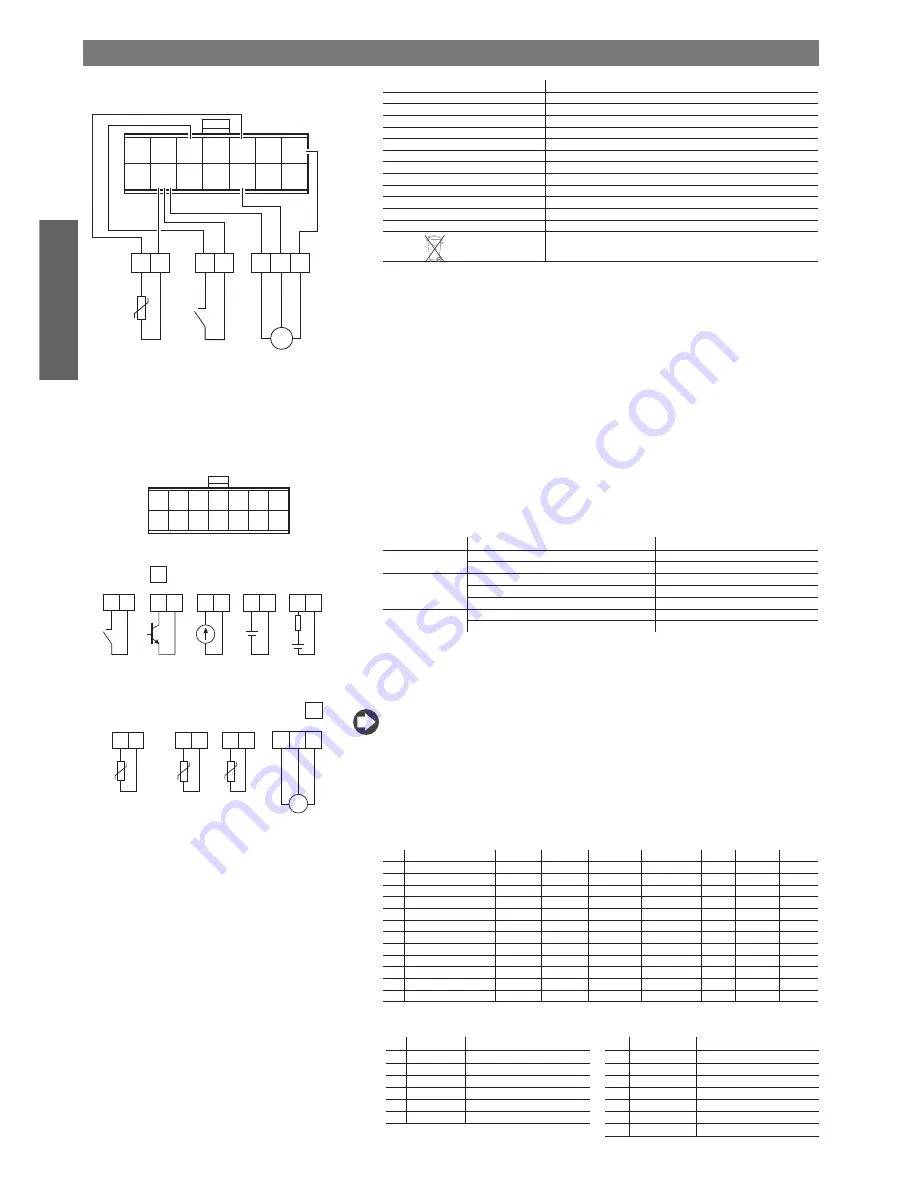
30
G Vbat DI1 S4V S3
S2
S1
G0 GND DI2 S4I Vr1 Vr2 OC
NT
C -5
0T1
05 °C
S3
Temperature
NTC*WF*
Digital input
DI1
GND
GND
DI1
ratio
OUT
Vr1
Ratiometric
pressure SPKT*R*
GND
P
S1
MOLEX
®
Mini-Fit 538-39-01-2140
G Vbat DI1 S4V S3
S2
S1
G0 GND DI2 S4I Vr1 Vr2 OC
NT
C 0T1
50 °C
S2
NTC*HT*
GND
GND
PT1
000
S2
TSQ*
NT
C -5
0T1
05 °C
S1
NTC*WF*
GND
DI2
DI1
GND
GND
4…2
0 mA
S4I
0…1
0 V
S4V
+
GND
10
mA ma
x
10
Vdc ma
x
OC
+
GND
GND
DI2
or
Vr2 S2
S3
or
ratio
OUT
SPKT*R*
GND
P
Fig. 4.1
Fig. 4.2
ENGL
ISH
EVD
4
+030220227 - rel. 2.1 - 12.06.2008
4. TECHNICAL AND CONSTRUCTIONAL SPECIFICATIONS
Installation and storage specifi cations
Operating conditions
-10T60°C, < 90% RH non-condensing
Storage conditions
-20T70°C, < 90% RH non-condensing
Index of protection
IP20
Wire cross-section
0.5 to 2.5 mm
2
Dimensions
70 x 110 x 60
PTI of insulating materials
250 V
Protection against electric shock
to be integrated into class I and/or II equipment
Degree of environmental pollution
normal
Resistance to heat and fi re
category D
Immunity against voltage surges
category 1
Surface temperature limits
as per the operating conditions
Assembly
on DIN rail
Case width
4 modules
Disposal
the module is made up of metal and plastic parts. These must be
disposed of according to the waste disposal local legislation in force
Motor control
The controller works with two-pole stepper motors (Fig. 1). It works with a theoretical sinusoidal wave-
form, in micro-steps and with speeds from 5 to 1000 steps; the current and the control speed effectively
achievable depend on the resistance and the inductance of the motor windings used. If the driver is
connected to a pCO, it receives all the individual operating parameters for the motor from the pCO
controller, if, on the other hand, it is used in stand-alone mode or with the microchiller controller, only
one parameter needs to be set, taken from Table 5, according to the model of motor used (see Table 5).
