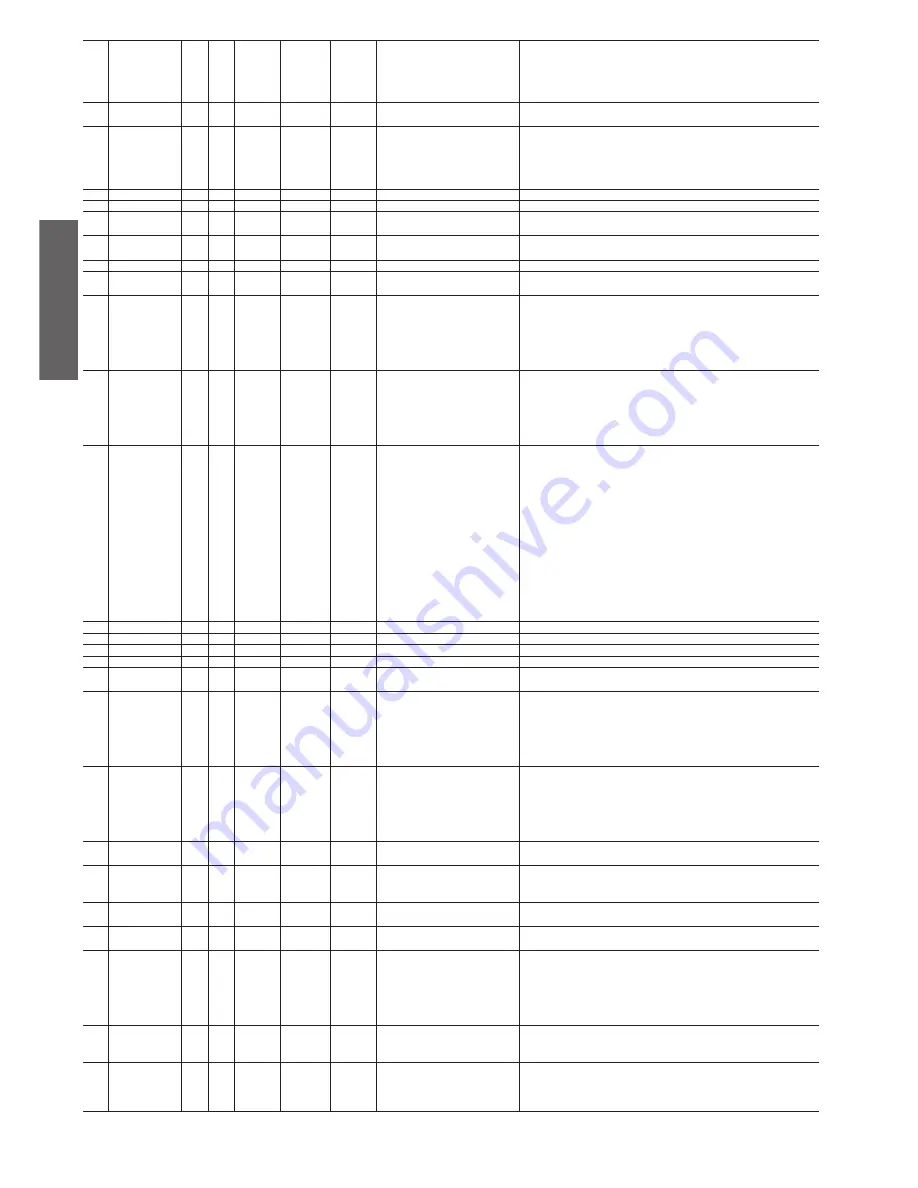
36
ENGL
ISH
EVD
4
+030220227 - rel. 2.1 - 12.06.2008
Dynamic proportio-
nal gain
I
71
0,6
0,6
0,6
attenuation coeffi cient with change in
capacity
Parameter active for each change in capacity of the circuit: when the driver pre-posi-
tions the valve (see CH-Circuit/EEV Ratio, HP-Circuit/EEV Ratio, and DF-Circuit/EEV
Ratio); the difference between the initial and the fi nal position is multiplied by value
of this parameter, between 0 and 1, and the effect of the change in capacity on the
SH is attenuated.
EEV mode man.
D
68
0
0
0
enable/disable manual valve positioning Enables/disables manual valve positioning, eliminating the activation of any control
or alarm
EEV not closed
D
47
0
0
0
active due to failed valve closing
If the EVD400 is installed with a backup battery, in the event of mains power failures
or no communication with the controller for more than 30 sec, the valve is closed.
If during this procedure EVD400 cannot control all the steps to close the valve due
to lack of backup power (fl at battery), when restarting the EEV not closed error is
displayed, with the consequent Go ahead request
EEV opening
A
17
0
0
0
valve opening as a %
Controlled opening of the valve as a %
EEV position
I
15
0
0
0
calculated valve opening position
Calculated opening of the valve, in steps
En. positioner
I
63
enable/disable manual positioner
function
Enables/disables the manual positioner function, from pCO
Enable reset to
default
I
1
0
0
0
enable restore default parameters
If set to 14797, allows the user to reset all the parameters to the default values by
enabling the Reset to default variable
Ev. probe press.
