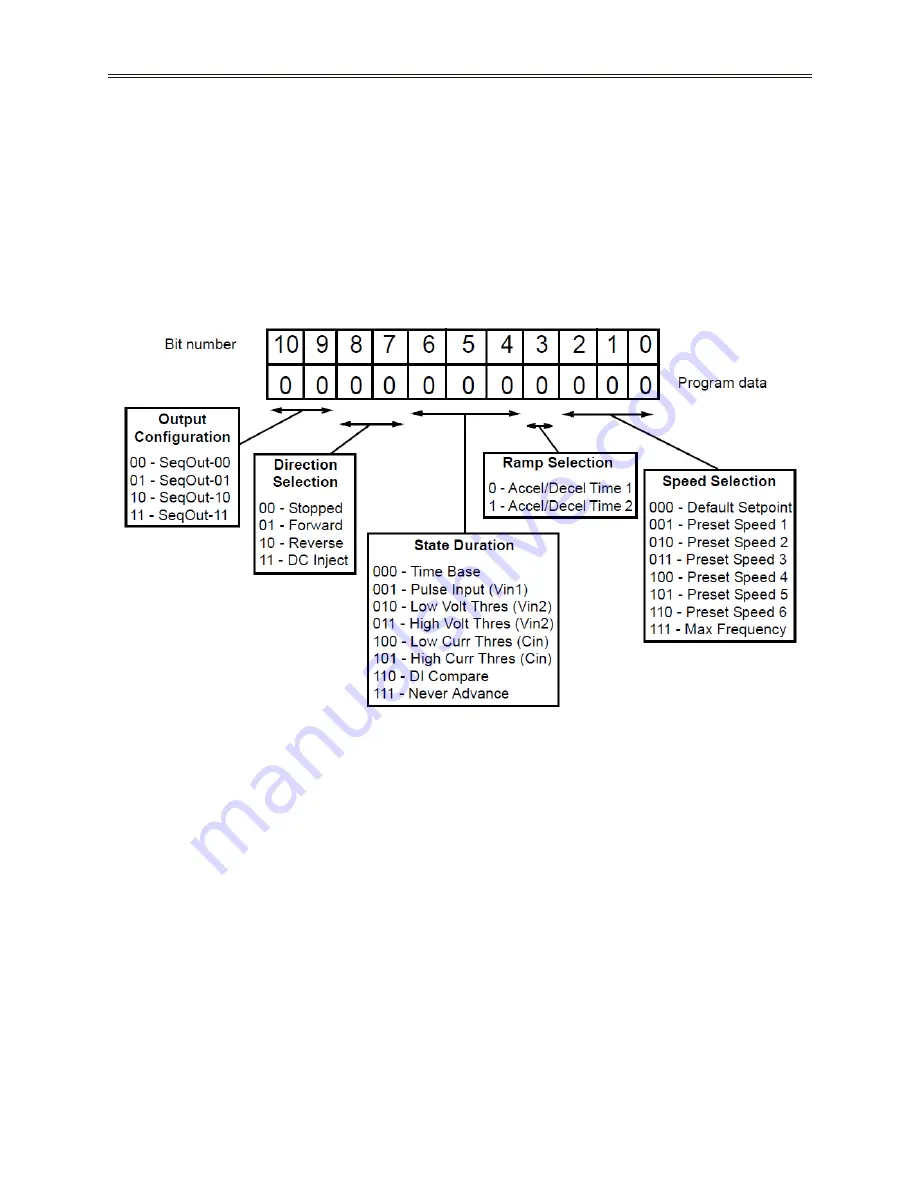
136
7 - PARAMETER DESCRIPTION
These five characteristics are configured by two parameters for each state. These parameters are named
“Seq Cntl X” and Seq Count X,” where X represents the state number of the sequencer (1-9). The “Seq
Cntl X” parameter is a binary parameter that sets each of the five characteristics listed above. “Seq Count
X” uses bits 4,5,6 and configures the threshold that the sequencer will use in determining when to advance
to the next stage by the method programmed in the control parameter. The descriptions for “Seq Count X”
is under the title “Description of Seq Count Function”. The bit patterns of the “Seq Cntl X” parameters are
shown below.
S4 Sequencer Speed Selection (Bits 0, 1, 2)
The table below gives more information on the speed selection options available in the S4 sequencer by
programming bits 0, 1 and 2 of each state’s control parameter. The options include any Preset Speed, Max
Frequency, or allowing the reference to be determined in the normal S4 control path.
S4 Seq Cntl Parameter: Bit Definition
Summary of Contents for RSi S4 Series
Page 4: ......
Page 9: ...1 1 Introduction...
Page 16: ...8 1 INTRODUCTION NOTES...
Page 17: ...9 2 Technical Specifications...
Page 28: ...20 2 TECHNICAL SPECIFICATIONS NOTES...
Page 29: ...21 3 Installation...
Page 37: ...29 4 Connections...
Page 51: ...43 4 CONNECTIONS 4 5 2 S4 Wiring Diagram S4 Series Wiring Diagram...
Page 56: ...48 4 CONNECTIONS NOTES...
Page 57: ...49 5 Keypad Operation and Programming...
Page 70: ...62 NOTES 5 KEYPAD OPERATION AND PROGRAMMING...
Page 71: ...63 6 Parameter Groups...
Page 82: ...74 NOTES 6 S4 Parameter Groups...
Page 83: ...75 7 Parameter Descriptions...
Page 149: ...141 8 Troubleshooting Maintenance...
Page 159: ...151 9 Motor Characteristics...
Page 162: ...154 9 MOTOR CHARACTERISTICS NOTES...
Page 163: ...155 10 Options...
Page 165: ...157 11 Appendices...