The controller can manage motors with maximum positions of up to 32000 steps. For connection use
4-wire shielded cables, AWG18/22, max. length 9.5 m. The shield should be connected to the closest
possible earth point in the panel.
Power supply
Power supply: 20 to 28 Vac or 20 to 30 Vdc 50/60 Hz to be protected by external 0.8 A fuse, type T.
Use a class II safety transformer rated to at least 20 VA. Average current input at 24 Vac: 60 mA with the
motor not operating (control logic only); 240 mA with CAREL motor operating (240 mA peak at 18
Ω
).
Emergency power supply: if the optional EVBAT00200/300 module is installed, power supply is
guaranteed to the controller for the time required to close the valve.
Inputs and outputs
Analogue inputs (*)
input
type
CAREL code
S1-S3:
NTC (-50T105 °C)
NTC*WF*
Raziom. (0,5…4,5 Vdc)
SPKT*R*
S2:
NTC (0T150 °C)
NTC*HT*
Raziom. (0,5…4,5 Vdc)
SPKT*R*
Pt1000
TSQ*
S4:
current at 100
Ω
4…20 mA
voltage at 1 k
Ω
0…10 V
Digital inputs ID1 and ID2: controlled by voltage-free contact or transistor, have a no-load voltage of 5 V and
deliver 5 mA short-circuited.
Digital output OC: open-collector transistor; max no-load voltage 10 V, max current 10 mA.
Relay output: normally open contact; 5 A 250 Vac resistive load; 2 A 250 Vac, inductive load (PF= 0.4).
(*) WARNING!
All analogue inputs except for S4 V, the digital I/O and the serial port (not optically-
isolated) refer to the GND earth, (Fig. 3) and consequently the even temporary application of voltages
higher than ±5 V to these connectors may cause irreversible damage to the controller. Input S4 V can
tolerate voltages up to 30 V. As GND is the common earth for all the inputs, this should be replicated
on the terminal block with low-resistance connections for each input used. The GNX earth for the serial
connection is electrically connected to the GND earth. The product complies with Directive 89/336/EEC
(EMC). Contact CAREL if specifi c disturbance occurs in the confi guration used. If the connection to the
motor is made using a shielded cable, the cable shield and the channel marked by the earth symbol on
the 6-pin connector must be earthed as near as possible to the EVD400.
Valve table
n°
Model
Step min Step max
Step close
Step/s speed mA pk mA hold % duty
0
CAREL E2V*
50
480
500
100
450
100
30
1
Sporlan SEI 0.5-20
100
1596
3600
200
200
50
70
2
Sporlan SEI 30
200
3193
3600
200
200
50
70
3
Sporlan SEH 50-250
400
6386
7500
200
200
50
70
4
Alco EX5-EX6
100
750
750
450
400
100
70
5
Alco EX7
250
1600
1600
330
750
250
70
6
Alco EX8 330 step/s
250
2600
2600
330
800
500
70
7
Alco EX8 500 step/s
250
2600
2600
500
800
500
70
8
Danfoss ETS-25/50
200
2625
2700
120
140
75
70
9
Danfoss ETS-100
300
3530
3600
120
140
75
70
10
CAREL E2V*P
50
380
400
100
450
100
30
11
Danfoss ETS-250/400 350
3810
3900
120
140
75
70
Table of refrigerants (consult the electronic expansion valve technical documentation to check
the complete valve-driver system compatibility with the chosen refrigerant)
n° “R” number operating temperature
n°
“R” number
operating temperature
1
R22
-40T60
7
R290
-50T96
2
R134a
-40T60
8
R600
-50T90
3
R404a
-40T60
9
R600a
-50T90
4
R407c
-40T60
10
R717
-60T70
5
R410a
-40T60
11
R744
-50T31
6
R507c
-40T60
12
R728
-201T-145
13
R1270
-60T90
Probe connections (Default)
Other connections
Summary of Contents for EVD4
Page 1: ...EVD4 Driver for electronic expansion valve User manual...
Page 2: ......
Page 3: ...User manual...
Page 6: ...6...
Page 44: ...44...
Page 47: ......