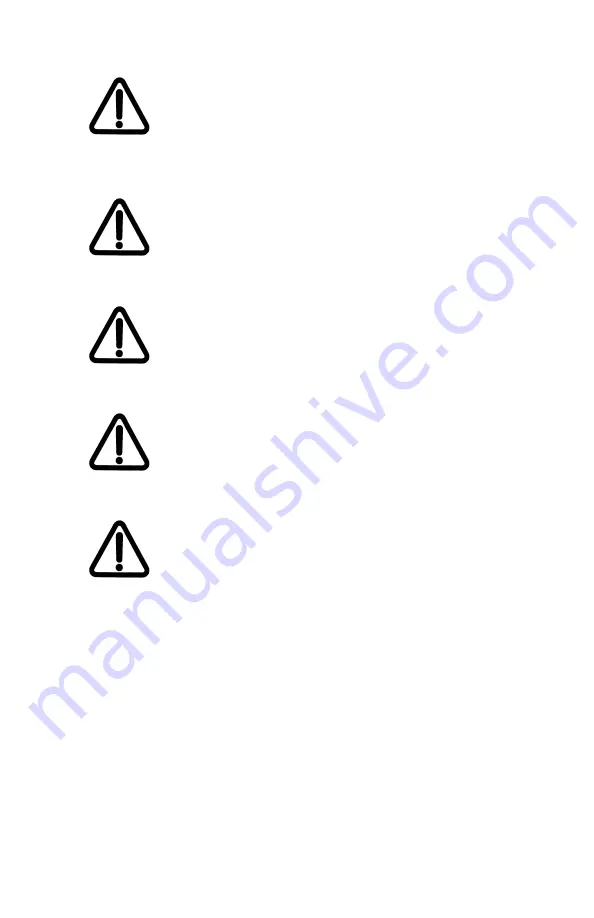
© 2018 Baker Hughes, a GE company, LLC. All rights reserved.
Masoneilan SVI II ESD Quick Start Guide
=
|
37
WARNING
EXPLOSION HAZARD - An improperly installed cover could leak
natural gas into the area.
The interior of the SVI II ESD is positively pressure with supply
medium. Appropriate safety measures must be taken to handle
pressurized natural gas that may enter the electrical conduit or
cable system.
WARNING
EXPLOSION HAZARD - A missing or improperly installed conduit
seal, cable seal, or cable gland could leak natural gas into the
conduit/cable system, and/or into any area where the conduit/
cabling system is present or connected to.
WARNING
Natural gas will constantly bleed and possibly vent from the SVI II
ESD if connected to a natural gas supply. Hazardous area
clarification is the responsibility of the end user. area ventilation
and other safety measures may be required to maintain a safe
environment.
WARNING
Installation in poorly ventilated confined areas, with any potential
of gases other than oxygen being present, can lead to a risk of
personnel asphyxiation.
WARNING
Isolate the valve from the process and disconnect air tubing from
the positioner. Disconnect air fully to avoid injury or process
damage.