considered completely open
Minimum steps
I
22
30
30
30
minimum control steps
Position below which the valve is considered closed. This parameter is only used
during repositioning (see CH-Circuit/EEV Ratio)
MODE
I
16
0
0
0
READ ONLY, received from µC
2
“Received from µC
2
, describes the type of cycle that the main controller is managing:
0 = cooling (CH)
1 = heating (HP)
2 = defrost (DF)
3 = pump-down”
MOP Cool Mode
A
53
12
80
80
temperature at maximum operating
pressure (MOP) in CH mode
Temperature at the maximum operating pressure allowed at the evaporator outlet, in
CH mode. When the temperature is greater than the set threshold, the system enters
MOP status, activating the MOP status digital variable and MOP control: the driver
stops SH control and starts controlling the valve position so as to reach the MOP set
point, considering the MOP integral time parameter. The driver resumes SH control
when the temperature returns below the set threshold.
MOP Defr. Mode
A
55
30
30
30
temperature at maximum operating
pressure (MOP) in DF mode
Temperature at the maximum operating pressure allowed at the evaporator outlet, in
DF mode. When the temperature is greater than the set threshold, the system enters
MOP status, activating the MOP status digital variable and MOP control: the driver
stops SH control and starts controlling the valve position so as to reach the MOP set
point, considering the MOP integral time parameter. The driver resumes SH control
when the temperature returns below the set threshold.
MOP Heat Mode
A
54
12
12
80
temperature at maximum operating
pressure (MOP) in HP mode
Temperature at the maximum operating pressure allowed at the evaporator outlet, in
HP mode. When the temperature is greater than the set threshold, the system enters
MOP status, activating the MOP status digital variable and MOP control: the driver
stops SH control and starts controlling the valve position so as to reach the MOP set
point, considering the MOP integral time parameter. The driver resumes SH control
when the temperature returns below the set threshold.
MOP integral time
A
35
2,5
2,5
0
integral time for high evaporation
pressure control (MOP)
Integral time for high evaporation pressure (MOP) control, see MOP cool mode
MOP startup delay
I
49
60
60
60
MOP delay time when starting control
When the system is started, the evaporation pressure is high and may exceed the set
MOP threshold. The duration of the MOP delay time can be set when starting the
controller
MOP status
D
49
0
0
0
active when in maximum evaporation
pressure control status
Active when in MOP control status, see MOP cool mode
Net address
I
21
2
30
250
network address
Network address
NUMRESTART
I
91
0
0
0
EVD
4
start counter (power supply).
EVD
4
start counter (power supply) and reset.
NUMVALVECLOSE
I
93
0
0
0
valve closing counter.
Valve closing counter.
NUMVALVEOPEN
I
92
0
0
0
EVD
4
start counter with valve error.
EVD
4
start counter with valve error.
Off SH cl
A
46
0
0
10
superheat offset with modulating
temperature in CH mode
Superheat offset with modulating temperature in CH mode
Open relay low SH D
60
1
0
1
enable/disable relay opening following
low superheat
Enables/disables the opening of the relay when the driver is in Low SH status
Open relay MOP
D
61
0
0
0
enable/disable relay opening following
MOP
Enables/disables the opening of the relay when the driver is in MOP status
Opening extra steps I
63
enable extra steps in opening
When the valve has reached the 100% of the control steps in opening, as set by
the parameters for each valve or the Maximum steps parameter, and the procedure
requires further opening, the driver attempts to further open the valve by controlling
[Maximum steps/128] steps every second, if this parameter is enabled. In addition,
allows any steps lost during control, when opening, to be recovered. Used by pCO
Phase current
I
27
450
450
450
peak current per phase
Peak current that the driver supplies to each valve control phase
Summary of Contents for EVD4
Page 1: ...EVD4 Driver for electronic expansion valve User manual...
Page 2: ......
Page 3: ...User manual...
Page 6: ...6...
Page 44: ...44...
Page 47: ......