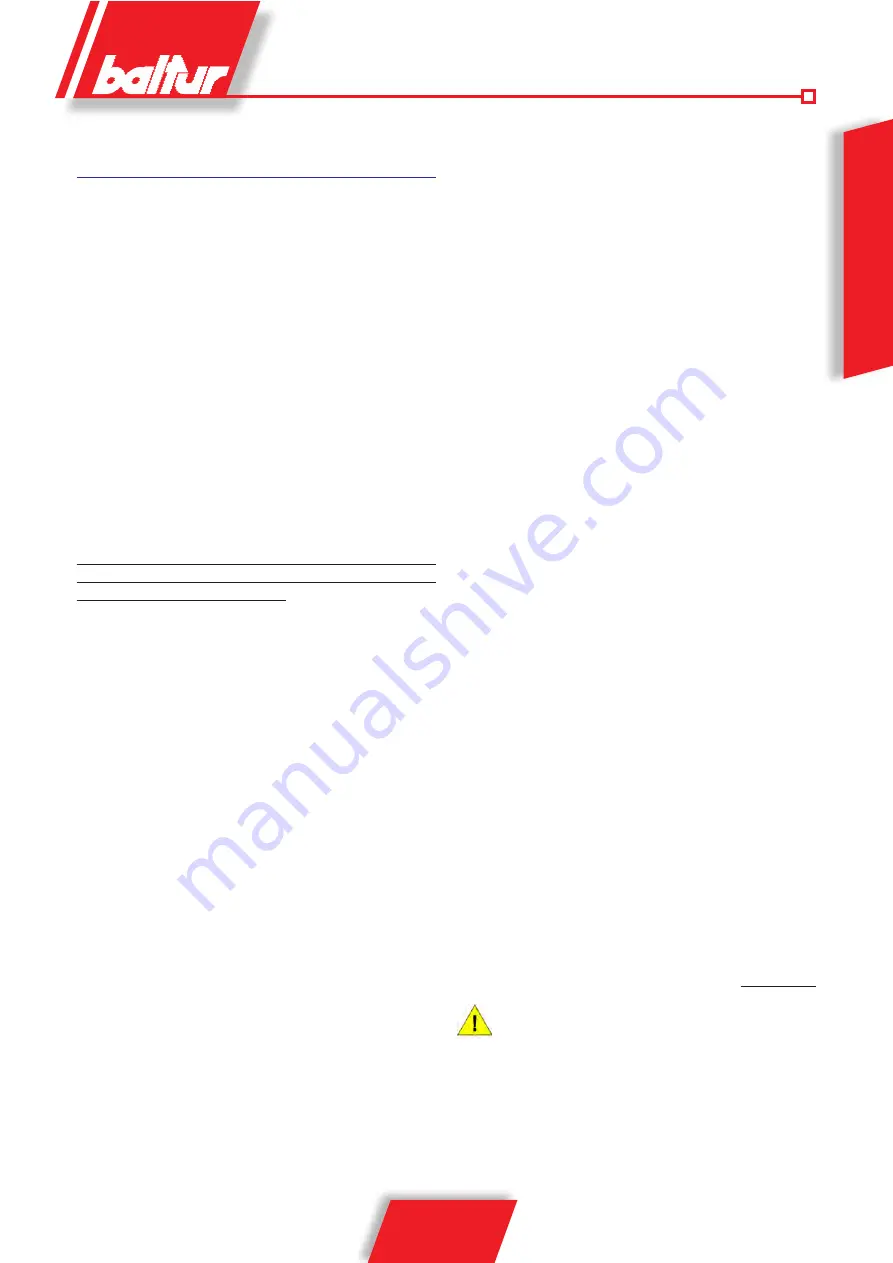
13 / 44
0006080118_201311
DESCRIPTION OF PROGRESSIVE TWO-
STAGE OPERATION WITH LIQUID FUEL
The term two-stage progressive operation indicates that transition
from the first to the second state (from minimum to maximum
operation) is progressive in terms of both amount of combustion
air let in and the amount of output fuel.
During the preheating stage of the fuel oil, voltage goes through
the pre-heater regulation thermostat and reaches the resistance
remote control switch coil.
The remote control switch activates and delivers current to the pre-heater
resistances that heat up the fuel oil that it contains.
The preheater's minimum thermostat closes when the temperature
reaches the value to which it is regulated.
The equipment activates only when the temperature inside the pre-
heater reaches the value at which the resistances turn off (opening of
the regulation thermostat contact), therefore, with the fuel oil inside
the pre-heater at maximum temperature.
The burner command and control device (cyclic relay) is therefore
activated by the pre-heater regulation thermostat as it excludes the
resistances deactivating the corresponding remote control switch.
The cyclic relay equipment carries out the ignition program by starting
the fan motor for the preventilation phase.
If the pressure of the air supplied by the fan is sufficient for turning on
the relative pressure switch, also the pump motor that precirculates
the hot oil in the burner pipes turns on.
From the pump, the oil reaches the preheater and crosses it, and
is heated at the foreseen temperature and exits through a filter to
reach the atomization unit.
The hot oil circulates inside the atomiser unit without coming out
of the nozzle since the passages towards the nozzle (delivery) and
nozzle (return) are closed. This closure is carried out by “closing
pins” applied to the ends of the rods.
These "pins" are pressed against the seats by strong springs placed
on the opposite end of the rods. The oil circulates and flows out of
the atomiser unit return, passing through the sump where the TRU
thermostat is activated. It arrives at the return pressure regulator,
goes through this and reaches the pump and from here is discharged
into the return. The above hot oil circulation takes place at a pressure
value that is a few bar higher than the minimum pressure setting for
the return pressure regulator (10 ÷ 12 bar). This oil preventilation
and precirculation phase has a specified duration.
