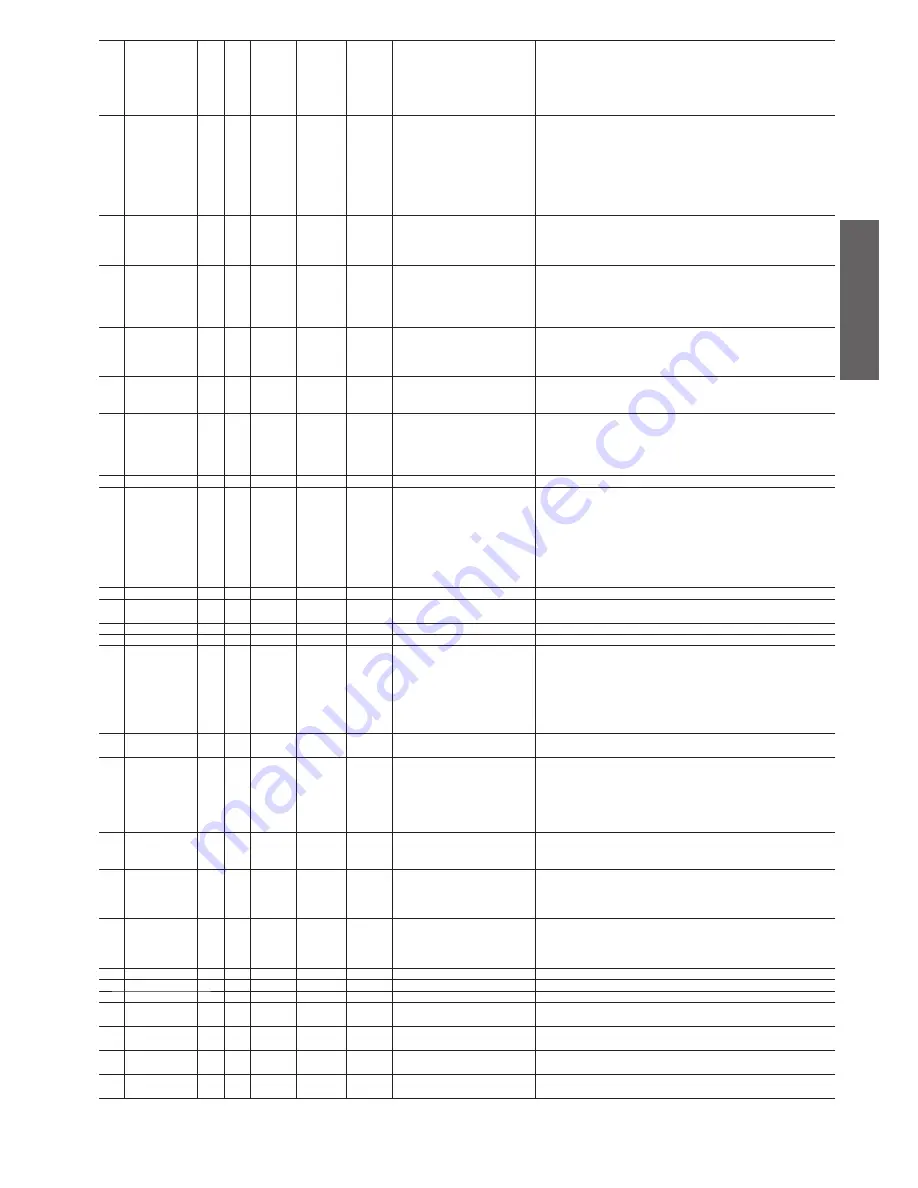
35
ENGL
ISH
EVD
4
+030220227 - rel. 2.1 - 12.06.2008
Capacity control
EVD
4
macroblock parameter that defi nes
the type of compressor control
“According to the type of compressor control selected, the macroblock calculates the
proportional factor, which will be entered indiscriminately for the parameters CH-
Proportional gain, HP-Proportional gain and DF-Proportional gain. Multiple choice:
- “”none or stages”” if the compressor is without capacity control or with step control
- “”continuous slow”” for screw compressors with slider control
- “”continuous fast”” for compressors with inverter control”
CH-Circuit/EEV
Ratio
I
20
percentage of the maximum capacity
managed by the valve
This is the ratio between the maximum cooling capacity delivered by the valve and
the maximum in the circuit, in cooling or CH mode, if managed. Used to pre-position
the valve when starting and/or changing capacity (if possible), sent by the pCO or
µC
2
controller (e.g. if the ratio is 40% and if the capacity of the system changes to
1/2 of the current level, the pCO or µC
2
tells the driver to preposition the valve at half
of 40%, that is, equal to 20% of the total capacity of the valve, minus the Dynamic
proportional gain factor), once the driver has completed pre-positioning, independent
SH control will commence
CH-Integral time
A
28
30
30
80
integral time for superheat control
This is the time of the PID integration action, increasing the value the SH reaches
the set point more slowly but avoids excessive swings. This depends on the type of
evaporator and the inertia of the circuit. If HP and DF modes are also available, this
refers to control in CH mode
CH-Low Superheat A
43
2,5
2,5
6
low superheat value
This is the minimum SH value below which the system activates the Alarm Low Supe-
rheat after the Alarms delay Low SH. This is used to avoid an excessively low pressure
difference between the condenser and evaporator circuits, which may cause liquid at
the compressor intake. If HP and DF modes are also available, this refers to control in
CH mode
CH-Proportional
gain
A
25
3
2,5
7
PID proportional factor
This is the PID proportional factor, increasing the value increases the reactivity of the valve and
therefore of SH control, however for high values control may become unstable. This depends
on the ratio between circuit capacity and valve capacity and on the maximum number of valve
control steps. If HP and DF modes are also available, this refers to control in CH mode
CH-Superheat set
A
22
6
6
10
superheat set point
Superheat set point. If HP and DF modes are also available, this refers to control in CH
mode. Do not set excessively low values (less than 5°C) or too near the low superheat
limit (at least 3°C difference).
