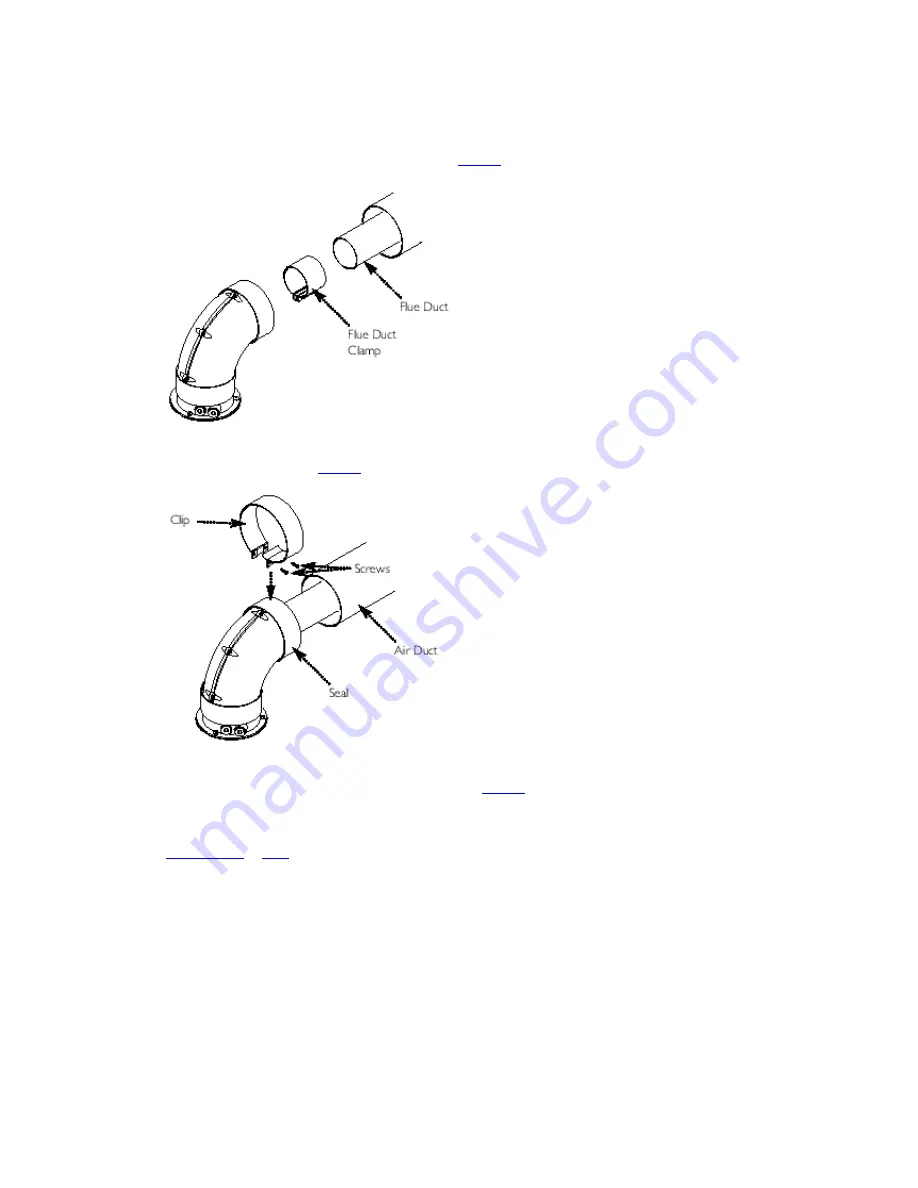
10. Refit the screws to the clip and tighten them to secure the elbow. Take the second rubber
seal and position it on the flue elbow.
11. Locate the flue duct clamp on the flue outlet elbow. Draw the flue duct out of the air duct,
engage it in the clamp and tighten the screws (
Fig. 22
).
Fig. 22
12. Draw the air duct out of the wall and align it with the elbow. Position the seal so that it
equally covers the joint (
Fig. 23
).
Fig. 23
13. Remove the screws from the second clip provided. Prise the clip apart and fit it over the
seal. Refit the screws to the clip and tighten them (
Fig. 23
).
14. Where possible position the clips so that the screws are not visible.
15. Make good between the wall and air duct outside the building.
16. Fit the circular flue trim outside if required, and if necessary fit a terminal guard (see
Section 7.10
&
7.11
).
8.7 Extensions & Additional Elbows
1. The method of connecting any flue extensions or additional elbows is the same as that for
connecting the standard flue and 90°elbow as described above.
2. If, for example, when a flue extension is connected to a 90°elbow the flue duct will project
from the air duct at the unconnected end by the same amount as the flue duct spigot does
from the elbow . Further elbows or extensions can then be added to this.
3. Similarly, a concentric flue can be connected to the boiler adaptor in the same manner as it
does to the elbow to provide a vertical flue.
4. The additional 90°elbow available is identical to the elbow supplied with the standard flue.
45°elbows are of the same principle.
5. Extensions can be cut according to the requirements of the installation.
Summary of Contents for 35/80 IE
Page 15: ...F 190mm G 143mm ...
Page 20: ...Fig 5 ...
Page 51: ......
Page 55: ......
Page 57: ......
Page 59: ......
Page 67: ...br brown bk black b blue r red g green g y green yellow w white Page 39 14 0 Fault Finding ...
Page 69: ...Page 40 Fault Finding Solutions Sections A to E ...
Page 70: ...Page 41 ...
Page 71: ......
Page 73: ......
Page 74: ......