This time may be extended (without limits in theory) because a
particular electric circuit does not permit continuing the ignition
program until the fuel temperature in the nozzle return pipe has
reached the value to which the TRU thermostat (nozzle return
thermostat) is set. This particular implementation does not permit
the fuel to cross the nozzle until the fuel itself reaches at least the
temperature to which the TRU thermostat is regulated. Normally, the
TRU thermostat is triggered within the normal preventilation time
(seconds). Otherwise, the fuel oil preventilation and precirculation
phases are extended until the TRU is activated.
TRU intervention, (sufficiently hot oil in circulation) allows the unit to
continue with the ignition sequence activating the ignition transformer
that supplies the electrodes with high voltage.
High voltage between the electrodes primes the electric spark for
ignition of the fuel/air mixture.
After the ignition spark, the equipment provides voltage to the magnet
that uses levers to draw back the two rods that shut-off the fuel flow
(delivery and return) to the nozzle. When the rods move back they
close the atomization unit internal passage (by-pass) bringing the
pump pressure to the nominal value of approx. 20 ÷ 22 bar. The
movement of the two rods from the closure seats makes it possible
for the fuel to enter the nozzle at the pump pressure at 20 ÷ 22 bar,
and exit from the nozzle in a suitable atomized state.
The return pressure, which determines delivery to the furnace, is
regulated by the return pressure regulator.
For the ignition flow rate (minimum output) this value is approx.
10 - 12 bar. The atomised fuel which exits the nozzle mixes with
the air provided by the fan and is ignited by the electrode spark.
The presence of the flame is detected by the UV photocell. The
programmer continues and exceeds the locked position, stops the
ignition and then activates the output regulation circuit (fuel/air).
The output regulation servomotor (fuel/air) controls the increase of
the contemporary output of fuel and combustion air. The increase in
the fuel output is determined by the variable profile disc that, when
turning, increases the compression of the return pressure regulator
spring, with consequent increase of both pressure and fuel output.
An increase in fuel delivery must correspond to an increase (of
adequate quantity) of combustion air.
This condition occurs during the first adjustment, by turning the
screws that vary the profile of the control disc that adjusts the
combustion air.
Fuel flow and, at the same time, combustion air flow, increase up
to maximum pressure (fuel pressure at return pressure regulator of
about 18 - 20 bar) if pressure at the pump is 20 - 22 bar.
The fuel and combustion air output remains at the maximum value
until the boiler temperature (or pressure in case of steam boiler)
approaches the value set in the thermostat (or pressure switch)
of the 2nd stage. The latter inverts the fuel/air output adjustment
servomotor direction to gradually reduce the fuel output and the
relevant combustion air to the minimum value. If also with minimum
fuel and combustion air output the maximum temperature (pressure
in case of steam boilers) is reached, the thermostat (pressure switch
for steam boilers), that completely stops the burner, triggers at the
value it is set to. As temperature (or pressure for steam boilers)
drops below the shut-down device's set point, the burner turns on as
described above. Upon standard operation the 2nd stage thermostat
(or pressure switch) detects boiler load variations and automatically
commands to the (fuel/air) adjustment servomotor to adapt the fuel
and relevant combustion air output.
Thus the delivery regulation system (fuel/air) reaches a balance
position corresponding to a fuel delivery and to its combustion air
delivery equal to the heat amount required by the boiler. Bear in mind
that the possible flow range, with good combustion, is approximately
from 1 to 1/3 of the max flow rate indicated on the ID plate.
The air pressure switch must be adjusted upon igniting
the burner according to the pressure value determined for
operation with the ignition flame.
ENGLISH
Summary of Contents for COMIST 180 DSPNM
Page 2: ......
Page 41: ...39 44 0006080118_201311 WIRING DIAGRAM ENGLISH ...
Page 42: ...40 44 0006080118_201311 ENGLISH ...
Page 43: ...41 44 0006080118_201311 ENGLISH ...
Page 44: ...42 44 0006080118_201311 ENGLISH ...
Page 45: ...43 44 0006080118_201311 ENGLISH MAIN TRAIN ...
Page 85: ...39 44 0006080118_201311 SCHÉMA ÉLECTRIQUE FRANÇAIS ...
Page 86: ...40 44 0006080118_201311 FRANÇAIS ...
Page 87: ...41 44 0006080118_201311 FRANÇAIS ...
Page 88: ...42 44 0006080118_201311 FRANÇAIS ...
Page 89: ...43 44 0006080118_201311 FRANÇAIS RAMPE PRINCIPALE ...
Page 129: ...39 44 0006080118_201311 ЭЛЕКТРИЧЕСКАЯ СХЕМА РУССКИЙ ...
Page 130: ...40 44 0006080118_201311 РУССКИЙ ...
Page 131: ...41 44 0006080118_201311 РУССКИЙ ...
Page 132: ...42 44 0006080118_201311 РУССКИЙ ...
Page 133: ...43 44 0006080118_201311 РУССКИЙ ГЛАВНАЯ РАМПА ...
Page 173: ...39 44 0006080118_201311 电路示意图 英語 ...
Page 174: ...40 44 0006080118_201311 英語 ...
Page 175: ...41 44 0006080118_201311 英語 ...
Page 176: ...42 44 0006080118_201311 英語 ...
Page 177: ...43 44 0006080118_201311 英語 主泵 ...
Page 179: ......