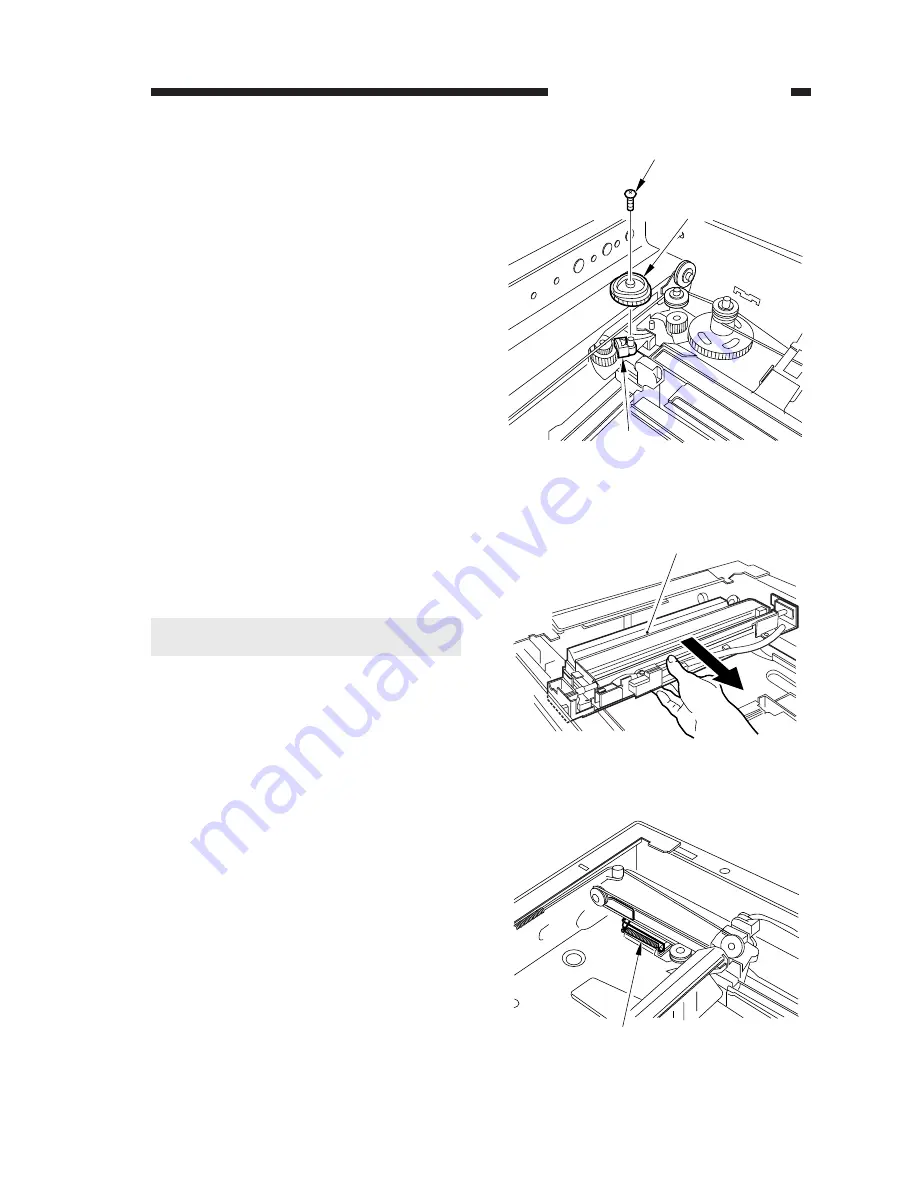
CHAPTER 3 EXPOSURE SYSTEM
COPYRIGHT © 1999 CANON INC. CANON PC800s/900s REV.0 AUG. 1999 PRINTED IN JAPAN (IMPRIME AU JAPON)
3-33
Figure 3-341
Figure 3-339
Figure 3-340
[7]
[8]
[6]
[9]
[10]
7) Remove the screw [7], and detach the cam
gear [6] and the cable retainer [8].
8) Holding the middle of the No. 1 mirror
mount [9], move it to the center of the
machine.
Caution:
Do not hold the reflecting plate.
9) Remove the spring [10].
Summary of Contents for PC920
Page 12: ......
Page 34: ......
Page 36: ......
Page 48: ......
Page 50: ......
Page 92: ......
Page 94: ......
Page 122: ......
Page 124: ......
Page 162: ......
Page 164: ......
Page 180: ......
Page 206: ......
Page 240: ......
Page 242: ......
Page 256: ......
Page 263: ......
Page 265: ......
Page 355: ......
Page 383: ......