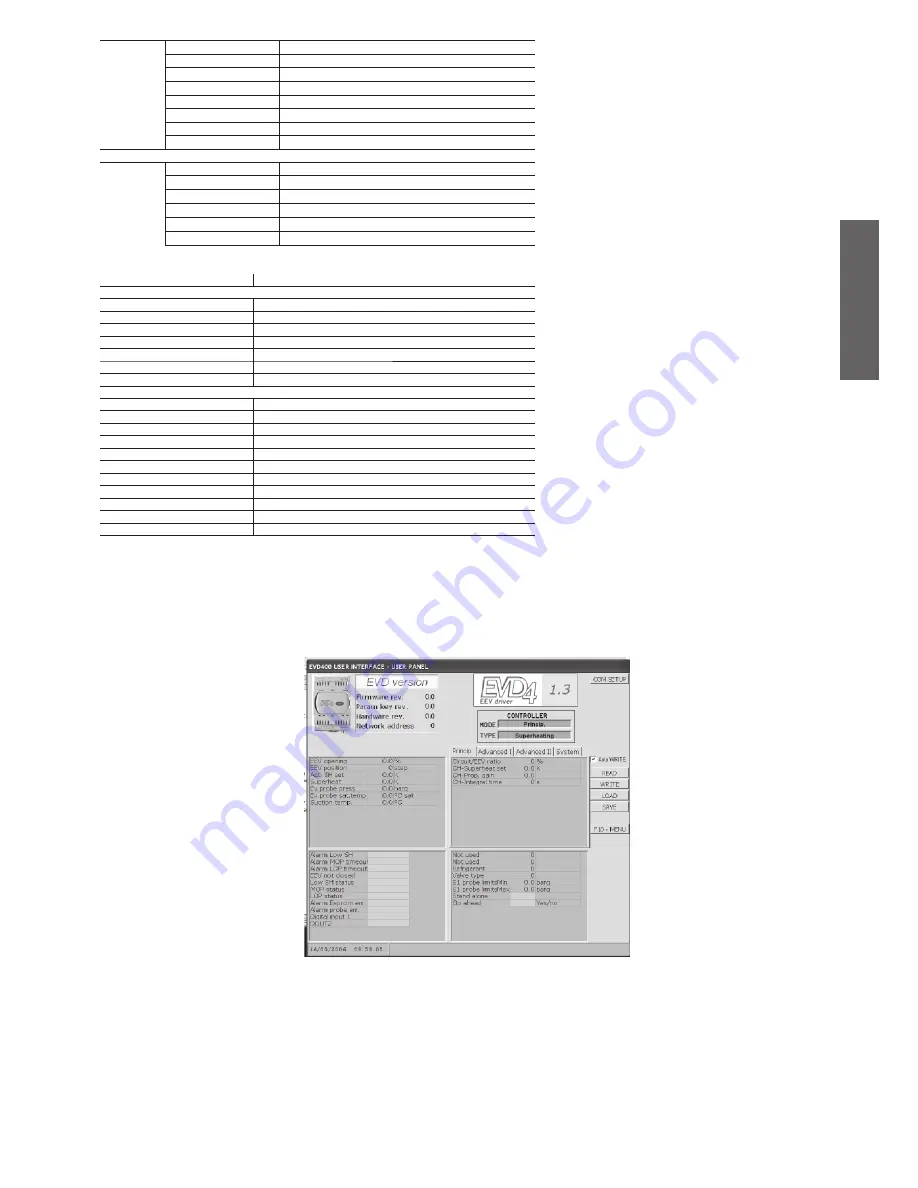
23
Fig. 3.21
ENGL
ISH
EVD
4
+030220227 - rel. 2.1 - 12.06.2008
System
Minimum steps
minimum control steps
—
Maximum steps
maximum control steps
—
Closing steps
steps completed in total closing
—
Standby steps
number of valve standby steps
—
Steprate
motor speed
—
Phase current
peak current per phase
—
Still current
current with the motor off
—
Duty cycle
motor duty cycle
—
Global parameters (Fig. 3.21)
Refrigerant
number indicating the type of refrigerant used
Valve type
number that defi nes the type of electronic valve used
S1 probe limitsMin barg ‘zero’ scale for pressure sensor on input S1
S1 probe limitsMax barg end scale for pressure sensor on input S1
Stand alone
enable StandAlone
Go ahead
enable restart following error
READ
Parameter name
Description
System measurements (Fig. 3.21)
EEV opening
valve opening as a %
EEV position
calculated electronic expansion valve opening position
Act. SH set
current superheat set point
Superheat
superheat value measured
Ev. probe press.
evaporation pressure value measured by sensor
Ev. probe sat. temp
saturated gas temperature value calculated in the evaporator
Suction temp.
compressor suction temperature value measured by sensor
Digital variables (Fig. 3.21)
Alarm Low SH
active in low superheat conditions
Alarm MOP timeout
active in conditions with excessive evaporation pressure
Alarm LOP timeout
active in conditions with insuffi cient evaporation pressure
EEV not closed
active due to failed valve closing
Low SH status
active when in low superheat control status
MOP status
active when in maximum evaporation pressure control status
LOP status
active when in minimum evaporation pressure control status
Alarm Eeprom err.
active following an EEPROM memory error
Alarm probe err.
active following an error on the signal from the probe
Digital input 1
status of digital input 1
DOUT2
output relay control signal
3.5.3 EVD4_UI user interface
The EVD4_UI user interface is based on the CAREL supervisor protocol and is designed for the easy
and intuitive reading or confi guration of the control parameters. The program can be started in different
confi gurations so as to display the set of parameters that is suitable for the type of installation the EVD4
is used in; to do this, make the connection using the name of the required confi guration.
The interface confi guration for the ‘positioner’ function is shown in Fig. 3.21 and is activated by making
the “EVD4_UI stand alone” connection, as described in APPENDIX I “INSTALLING AND USING THE
EVD4_UI PROGRAM”.
3.5.4 Start-up
After having connected the EVD4, as described in 3.5.1, connect the service serial port to a PC via the
special converter and confi gure the parameters and the address using according to the application and/
or systems used. The controller is already enabled; to switch off the EVD4, disable the Stand-alone
variable or modify the status of digital input D1 (Fig. 2.1) and run the supervisor program (i.e. PlantVisor)
to monitor the system.
Summary of Contents for EVD4
Page 1: ...EVD4 Driver for electronic expansion valve User manual...
Page 2: ......
Page 3: ...User manual...
Page 6: ...6...
Page 44: ...44...
Page 47: ......