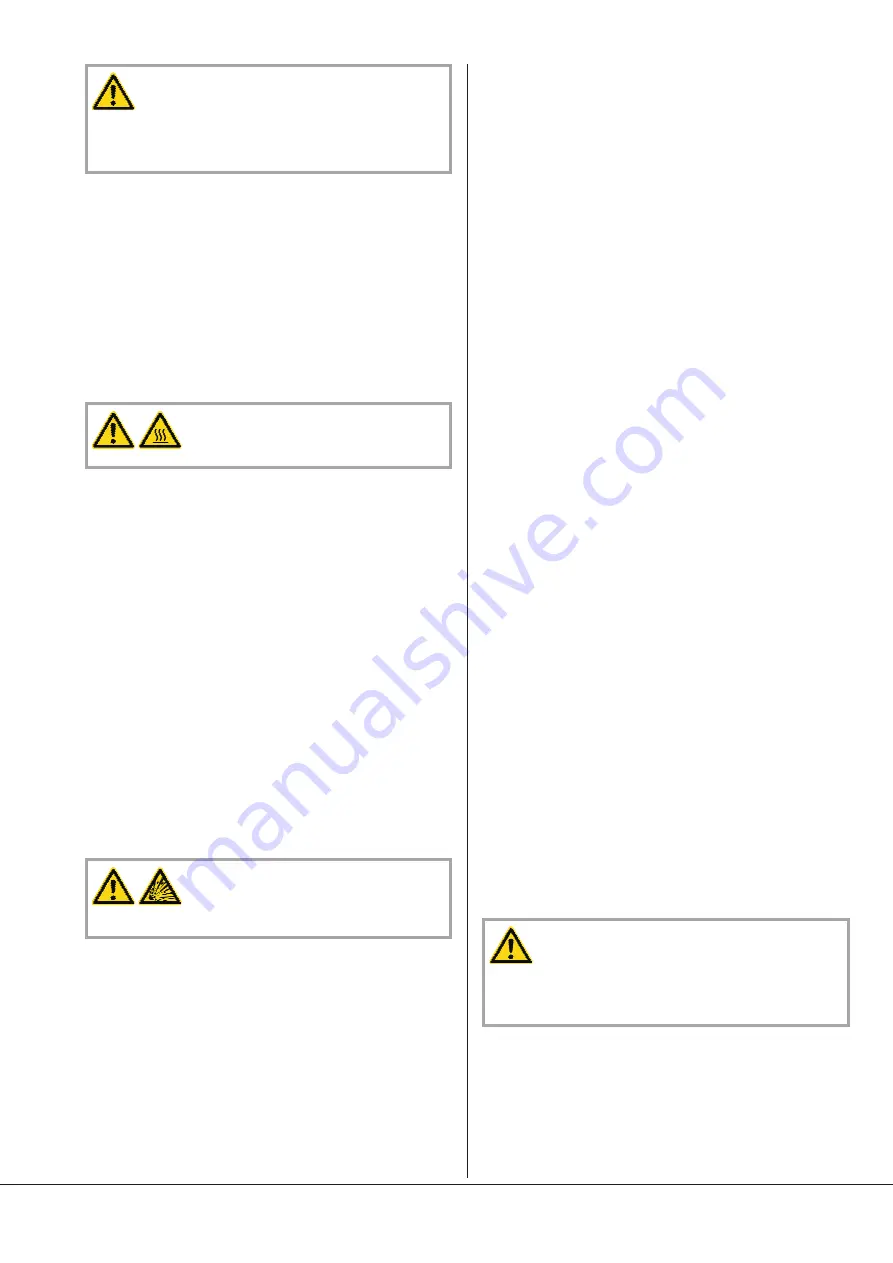
CAUTION
The vacuum pump cannot run for more than 1 minute without
injection liquid. The outlet gas temperature measured by the
TSA+/0102 sensor must never exceed the trip value determined in
the “COBRA ATEX catalogue”.
