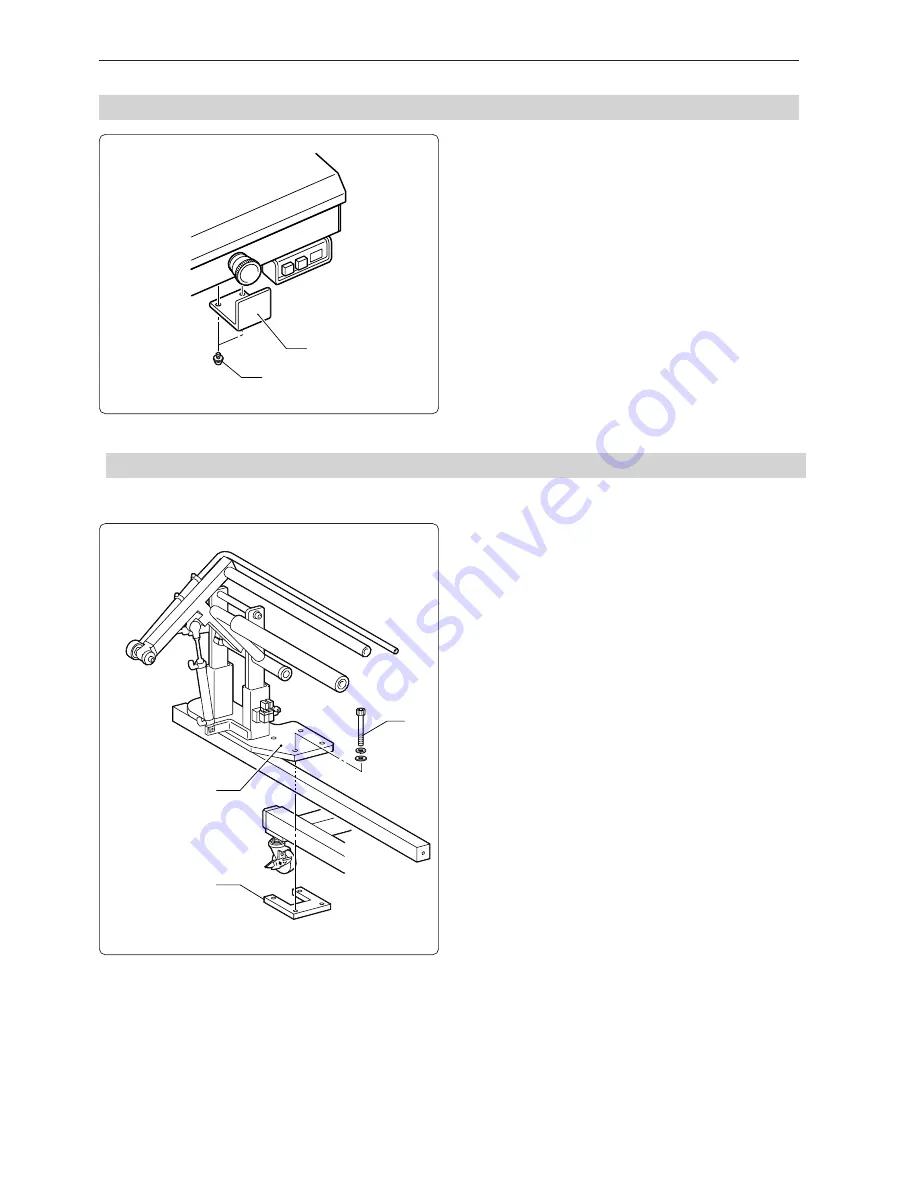
Chapter 1 Machine Preparation
BAS-6150
14
3-6. Attachment of the stacker (option)
■
How to attach
1.
Set tap plate
q
at the bottom and the
stacker base
w
at the top of the leg. Fix
them with four bolts
e
respectively.
e
w
q
3-5. Detachment of the emergency stop switch cover
Unscrew two tightening screws
q
and
detach emergency stop switch cover
w
.
Attach the emergency stop switch cover to protect the emer-
gency stop switch. Keep the emergency stop switch cover with
good care.
OF
F
O N
OF
F
O N
w
q
1440S
1441S
Summary of Contents for BAS-6150
Page 2: ......
Page 11: ...Chapter 1 Machine Preparation ...
Page 29: ...Chapter 2 Sewing flow ...
Page 41: ...Chapter 3 Settings ...
Page 55: ...Chapter 4 Oiling ...
Page 59: ...Chapter 5 Adjustment For raising the head refer to 3 How to raisethehead in Chapter4 Oiling ...
Page 70: ...Chapter 5 Adjustment BAS 6150 68 ...
Page 71: ...Chapter 6 Knife replacement ...
Page 77: ...Chapter 7 Environment setting ...
Page 85: ...Chapter 7 Environment setting BAS 6150 83 Standard stacker 4 steps 0 1 3 4 2 1530S ...
Page 95: ...Chapter 8 Dipswitch ...
Page 98: ...Chapter 8 Dipswitch BAS 6150 96 ...
Page 99: ...Chapter 9 Error code List ...
Page 103: ...Chapter 10 Troubleshooting ...