A
14
0
0
0
evaporation pressure value measured
Value measured by the evaporation pressure probe
Ev. probe sat. temp. A
16
0
0
0
saturated gas temperature value calcula-
ted in the evaporator
Saturated gas temperature value calculated in the evaporator, taken from the evapora-
tion pressure on the Mollier chart
Evaporator type
cool
type of evaporator in CH mode
“Identifi es the type of exchanger used as the evaporator in cooling mode:
1 • Plates
2 • Shell&tube
3 • Fast fi nned
4 • Slow fi nned
This section confi gures the integral time in the PID control parameters.”
Evaporator type
heat
type of evaporator in HP mode
“Identifi es the type of exchanger used as the evaporator in heating mode:
1 • Plates
2 • Shell&tube
3 • Fast fi nned
4 • Slow fi nned
This section confi gures the integral time in the PID control parameters.”
EVD probes type
I
69
0
0
0
type of sensors used
“Number that indicates the combination of sensors used to calculate the superheat
value; the default value 51 corresponds to a ratiometric probe connected to S1 and
a 103 AT NTC sensor temperature to S3. For other connections, set the value of the
parameter according to the following formula:
EVD probes type = CFGS1 + 5 * CFGS2 + 25 * CFGS3where:
CFGS1 (probe on channel S1) = 0, 1 or 2
CFGS2 (probe on channel S2) = 0, 1, 3 or 4
CFGS3 (probe on channel S3) = 0, 1 or 2
and:
0 = no measurement
1 = ratiometric pressure
2 = NTC 103AT (10000 ohm at 25 °C)
3 = NTC IHS (50000 ohm at 25 °C)
4 = Pt1000”
EVD type
model of EVD used
Model of EVD used, from pCO
EVD version H.W
I
100
0
0
0
driver hardware version
Driver hardware version
EVD version S.W
I
100
0
0
0
software version installed on the driver
Software version installed on the driver
Force
D
8
0
0
0
send a FORCE command to the EVD
Transmission of all the parameters or variables
Functional test
D
2
0
0
0
functional test
The functional test is a status of the driver that is used to check the operation of the
device, and in particular to calibrate a number of variables
Go ahead
D
35
0
0
0
enable restart following error
“When the driver signals one of the following errors:
- Probe error alarm
- EEPROM error alarm
- EEV not closed
authorisation is requested continue after the user has checked the existence and the
seriousness of the problem.”
Heat
type of evaporator in HP mode
“Identifi es the type of exchanger used as the evaporator in heating mode:
1 • Plates
2 • Shell&tube
3 • Fast fi nned
4 • Slow fi nned
This section confi gures the integral time in the PID control parameters.“
Hi TCond. int. time A
36
0
0
0
integral time for high condensing
temperature control (HiTcond)
Integral time for high condensing temperature control, see Hi TCond. protection
Hi TCond.
protection
A
40
80
80
80
maximum condensing temperature
Maximum condensing temperature; once exceeded, the driver starts controlling
the valve position based on this set point and considering the Hi TCond. int. Time
parameter
High superheat
alarm threshold
A
37
200
200
200
maximum superheat temperature
Maximum superheat temperature. If HP and DF modes are also available, this refers
to control in CH mode
High Tc status
D
53
0
0
0
active when in high condensing tempe-
rature control status
Active when in high condensing temperature control mode, see Hi TCond. protection
HP-Circuit/EEV
Ratio
I
20
percentage of the maximum capacity
managed by the valve in HP mode,
from pCO
This is the ratio between the maximum cooling capacity delivered by the valve and
the maximum in the circuit, in HP mode. Used to pre-position the valve when starting
and changing capacity, sent by the pCO or µC
2
controller (e.g. if the capacity of the
system changes to 50%, the pCO or µC
2
tells the driver to preposition the valve at
50% of its total travel, minus the Dynamic proportional gain factor, then the driver will
commence independent SH control), from pCO or µC
2
.
HP-Integral time
A
29
35
35
200
integral time for superheat control in
HP mode
This is the time of the PID integration action for operation in HP mode, increasing
the value the SH reaches the set point more slowly but avoids excessive swings. This
depends on the type of evaporator and the inertia of the circuit.
HP-Low Superheat
A
44
3
3
6
low superheat value in HP mode
This is the minimum SH value below which the system activates the Alarm Low
Superheat after the Alarms delay Low SH in the operation in HP mode. This is used to
avoid an excessively low pressure difference between the condenser and evaporator
circuits, which may cause liquid at the compressor intake.
Summary of Contents for EVD4
Page 1: ...EVD4 Driver for electronic expansion valve User manual...
Page 2: ......
Page 3: ...User manual...
Page 6: ...6...
Page 44: ...44...
Page 47: ......