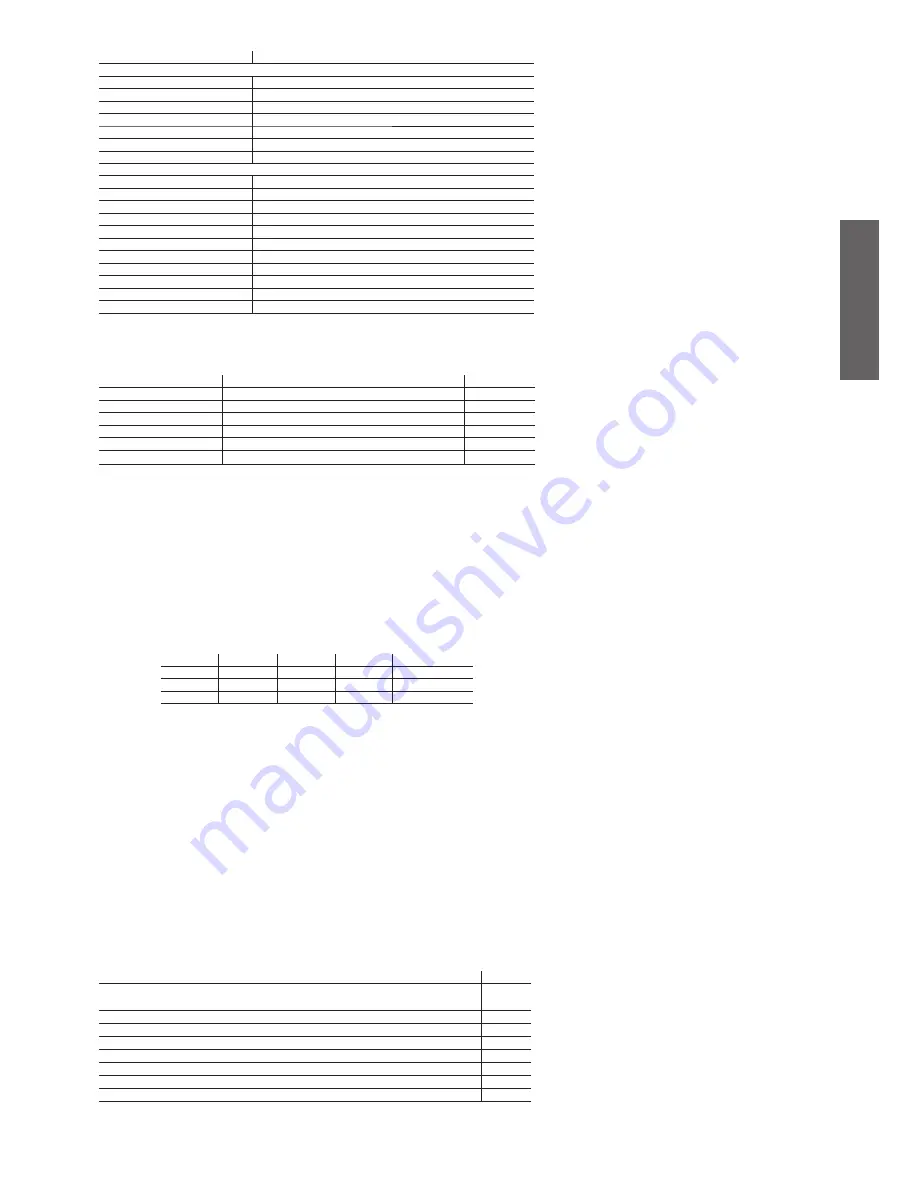
25
ENGL
ISH
EVD
4
+030220227 - rel. 2.1 - 12.06.2008
READ
Parameter name
Description
System measurements (Fig. 3.21)
EEV opening
valve opening as a %
EEV position
calculated electronic expansion valve opening position
Act. SH set
current superheat set point
Superheat
superheat value measured
Ev. probe press.
evaporation pressure value measured by sensor
Ev. probe sat. temp
saturated gas temperature value calculated in the evaporator
Suction temp.
compressor suction temperature value measured by sensor
Digital variables (Fig. 3.21)
Alarm Low SH
active in low superheat conditions
Alarm MOP timeout
active in conditions with excessive evaporation pressure
Alarm LOP timeout
active in conditions with insuffi cient evaporation pressure
EEV not closed
active due to failed valve closing
Low SH status
active when in low superheat control status
MOP status
active when in maximum evaporation pressure control status
LOP status
active when in minimum evaporation pressure control status
Alarm Eeprom err.
active following an EEPROM memory error
Alarm probe err.
active following an error on the signal from the probe
Digital input 1
status of digital input 1
DOUT2
output relay control signal
3.6.3 Communication protocole
The protocol is implemented according to the envisaged specifi cations so that the device belongs to the
BASIC class, with the possibility of setting some parameters (REGULAR class).
Value
Default
Address
From 1 to 247
1
Broadcast
Detect messages with 0
---
Baudrate
4800, 9600, 19200
19200
Parity
None, even, odd
none
Mode
RTU
Interface
RS485
Setting the UNICAST address
The Modbus address can be selected using the “EVD4_UI Address” connection as described in “Ap-
pendix I – Installing and using the EVD4-UI program”, within the envisaged range. Values from 248 to
255 are reserved. If set to one of these values or 0, the FW sets the default value without modifying the
parameter in the E2prom. After setting the new value, the device needs to be switched off and on again
to make it effective.
Setting the BROADCAST address
Broadcast messages (with address 0) can be sent, and will be write-only messages.
The command will be executed, if possible, without any response.
Parity selection mode
The parity is selected using the same program for setting the “EVD4_UI Address”, as described in “Ap-
pendix I – Installing and using the EVD4-UI program”, setting bit 1.2 of parameter CfgProt. Specifi cally:
CfgProt
Bit0
Bit1
Bit2
ModBus parity
1
1
0
0
None
3
1
1
0
Even
5
1
0
1
Odd
If no parity is selected, the number of stop bits will be 2 (default). After setting the new value, the device
needs to be switched off and on again to make it effective.
Modbus messages
The Modbus messages codes are:
01 Read Coil Status
02 Read Input Status
These two messages have the same effect as reading digital variables.
03 Read Holding Registers
04 Read Input Registers
These two messages have the same effect as reading analogue/integer variables.
05 Force Single Coil
06 Preset Single Register
15 Force Multiple Coils
16 Preset Multiple Regs
A maximum number of 8 variables can be written with commands 15 and 16.
17 Report Slave ID
The message is structured as follows, as regards the data part:
Description
Type
ON status Run indicator: 0xFF or 0x00 depending on whether the device is actively control-
ling or not
byte
Peripheral type: high part and low part of the device code
word
Firmware release: high part and low part of the FW release
word
Reserved
word
Hardware release: high part and low part of the HW release
word
Reserved
word
Reserved
word
Reserved
word
Summary of Contents for EVD4
Page 1: ...EVD4 Driver for electronic expansion valve User manual...
Page 2: ......
Page 3: ...User manual...
Page 6: ...6...
Page 44: ...44...
Page 47: ......