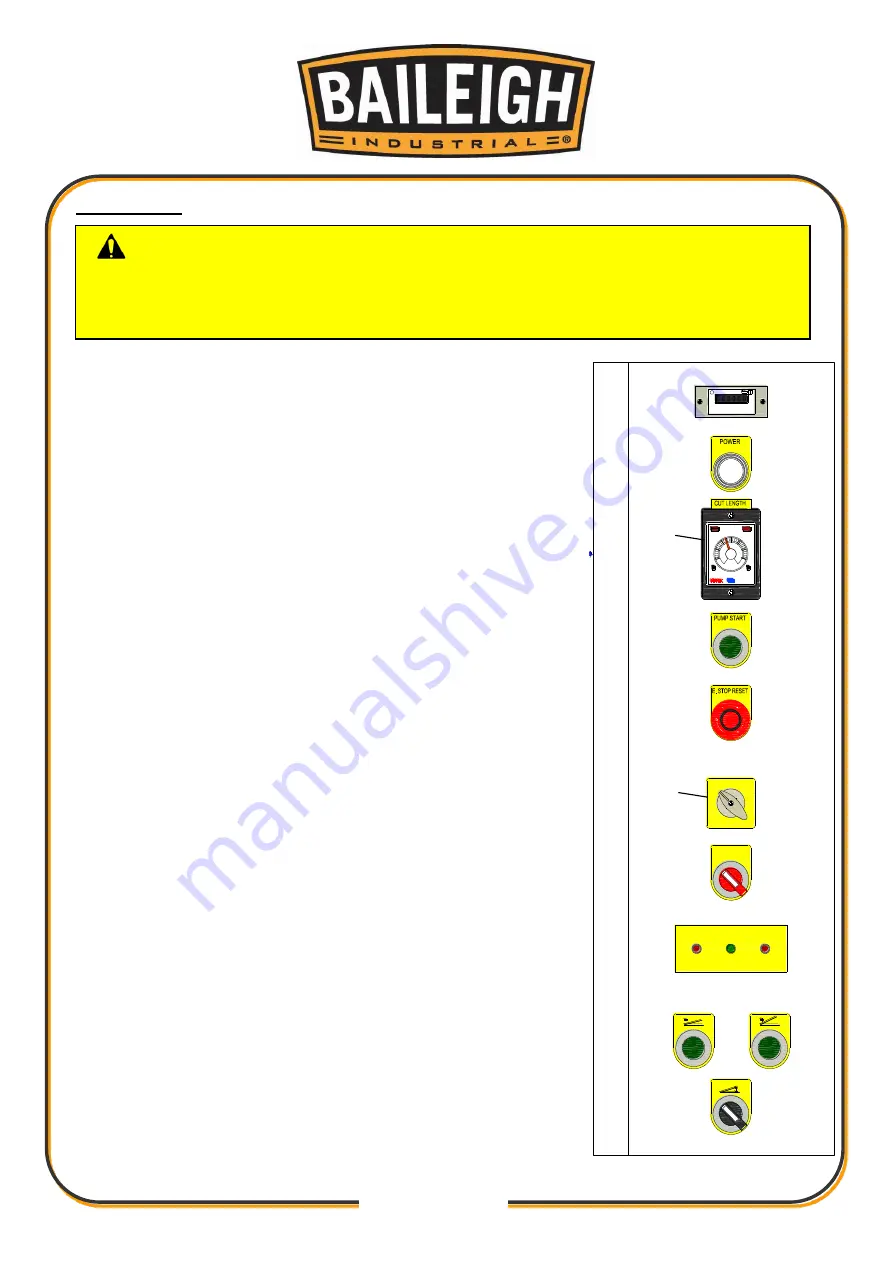
28
28
Single Mode
When performing a cut in the
SIN
mode, pressing the foot
pedal will complete one full shear cycle.
1. Place the 3-position selector switch (
E
) in the
SIN
(singular) position.
2. Clear the shear table.
3. Turn on the main power to start the machine.
4. Re-set the emergency stop button, and start the hydraulic
pump.
5. The upper blade will automatically rise to the upper limit.
6. Set the CUT LENGTH timer (
F
).
7. Load and position the material to be cut.
8. Check that the cutting area has only the material to be cut
and step down on the footswitch. The upper blade will
lower to cut the material and automatically return the
upper limit position. The blade will stop until the foot pedal
is released and pressed again.
9. The COUNTER will accumulate the number of strokes
automatically.
CAUTION:
Always wear proper eye protection with side shields, safety
footwear, and leather gloves to protect from burrs and sharp edges.
Keep hands and fingers clear of the shearing blade and clamping cylinders.
When handling large heavy sheets make sure they are properly supported.
0
0.5
1.0
1.5
2.0
2.5
3.0
X1
X10
S
M
UP
PW
TIMER
STPY-M3
SIN
INCH
AUTO
OFF
LAMP
ON
OFF
ON
MILD STEEL T.S 64000psi
20GA
10 GA
3/16"
28GA
10GA
STAINLESS T.S 100000psi
14 GA
HAUPTSCHALTER MAIN SWITCH
OFFNEN IN
0-STELLUNG
OPEN IN
OFF - POSITION
O
E
F
Summary of Contents for SH-8008HD
Page 19: ...16 16 GETTING TO KNOW YOUR MACHINE I D E H J K A C O O P...
Page 47: ...44 44 ELECTRICAL ENCLOSURE BACK PANEL...
Page 57: ...54 54 NOTES...
Page 58: ...55 55 NOTES...
Page 59: ...56 56 NOTES...