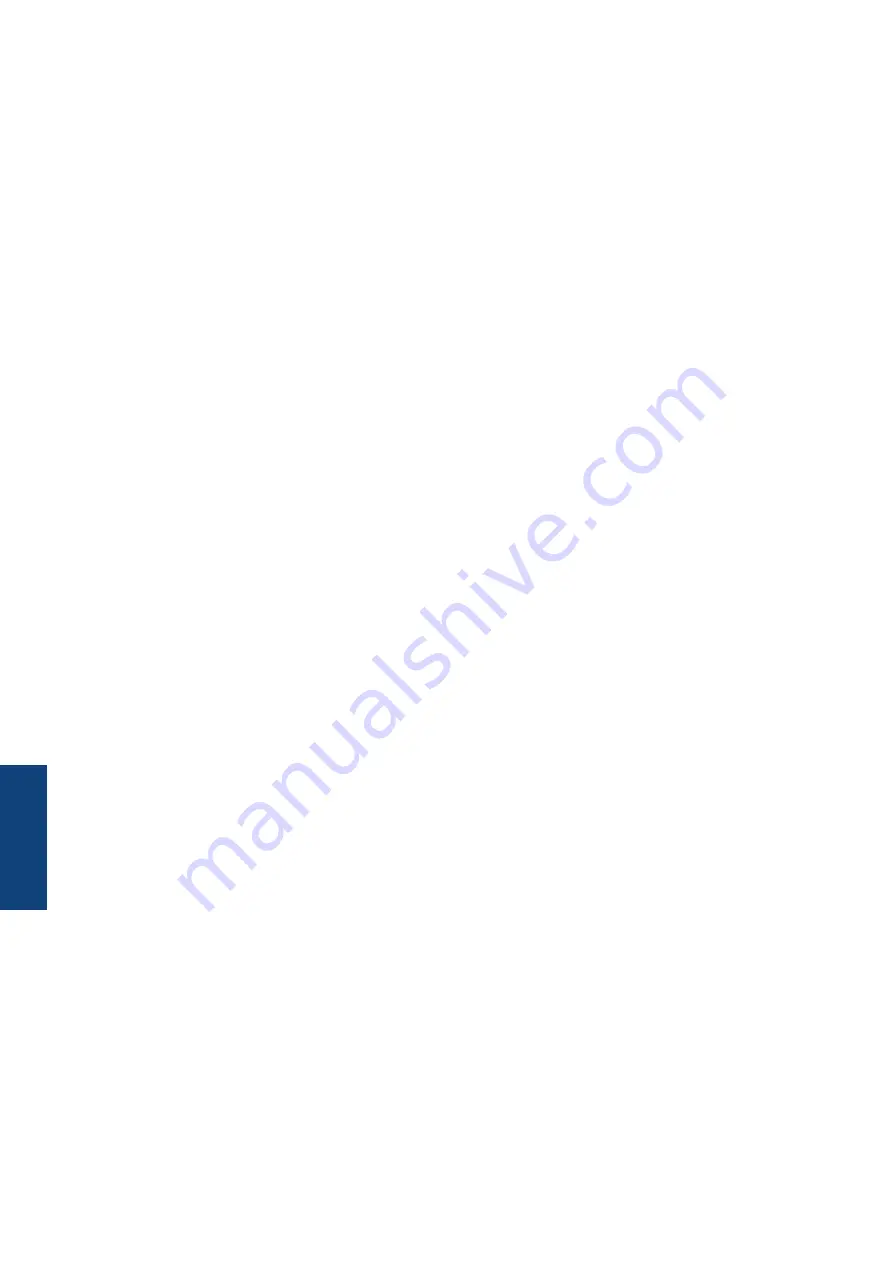
34
MAI
N
TE
NAN
C
E
&
I
N
S
P
EC
TI
ON
Category I
This category involves observing
the equipment during operation for
indications of inadequate performance.
When in use, equipment shall be
visually inspected on a daily basis
for cracks, loose fits or connections,
elongation of part, and other signs of
wear, corrosion or overloading. Any
parts found to show cracks, excessive
wear, etc., shall be removed from
service for further examination.