Before starting any maintenance work, make sure that the vacuum
pump has been fully switched off and that it cannot accidentally be
switched on again. Follow the shutdown procedure in the section
“Stopping procedure for maintenance”:
l
Close the injection of cooling liquid (INJ) in the cylinder
u
Let the vacuum pump run for 1 minute
l
Stop the vacuum pump
l
Close the cooling liquid supply (CL)
l
Switch off the power supply (the vacuum pump must be fully dis-
connected from the power supply)
l
Put up label or warning board “Maintenance in progress” on or
next to the pump
CAUTION
The oil temperature can reach a value of 60°C!
l
Make sure that the oil circuit and the cooling liquid circuit have
been drained before moving the vacuum pump
l
Make sure that any cleaning materials used to clean the vacuum
pumps have been disposed of according to local and national regu-
lations
Before disconnecting the different connections, make sure that the inlet
and exhaust lines of the vacuum pump have been brought to
atmospheric pressure
When the maintenance work has been finished, follow the procedure
“Start-up procedure after maintenance”:
l
Remove the label or warning board “Maintenance in progress”
l
Check the cooling liquid level according to chapters “Checking the
oil level”
l
Connect the pump up to the power supply
l
Make sure that the “Installation Prerequisites” are followed
l
Open the cooling liquid supply, adjust the flow rate
l
Start the vacuum pump
l
Open the injection of cooling liquid in the cylinder, adjust the flow
rate
Maintenance program
WARNING
Opening the vacuum pump is only authorised after it has stopped,
and in absence of explosive atmospheres.
NOTE
: The maintenance intervals depend on the individual operating
conditions. The intervals given below should be considered as initial
guidelines which should be shortened or extended as appropriate. In
particularly heavy duty operation such as high dust loads in the
environment or in the process gas, it can become necessary to shorten
the maintenance intervals significantly.
Weekly:
l
Check the vacuum pump for oil leaks (condensate drain plug (CD))
- in case of leaks, have the vacuum pump repaired (Busch service)
l
Check the vacuum pump for cooling liquid leaks - in case of leaks,
have the vacuum pump repaired (Busch service)
In case of operation in a dusty environment:
u
Check the motor hood for dirt, if necessary clean
Monthly:
l
Check the oil level (see “Checking the Oil”)
l
Check the different cooling liquid flow rates
In case of operation in a dusty environment:
u
Make sure that the operating room is clean and free of dust;
clean the room if necessary
l
Make sure that the vacuum pump has been switched off and that
it cannot accidentally be switched on again
u
Check the electrical connections
u
Carry out a visual inspection of the vacuum pump
In case of operation in a clean environment:
u
Check the motor hood for dirt, if necessary clean
Yearly:
l
Make sure that the vacuum pump has been switched off and that
it cannot accidentally be switched on again
l
Drain and fill in used oil (see “Draining the Oil” and “Filling in new
oil")
l
Check the operation and condition of the intermediate chamber
ventilation assembly none return valve and filter/ silencer, clean or
replace as necessary
If the inlet is equipped with a mesh screen:
u
Check the mesh screen at the inlet and clean it if necessary
Every 5000 operating hours:
l
Check the cooling liquid lines
l
Drain and fill in new oil (see “Draining the Oil” and “Filling in new
oil”)
Every 8000 operating hours:
l
Check the trouble-free operation of all electric devices fitted to the
pump
NOTE :
This maintenance procedure is not obligatory if the vacuum
pump is not used for drawing explosive gases or vapours. However, it
can be carried out if the operator believes it to be necessary.
Every 10’000 operating hours:
l
Drain and fill in used oil (see “Draining the Oil” and “Filling in new
oil")
l
Check the seals and replace them if necessary
l
Check the inlet and discharge lines and clean or replace them if ne-
cessary
Every 16’000 operating hours, at the latest
after 4 Years:
Have a major overhaul done on the vacuum pump (Busch service)
Stopping procedure for maintenance
CAUTION
The vacuum pump cannot run for more than 1 minute without in-
jection liquid. The outlet gas temperature measured by the
TSA+/0102 sensor must never exceed the trip value determined in
the “COBRA ATEX catalogue”.
l
Close the injection of cooling liquid (INJ) in the cylinder
u
Let the vacuum pump run for 1 minute
l
Stop the vacuum pump
l
Close the cooling liquid supply (CL)
l
Switch off the power supply (the vacuum pump must be discon-
nected from the power supply)
Maintenance
Page 15
Summary of Contents for COBRA AC 1000 F
Page 26: ...Note...
Page 27: ...Note...