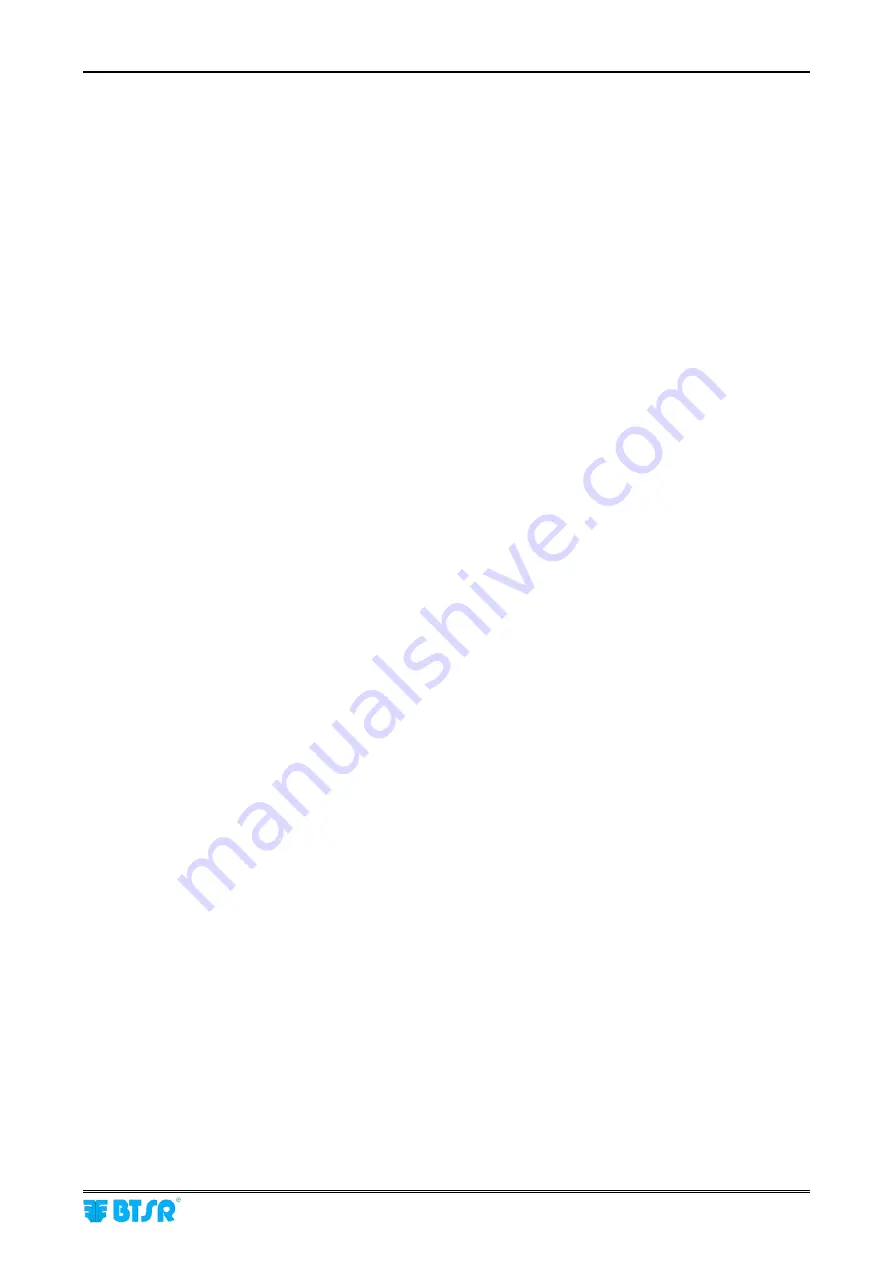
IS3x/TTS Sensor Features
SMART MATRIX TWIST
- 3-6 -
Touch Light Function
Failure Reset
:
When the sensor is in Failure Status
(Red Led blinking)
by skimming the touch light you
reset the failure and, after the programmed
Delay-Control
time, the sensor resumes the
control.
Numbering
:
When the sensor is in Numbering Status
(Green Led blinking)
, by skimming the touch
light, you give the sensor the identification number shown in
Config
→
Identify
.
Activation/
De-Activation
:
When the sensor is either in
Control
or
Delay-Control
phase, by skimming the touch
light you will either deactivate or re-activate the sensor itself.
This function can be either enabled or disabled using parameter LOCK-UNLOCK.
Sensor –System Interface
The sensor communicates with the SM-DIN TWIST Board and with the textile machine through the following
signals:
TX-RX:
Is the bi-directional communication line between sensor and SM-DIN TWIST Board, used for
sensor operation parameters programming, for sensor’s test and for all the other real-time
communications between sensor and Board.
STOP Output:
The STOP signal is an OPEN COLLECTOR Output through which the IS3x/TTS sensor
signals the yarn control status
(number of twisting within the minimum-maximum
programmed range or number of twisting higher than the maximum threshold or lower than
the minimum threshold)
.
The STOP Output can be configured as a Normally Open
(NO)
or Normally Closed
(NC)
signal and, in addition, it can be configured either as Continuous signal
(CONT)
or as a 2
seconds Pulse signal
(PULSE 2S)
or 10 seconds Pulse signal
(PULSE 10S)
.
Electrical Characteristics of STOP Signal
Protected against short circuit
Max DC current at collector: 200 mA
Max peak current at collector: 500 mA
Vce = 1,2V with I_collector = 500 mA
Summary of Contents for SMART MATRIX TWIST
Page 1: ...SMART MATRIX TWIST Operating Manual ENGLISH Rev 1 2 January 2012 ...
Page 3: ...Introduction i ...
Page 4: ......
Page 8: ...Table of Contents SMART MATRIX TWIST iv Page intentionally left blank ...
Page 9: ...Connections and Electrical Interface 1 ...
Page 10: ......
Page 25: ...Operating Instructions 2 ...
Page 26: ......
Page 67: ...System Components 3 ...
Page 68: ......