The equipment shall be visually
inspected by a person knowledgeable
in that equipment and its function.
Category II
This is Category I inspection plus
further inspection for corrosion,
deformation, loose or missing
components, deterioration, proper
lubrication, visible external cracks, and
adjustment.
Category II may involve some
disassembly to access specific
components and to identify wear that
exceeds the allowable tolerances.
Category III
This is Category II inspection plus
further inspection, which should include
NDT of critical areas and may involve
some disassembly to access specific
components and to identify wear that
exceeds the allowable tolerances.
Prior to inspection, all foreign material
such as dirt, paint, grease, oil, scale,
etc. shall be removed from the
concerned parts by a suitable method
(e.g. paint-stripping, steam-cleaning,
grit-blasting).
Category IV
This is Category III inspection plus
further inspection for which the
equipment is disassembled to the
extent necessary to conduct NDT of all
primary-load-carrying components.
Equipment shall be:
•
disassembled in a suitable-
equipped facility to the extent
necessary to permit full
inspection of all primary-load-
carrying components and other
components that are critical to the
equipment.
•
inspected for excessive wear,
cracks, flaws and deformation.
Procedure:
•
Corrections shall be made
in accordance with the
manufacturer’s recommendations.
•
Prior to inspection, all foreign
material such as dirt, paint, grease,
oil, scale, etc. shall be removed
from the concerned parts by
a suitable method (e.g. paint-
stripping, steam-cleaning, grit-
blasting)
Frequency
Periodic inspection
The recommended schedule for
inspection of all kind of Elevators is as
follows:
Ongoing: I
Daily:
II
6 Monthly:
III
1 Year:
IV
The recommended frequencies apply
for equipment in use during the
specified period.
The inspection frequencies are only
recommendations. The schedule of
inspection heavily depends on the
following factors:
•
environment
•
load cycles
•
regulatory requirements
•
operating time
•
testing
•
repairs
•
re manufacture
Non-periodic inspection
A complete, on-job, shut-down
inspection equivalent to the periodical
Category III or Category IV should be
made before (if anticipated) and after
critical jobs (e.g., running heavy casing
/ drill strings, jarring, pulling on stuck
pipes and/or operating at extreme low
temperatures) <-20° C (<-4° F).
Inspection
A thorough inspection should be carried
out periodically (every 3 months)
or as special circumstances may
require. Before starting an inspection
disconnect hydraulic/pneumatic system
and remove all foreign materials (dirt,
paint, grease Oil, scale, etc.) from
surface by a suitable method. After a
field inspection, it is advisable to record
the extent of testing and testing results.
Conduct the periodic or critical load
inspection in the field by the crew with
the supervisor.
If cracks, excessive wear etc. is
recognized, contact Blohm + Voss
Oil Tools or an authorized service
company.
Inspection categories acc. to API RP 8B
Summary of Contents for 613000-Y-H-F
Page 8: ...8 ...
Page 9: ...9 DESCRIPTION DESCRIPTION ...
Page 16: ...16 DESCRIPTION ...
Page 17: ...17 COMMISIONINGS COMMISIONING COMMISSIONING ...
Page 20: ...20 COMMISIONINGS ...
Page 21: ...21 INSTALLATION INSTALLATION ...
Page 27: ...27 OPERATIONS OPERATIONS ...
Page 29: ...29 MAINTENANCE INSPECTION MAINTENANCE INSPECTION ...
Page 43: ...43 SIZE COMPONENTS SIZE COMPONENTS ...
Page 46: ...46 ...
Page 47: ...47 DRAWINGS SPARE PARTS DRAWINGS SPARE PARTS ...
Page 51: ...51 DRAWINGS SPARE PARTS PN 613040 Mechanic Kit D 29 31 D 2 5 31 31 18 3 ...
Page 52: ...52 DRAWINGS SPARE PARTS 570 9 27 7 21 11 4 25 8 1 28 6 22 5 131 87 238 85 23 5 ...
Page 53: ...53 DRAWINGS SPARE PARTS 25 12 25 26 9 24 19 10 30 50 18 23 C 1 2 16 17 13 14 15 ...
Page 62: ...62 DRAWINGS SPARE PARTS ...