Closing extra steps
I
63
enable extra steps in closing
Enables the extra steps function when closing: when the driver closes the valve but
the SH value measured is not coherent (too low), the driver realises that the valve is
not completely closed and forces some extra closing steps at preset intervals, until the
SH reaches coherent values. Maximum steps/128 are completed every second. Used
by pCO.
Closing steps
I
24
500
500
500
steps completed in total closing
Number of steps that the driver uses to totally close the valve (not during control)
Compressor or unit
macroblock parameter that defi nes the
integral time
“Identifi es the type of unit/compressor that the expansion valve is used on.
This selection optimises the PID control parameters and the auxiliary Driver protectors,
considering the control characteristics of the various types of system.
1 Reciprocating
2 Screw
3 Scroll
4 Flooded cabinet
5 Cabinet“
Cond. probe press. A
12
0
0
0
condensing pressure value measured
Condensing pressure value measured, from µC
2
or pCO
Cond. probe sat.
temp.
A
9
0
0
0
saturated gas temperature in the
condenser
Saturated gas temperature value calculated in the condenser, from µC
2
or pCO
STEPCOUNTH
I
95
0
0
0
step counter high word
Step counter in hexadecimal format, high part
STEPCOUNTL
I
94
0
0
0
step counter low word
Step counter in hexadecimal format, low part
Cool
macroblock parameter that defi nes the
integral time
“Identifi es the type of exchanger used as the evaporator in cooling mode:
1 Plates
2 Shell&tube
3 Fast fi nned
4 Slow fi nned
This selection optimises the PID control parameters and the auxiliary Driver protectors,
considering the control characteristics of the various types of system.“
Derivative time
A
31
1
1
1
PID derivative time
This is the time of the PID derivative action, increasing the value decreases swings but
bring fl uctuations vibrations around the SH set point.
DF-Circuit/EEV Ratio I
20
percentage of the maximum capacity
managed by the valve in DF mode,
from pCO
This is the ratio between the maximum cooling capacity delivered by the valve and
the maximum in the circuit, in DF mode. Used to pre-position the valve when starting
and changing capacity, sent by the pCO or µC
2
controller (e.g. if the capacity of the
system changes to 50%, the pCO or µC
2
tells the driver to preposition the valve at
50% of its total travel, minus the Dynamic proportional gain factor, then the driver will
commence independent SH control), from pCO or µC
2
.
DF-Integral time
A
30
30
30
30
integral time for superheat control in
DF mode
This is the time of the PID integration action in the operation in DF mode, increasing
the value the SH reaches the set point more slowly but avoids excessive swings. This
depends on the type of evaporator and the inertia of the circuit.
DF-Low Superheat
A
45
4
4
4
low superheat value in DF mode
This is the minimum SH value below which the system activates the Alarm Low
Superheat after the Alarms delay Low SH in the operation in DF mode. This is used to
avoid an excessively low pressure difference between the condenser and evaporator
circuits, which may cause liquid at the compressor intake.
DF-Proportional
gain
A
27
4
4
4
PID proportional factor in DF mode
This is the PID proportional factor per operation in DF mode, increasing the value in-
creases the reactivity of the valve and therefore of SH control, however for high values
control may become unstable. This depends on the ratio between circuit capacity and
valve capacity and on the maximum number of valve control steps.
DF-Superheat set
A
24
10
10
10
superheat set point in DF mode
Superheat set point in operation DF
Digital input 1
D
17
0
0
0
status of digital input 1
Checks the status of digital input 1 (enabled or disabled)
Digital input 2
D
18
0
0
0
status of digital input 2
Checks the status of digital input 2 (enabled or disabled)
DOUT2
D
21
0
0
0
relay output control
Variable that checks and/or signals the opening or closing of the relay, 0 = open, 1 =
closed
Driver X high
superheat
driver X with high superheat
EVD200 alarm, driver X with high superheat, checks the sensors on driver X
DriverX mode
operating mode of the X-th driver
Operating mode of the X-th driver (CH, HP, DF), from pCO
Duty cycle
I
29
30
30
30
motor duty cycle
Duration of the control signal sent by the driver to the valve in one second, as a
percentage (100% = continuous signal)
Summary of Contents for EVD4
Page 1: ...EVD4 Driver for electronic expansion valve User manual...
Page 2: ......
Page 3: ...User manual...
Page 6: ...6...
Page 44: ...44...
Page 47: ......