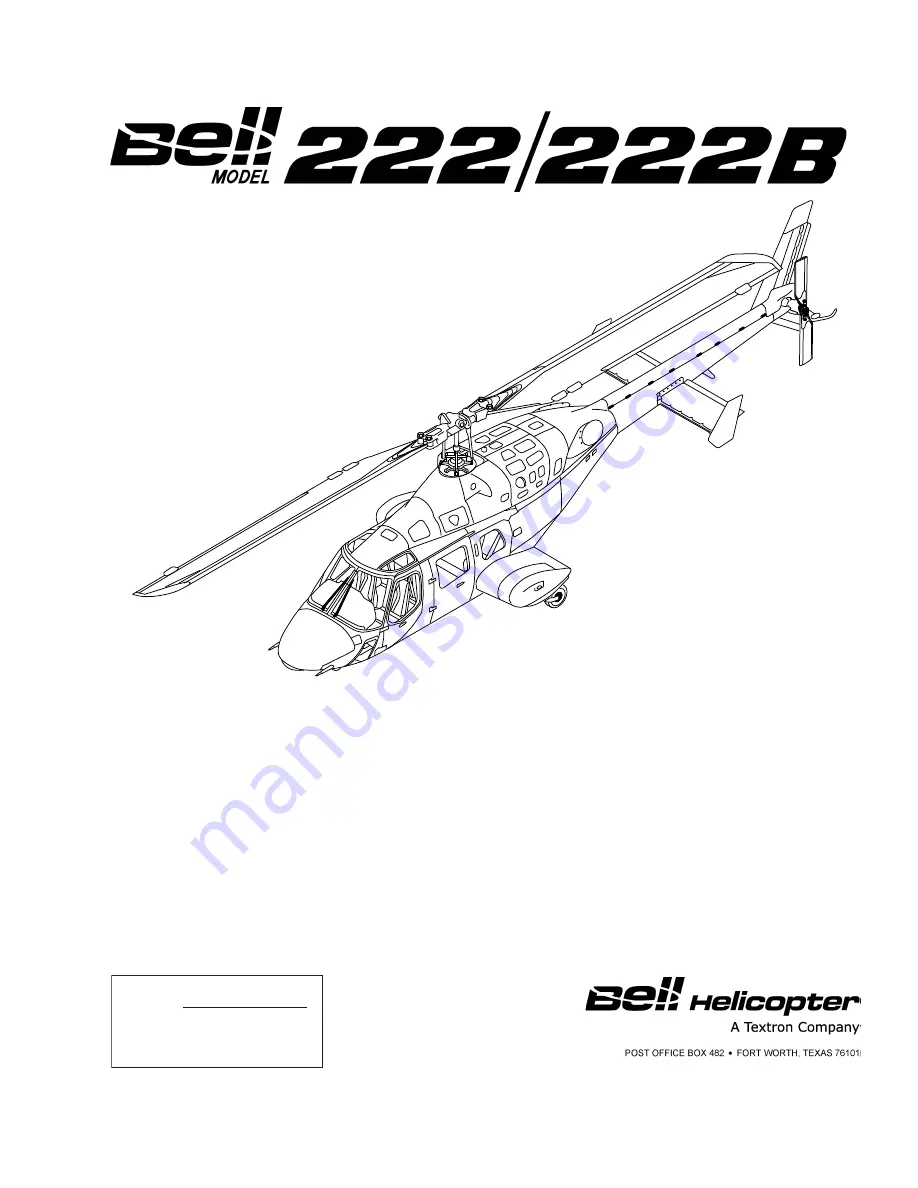
BHT-222/222B-MM-1
NOTICE
The instructions set forth in this manual, as supplemented or modified by Alert Service Bulletins (ASB) or
other directions issued by Bell Helicopter Textron Inc. and Airworthiness Directives (AD) issued by the
applicable regulatory agencies, shall be strictly followed.
REISSUE — 12 FEBRUARY 1998
REVISION 7 — 9 SEPTEMBER 2011
COPYRIGHT NOTICE
COPYRIGHT
2011
BELL ® HELICOPTER TEXTRON INC.
AND BELL HELICOPTER TEXTRON
CANADA LTD.
ALL RIGHTS RESERVED
MAINTENANCE MANUAL
VOLUME 1
GENERAL INFORMATION
Summary of Contents for 222
Page 6: ......
Page 12: ......
Page 13: ......
Page 14: ......
Page 15: ......
Page 16: ......
Page 17: ......
Page 18: ......
Page 24: ...BHT 222 222B MM 1 5 00 00 Page 6 Rev 7 9 SEP 2011 ECCN EAR99 Figure 5 1 Maintenance Zones ...
Page 26: ......
Page 48: ......
Page 60: ......
Page 66: ......
Page 70: ......
Page 74: ......
Page 80: ......
Page 84: ......
Page 106: ......
Page 108: ......
Page 110: ......
Page 118: ......
Page 120: ......
Page 122: ......
Page 126: ......
Page 128: ......
Page 132: ......
Page 136: ......
Page 138: ......
Page 140: ......
Page 142: ......
Page 144: ......
Page 146: ......
Page 148: ......
Page 150: ......
Page 154: ......
Page 156: ......
Page 158: ......
Page 166: ......
Page 174: ......
Page 180: ......
Page 186: ......
Page 190: ......
Page 196: ......